
De structuur van het TFT LCD-scherm
Vloeibaar kristalpaneel (paneel): Dit is het hoofdonderdeel van het display, verantwoordelijk voor het presenteren van het beeld. Het vloeibaar kristal paneel wordt gevormd door twee glasplaten met een laag vloeibaar kristal ertussen, bekend als de vloeibaar kristal cel.
Polarisatiefilters:Deze componenten bevinden zich aan beide zijden van de vloeibaar-kristalcel en zijn verantwoordelijk voor de verwerking van het licht dat door de cel gaat.
Kleurfilter: Meestal vervaardigd op een van de glasplaten van de verzegelde vloeibaar-kristalcel. Dit wordt gebruikt voor kleurenweergave.
Dunnefilmtransistorarray (TFT-array):Het is op de andere glasplaat van de verzegelde vloeibaar-kristalcel geplaatst en speelt een actieve rol bij de aansturing van het display.
Achtergrondverlichting:De lichtbron die zich achter de TFT-LCD-schermmodule bevindt, levert het licht dat nodig is om het zichtbare beeld via de vloeibaar-kristalcel te produceren.
Externe schijfschakeling:Deze circuits zijn verantwoordelijk voor het beheer van de invoerbeeldsignalen om de TFT-reeks en de achtergrondverlichting op de juiste manier aan te sturen.

Het productieproces van TFT LCD-schermen
Filmvorming:Met technieken als sputteren (SPT) en chemische dampdepositie (CVD) worden meerdere lagen op het substraat aangebracht.
Fotolithografie: Het aanbrengen, belichten en ontwikkelen van fotoresist om microstructuren te vormen.
Etsen:Natte en droge etsmethoden modelleren het substraat door specifieke gebieden te verwijderen.
Strippen:Na het aanbrengen van het patroon worden overtollige materialen verwijderd om het substraat te reinigen.
Hulpprocesstappen:
Schoonmaak:Zorgt ervoor dat het substraat vrij is van verontreinigingen.
Markering en blootstelling:Identificeert en bereidt de randen van het substraat voor.
Geautomatiseerde optische inspectie (AOI):Wordt gebruikt voor inspectie op defecten.
Microscopische inspectie en macroscopische inspectie (Mic/Mac):Gedetailleerde controle.
Filmprestatietesten:Maakt gebruik van hulpmiddelen zoals plaatweerstandsmeters, profilometers, reflectometers/ellipsometrie en Fourier-transformatie-infraroodspectroscopie.
Open/kortsluiting (O/S) elektrische test:Controleert op continuïteit van het circuit en kortsluitingen. Test Element Group (TEG) elektrische tests: test de elektrische prestaties van elementen.
Elektrische testen van arrays:Zorgt voor de elektrische functionaliteit van de array.
Laserreparatie:Corrigeert eventuele gebreken op basis van de inspectieresultaten.
Fotoresist-herbewerking (PR-herbewerking):Indien nodig worden de fotolithografiestappen aangepast of herhaald.
Filmbewerking: Verandert of perfectioneert indien nodig het filmvormingsproces.

OC-laag beschermt en bereidt de kleurfilterpatronen voor.
RGB-laag vorming via coating-, blootstellings- en ontwikkelingssequenties.
BM (Black Matrix) laag verbetert het contrast en beperkt lichtverlies.
PS (Photo Spacer)-laag zorgt voor een nauwkeurige afstand tussen de substraten, wat cruciaal is voor de beeldkwaliteit.
IT-laag voegt een transparante geleidende film toe voor elektrische geleiding en aanraakfunctionaliteit.

Polyimide (PI) Uitlijning en oriëntatie: Het aanbrengen en oriënteren van de PI-laag voor uitlijning van vloeibare kristallen.
ODF (Optische Display Film) verbetert visuele effecten.
Reiniging en aanbrengen van framekit: Voorbereiding voor het inbrengen van vloeibare kristallen druppels.
Vloeibaar kristal injectie: Het nauwkeurig doseren van het vloeibare kristal op het display.
TFT & CF-laminering: Het TFT- en CF-componenten aan elkaar verbinden.
UV-uitharding en thermische verwerking: Het vloeibare kristal wordt gestold en gelijkmatig verdeeld met behulp van ultraviolet licht en warmtebehandeling.
Snijden, elektrisch testen en randafwerking: Het vormen van het substraat, het uitvoeren van elektrische controles en het gladmaken van de randen.
Polarisatorbevestiging en ontluchting: Het aanbrengen van polariserende folies en het verwijderen van luchtbellen, eventueel met de mogelijkheid tot nabewerking.

Lasersnijden en elektrisch testen: Zorgt voor een nauwkeurige vorm en elektrische integriteit.
COG (Chip On Glass) Bonding, FPC (Flexible Printed Circuit) Bonding & Testen: Het installeren en testen van de aandrijfschakeling.
Montage en elektrische testen: Alle onderdelen van de displaymodule samenvoegen en de laatste elektrische tests uitvoeren.
Veroudering: Langdurige stroomvoorziening om de betrouwbaarheid van het product te garanderen.
Verpakking en verzending: Het gereedmaken van het eindproduct voor levering.

Array segmentstroom
G: De gate-isolator, gemaakt van SiNx (siliciumnitride), zorgt voor de nodige isolatie tussen de gate en de andere lagen.
I: De kanaallaag, a-Si (amorf silicium), waar de elektronische schakeling plaatsvindt.
N: De n+ a-Si-laag is gedoteerd met een hoge concentratie fosfine (PH3). Deze dotering vermindert de potentiaalbarrière bij de interface, waardoor een ohms contact wordt gegarandeerd, wat cruciaal is voor een betrouwbare werking van het apparaat.

Poortmetaal (AlNd/MoN)

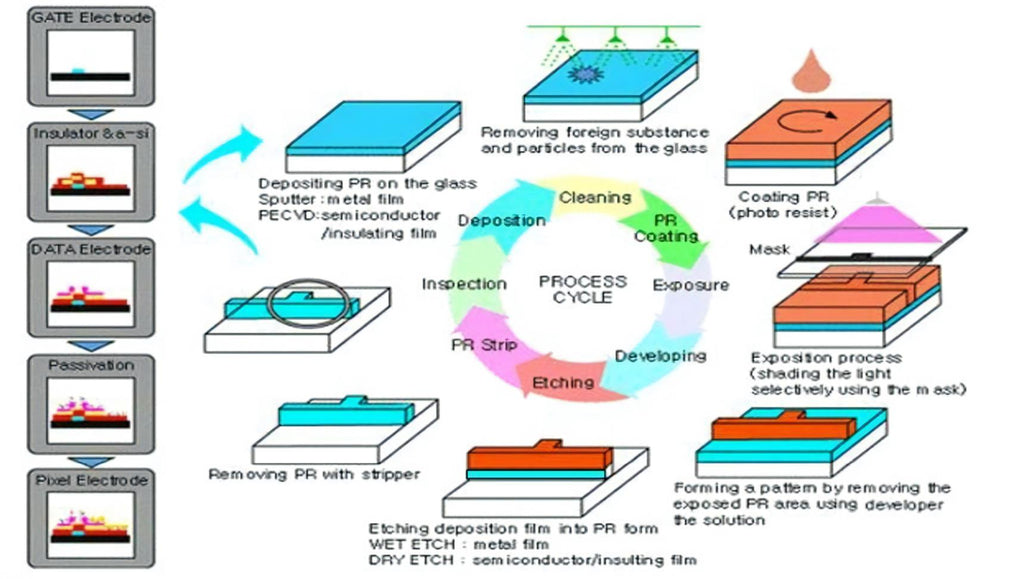
GIN (SiNx / a-Si / n+ a-Si)

S/D Metaal (Mo \Al\Mo)
De vorming van de bron- en afvoerelektroden (S/D), data-elektrode en kanaal omvat specifieke procedures zoals gelaagdheid met molybdeennitride (MoN) en zuiver aluminium (voor bron en afvoer), sputteren van de S/D-metaallaag, S/D-fotolithografie, S/D-nat etsen en kanaaldroog etsen. Door deze processen worden de bron- en afvoerelektroden, het kanaal en de datalijnen van de TFT gevormd op het glazen substraat. In dit stadium is de constructie van de TFT afgerond. Het resulterende ontwerp en proces zijn als volgt:
S/D-sputteren: Dit is een cruciale stap om source/drain-elektroden te vormen. Tijdens dit proces wordt een dichte laag metalen elektroden gevormd door zware metaalionen op het substraat te sputteren.
Reinigen voor PR-coating:Voordat u de fotolak aanbrengt, moet u het substraat reinigen om stof en resten te verwijderen. Zo verkrijgt u een goed coatingresultaat.
DHP (Hot Plate):Om de fotoresist beter aan het substraat te laten hechten, wordt het substraat voor het coatingproces voorverwarmd op een verwarmingsplaat.
Weerstandscoating: Breng een laag fotoresist aan op het voorverwarmde substraat, die vervolgens wordt gebruikt voor het aanbrengen van patronen.
Vooruitharden (SHP):Het met fotoresist gecoate substraat is voorgehard om de fotoresist gelijkmatiger en sterker te maken.
Stepper-blootstelling:In deze stap wordt de hoeveelheid licht gecontroleerd om bepaalde delen van de fotoresist te verharden en het gewenste patroon te creëren.
Ontwikkeling:De belichte fotoresist wordt verwerkt om het patroon zichtbaar te maken.
Fotoresist nabakken (HHP): Het fotoresistpatroon wordt verder gehard en prominenter gemaakt door een ander verwarmingsproces. Dit kan ook het vermogen om chemische corrosie en slijtage te weerstaan verbeteren.
Ontwikkelingsinspectie:Na de ontwikkeling is een gedetailleerde inspectie nodig om de nauwkeurigheid van het patroon te garanderen en eventuele problemen snel te detecteren en aan te pakken.
Natte ets:Dit is een chemisch reactieproces waarbij een bijtende vloeistof wordt gebruikt om het materiaal in de niet-beschermde gebieden te etsen om het circuitpatroon te vormen.
Kanaal droog etsen: Er wordt een kanaal gevormd tussen de source en de drain. In dit proces wordt het silicium in het kanaalgebied geëtst in de gewenste vorm met behulp van een droge etstechniek.
Weerstandsstrook:Ten slotte wordt de fotoresist op het substraat verwijderd om het oppervlak van het substraat te reinigen.
Na de bovenstaande stappen worden de source/drain-elektroden, de data-elektroden en het TFT-kanaal uiteindelijk op het glazen substraat gevormd.
Passivering (SiNx)
De vorming van de passiveringslaag (SiNx), vaak bekend als de beschermende isolatielaag, samen met de via's, omvat specifieke bewerkingen zoals PECVD-filmvorming, fotolithografie en droog etsen voor via-creatie. Na het doorlopen van deze procedures worden de beschermende isolatielaag voor het TFT-kanaal en de geleidende via's uiteindelijk gevormd op het glazen substraat. De afbeeldingen en het proces verkregen na het voltooien van deze stappen zijn als volgt:
2. Reiniging vóór de coating - Hier wordt het substraat gereinigd voordat de fotoresist wordt aangebracht.
3. Voorbakken op hete plaat (DHP) - Hierbij wordt een verwarmingsplaat gebruikt om het substraat voor te verwarmen ter voorbereiding op de coatingstap.
4. Fotoresistcoating - Tijdens deze fase wordt een laag fotoresist over het substraat aangebracht.
5. Zacht bakken (SHP) - Het substraat, bedekt met fotoresist, ondergaat een voorhardingsproces om de laag te laten stollen.
6. Stepper-blootstelling - Hierbij wordt gebruikgemaakt van de stepperlithografietechnologie om de fotoresist te belichten en patronen te vormen.
7. Ontwikkelen - De belichte fotoresist wordt verwerkt om het patroon zichtbaar te maken.
8. Hard bakken (HHP) - Het fotoresistpatroon wordt uitgehard door een nabakbehandeling.
9. Inspectie na ontwikkeling - In deze fase wordt het ontwikkelde substraat geïnspecteerd om de nauwkeurigheid van de patronen te bevestigen.
10. Nat etsen - Ongewenste dunne filmmaterialen worden verwijderd via een natchemisch etsproces om circuitpatronen te creëren.
11. Fotoresist strippen - De fotoresist wordt verwijderd en het oppervlak van het substraat wordt gereinigd.
12. Contactgat etsen (CH Etsen) - De benodigde via's worden gevormd door middel van een droog etsproces.
Dit zijn de gedetailleerde stappen die nodig zijn om het substraat voor TFT-toepassingen voor te bereiden, wat leidt tot de bescherming van het actieve TFT-kanaal en de vorming van geleidende via's.
Vorming van transparante pixelelektrode ITO (Indium-Tin-Oxide)
Het creëren van transparante pixelelektroden in TFT-schermen is een geavanceerd proces, dat begint met de afzetting van indium-tin-oxide (ITO). De betrokken fasen zijn nauwkeurig ontworpen en omvatten het sputteren van de ITO-laag om transparantie te bereiken, gevolgd door fotolithografie voor ingewikkelde patronen en afgesloten met nat etsen om de pixelstructuur te finaliseren. Deze nauwkeurige reeks eindigt met de vorming van de pixelelektroden, feilloos geïntegreerd op het glazen substraat, wat de cruciale voltooiing van het arrayproces markeert. De volgende workflow beschrijft de verfijning en volgorde van bewerkingen na voltooiing van het proces.
Pixellaagdepositie (ITO-sputteren) – Vormt een transparante geleidende film van ITO (Indium Tin Oxide) voor daaropvolgende pixelpatronen.
Reiniging van het substraat (reiniging van pre-resist coating) – Zorgt voor de zuiverheid van het substraat voordat het fotoresistmateriaal wordt aangebracht.
Voorverwarmen van substraat (Dehydration Hot Plate, DHP) – Bereidt het substraat voor met een voorbakstap voor optimale hechting van de fotoresist.
Weerstandstoepassing (coating) – Brengt een gelijkmatige fotoresistlaag aan op het substraat.
Zacht bakken (vooruitharden van SHP) – Voert voorharding uit om de fotoresist te laten stollen voordat het patroon wordt aangebracht.
Precisiebelichting (stappenbelichting) – Maakt gebruik van stepperfotolithografie om de fotoresist bloot te leggen en zo het gewenste patroon te creëren.
Patroonontwikkeling (Ontwikkelen) – Ontwikkelt de belichte fotoresist om het ingewikkelde pixelpatroon te onthullen.
Weerstand tegen verharding (nabelichting bakken, hard bakken HHP) – Verhardt de gepatroneerde fotoresist om de etsbestendigheid te verbeteren.
Patrooninspectie (inspectie na ontwikkeling) – Inspecteert de ontwikkelde patronen op nauwkeurigheid en integriteit.
Patroonoverdracht (ITO-etsen) – Brengt het patroon over door de ITO-laag te etsen om pixelelektroden te vormen.
Verwijderen van weerstand (strippen) – Verwijdert de fotoresist en laat een schoon substraatoppervlak achter.
Prestatieverbetering (gloeien) – Gloeit de componenten om de elektrische eigenschappen van de dunnefilmtransistors te verbeteren.
Kwaliteitscontrole (TEG-test) – Voert elektrische testen uit op testelementen om de kwaliteit tijdens de productie te bewaken.
Deze gestroomlijnde volgorde legt de basis voor hoogwaardige TFT-schermen met optimale elektrische prestaties.

Kleurfilter (CF)-proces
Glazen substraat: De fundamentele basislaag die mechanische ondersteuning biedt.
Zwarte Matrix (BM): Het is gemaakt van een lichtabsorberend materiaal, waardoor elke pixel wordt gemarkeerd en het lichtverlies tussen pixels wordt geminimaliseerd, wat het contrast verbetert.
Kleurharslagen: Als de werkelijke rode, groene en blauwe filters bepalen deze lagen de pixelkleuren. Ze zijn gemaakt van een geverfd transparant harsmateriaal.
Overjaslaag (OC): Een beschermende laag die over de gekleurde harsen wordt aangebracht om het oppervlak egaal te maken en de filters te beschermen tegen fysieke en chemische schade.
ITO (Indium Tin Oxide) Elektrode: Deze transparante geleidende laag zorgt ervoor dat het paneel als een elektrode functioneert en de hoeveelheid licht die erdoorheen gaat, reguleert.

Voorbereiding van het substraat: De reinheid van het glassubstraat is van het grootste belang. Daarom wordt het grondig gereinigd om onzuiverheden te verwijderen die de CF-kwaliteit in gevaar kunnen brengen.
Zwarte Matrix Vorming: Door een fotoresistlaag op het gereinigde substraat aan te brengen, wordt fotolithografie gebruikt om het BM-patroon te schetsen. Na belichting worden onontwikkelde gebieden onthuld en gevuld met zwart pigment, en vervolgens uitgehard.
Toepassing van kleurhars: Opeenvolgende toepassing van rode, groene en blauwe kleurharsen binnen de BM-grenzen wordt uitgevoerd met behulp van een afzonderlijk fotolithografieproces voor elke kleurlaag. Na het coaten en belichten worden de gebieden zonder fotoresist ontwikkeld en gevuld met de hars, gevolgd door uitharding.
Toepassing van de overlaaglaag: Er wordt een OC-laag aangebracht over de harskleuren om ze te beschermen en een glad oppervlak te creëren voor de daaropvolgende ITO-elektrodeafzetting.
ITO-elektrode-afzetting: De transparante ITO-elektrode wordt door middel van sputteren op de OC-laag aangebracht en vervolgens gepatroneerd om de elektrodearchitectuur te structureren.
Inspectie en testen: Gedurende de productie zorgen nauwkeurige inspecties en tests voor CF-kwaliteit. Metrieken zoals kleurechtheid, uniformiteit en defectniveaus worden grondig onderzocht.
Integratie: Na kwaliteitsborging wordt het kleurenfilter nauwkeurig uitgelijnd en gelamineerd met TFT-LCD-paneelcomponenten zoals de TFT-array en de vloeibaar-kristallaag.

CEL-segmentstroom
Het productieproces binnen het 'Cel'-aspect van een TFT-scherm kan grofweg worden onderverdeeld in vier belangrijke fasen: Uitlijning, Boxing, Snijden en Polarisatorbevestiging. De doelstellingen en primaire procedures van deze fasen worden als volgt kort geschetst:
Het uitlijningsproces
Het doel van het Alignment-proces is om een laag transparante PI (Polyimide) film te creëren op zowel de TFT- als CF-substraten. Door een daaropvolgend wrijvingsproces beïnvloedt deze laag de vloeibare kristalmoleculen om zich uit te lijnen in de richting van de wrijving. Voor een dieper begrip van de onderliggende principes, dienen geïnteresseerde lezers de relevante literatuur te raadplegen. Daarom bevat deze fase prominent twee primaire processen: PI Printing en Rubbing.
PI (Polyimide) Afdrukken
Polyimide (PI) is een hoogwaardig, transparant organisch polymeermateriaal dat bestaat uit hoofd- en zijketens. Na het aanbrengen en bakken hecht het stevig aan de oppervlakken van CF- en TFT-substraten. De coating van PI maakt gebruik van een speciale diepdruktechniek. Naast het primaire diepdrukproces omvat PI-printen verschillende hulpprocessen, waaronder substraatreiniging vóór het printen, voorbakken na het printen, automatische optische inspectie, uitharding en indien nodig een PI-herbewerkingsproces.
1. Reiniging vóór PI:Bij deze stap wordt het substraat grondig gereinigd voordat u gaat printen. Hierbij wordt ervoor gezorgd dat het vrij is van stof, vet en andere verontreinigingen, ter voorbereiding op de volgende stappen.
2.PI-afdrukkenHierbij wordt het PI (Polyimide) materiaal op het substraat aangebracht, vergelijkbaar met het printen van een ontwerp op papier. Alleen is de 'inkt' een speciaal materiaal dat een beschermlaag vormt.3. Voorbakken:Beschouw dit als een voorlopige bakfase, waarin de PI-laag gedeeltelijk droogt om een goede hechting aan het substraat te garanderen.
4.PI-inspectie:Op dit punt worden de geprinte lagen nauwkeurig onderzocht op vlekken, oneffenheden en defecten. Dit is vergelijkbaar met het inspecteren van een geverfde muur op onvolkomenheden.
5. PI-herwerking:Als er tijdens de inspectie problemen worden vastgesteld, worden deze onvolkomenheden in deze stap gecorrigeerd. Dit is vergelijkbaar met het uitgummen van fouten op een schets.
6.PI-uitharding:Tot slot wordt de PI-laag volledig uitgehard door middel van een bakproces, vergelijkbaar met het uitharden van klei in een oven, waardoor het sterk en duurzaam wordt.
Deze fase is gericht op het verwijderen van stof en deeltjes van het substraat met behulp van een ultrasoonreiniger, die ultrasone golven gebruikt voor grondige reiniging. Dit zorgt ervoor dat het substraat vrij is van verontreinigingen voordat u doorgaat naar de volgende stappen.
2. Uitlijning:
De uitlijningsfase past de oriëntatie van het substraat aan om aan de visuele vereisten te voldoen. Dit proces is eenvoudig en richt zich op het correct positioneren van het substraat voor daaropvolgende behandelingen.
3. Wrijven:
Tijdens de wrijffase wordt een fluwelen doek gebruikt om over de PI-laag te wrijven. Deze actie lijnt de zijketens van de PI uit in een uniforme richting, waardoor de moleculaire structuur wordt georganiseerd om de gewenste oppervlakte-eigenschappen te bereiken.
4. Ultrasoon reinigen na het wrijven (USC):
Na het wrijven kan het substraat deeltjes of resten bevatten. De USC-reiniging na het wrijven verwijdert deze resten, waardoor het oppervlak van het substraat onberispelijk schoon is. Deze stap is cruciaal voor het behoud van de kwaliteit van het eindproduct, omdat het ultrasone golven gebruikt om alle deeltjes of resten die tijdens het wrijven zijn blijven kleven, los te maken en te verwijderen.

ODF (One Drop Fill) encapsulatieproces
1. Aanbrengen van kit en zilverpasta:UV-uithardende lijm wordt gebruikt als afdichtingsmiddel, aangebracht langs de randen van de CF- en TFT-glassubstraten, om ervoor te zorgen dat de twee substraten stevig aan elkaar vastzitten en om de dikte van de cel te definiëren. Tegelijkertijd wordt zilverpasta aangebracht om de gemeenschappelijke elektroden op CF en TFT te verbinden om elektrische connectiviteit te garanderen.
2. Vloeibaar kristalcoating:Vloeibaar kristalmateriaal wordt op het TFT-substraat gedruppeld dat al is gecoat met de kit. Het vloeibaar kristalmateriaal speelt een cruciale rol in het weergaveproces; het past de toestand van het licht dat erdoorheen gaat aan door de opstelling ervan te veranderen, waardoor de kleur en helderheid van pixels wordt geregeld.
3. Vacuümverbinding:Het CF-substraat, dat is gecoat met de kit, zilverpasta en vloeibaar kristal, wordt in een vacuümomgeving met het TFT-substraat verbonden. Deze stap helpt de vorming van bellen te voorkomen en zorgt ervoor dat er een strakke, gapless verbinding is tussen de twee substraten.
Thermische uitharding:Nadat de UV-uitharding is voltooid, ondergaan de substraten een thermisch proces om de hechting van de kit verder te versterken. Deze stap is met name gericht op gebieden die niet volledig worden bereikt door UV-licht, zoals onder de leidingen, om ervoor te zorgen dat deze onderdelen grondig worden uitgehard.

1.Snijden
Vanwege de specifieke grootte van het glassubstraat en de verscheidenheid in productgroottes, worden meerdere productcellen op één glassubstraat gerangschikt. Het snijden wordt uitgevoerd door een diamantwiel over het glasoppervlak te schuiven. Er is doorgaans een debondingproces na het snijden, maar met de vooruitgang in de snijwieltechnologie is er nu een techniek die een zeer diepe snijmarkering creëert, waardoor de noodzaak voor debonding vervalt.
2. Randafwerking
Nadat het glas in afzonderlijke schermen is gesneden, hebben de randen van elk scherm veel fijne barsten. Om te voorkomen dat deze barsten breuk veroorzaken door botsingen bij latere verwerking, is een randbehandeling noodzakelijk.
3. Elektrische meting
Elektrische meting is een hulpproces dat meerdere keren tijdens de productie wordt gebruikt, maar het is hier vooral cruciaal omdat dit de eerste keer is dat elektriciteit wordt toegepast om de weergaveprestaties van het LCD-scherm te testen. Het testprincipe is eenvoudig: pas elektriciteit toe op afzonderlijke weergavepixels en observeer de weergaveprestaties van de cel via een polariserende film. Meestal wordt een korte balk die wordt gebruikt voor arraytesten geëlektrificeerd. Na elektrische tests worden schermen die niet aan de normen voldoen, verwijderd om verspilling van materialen in latere stadia te voorkomen.
Aanvullende ondersteunende processen zijn onder meer visuele inspectie na het snijden en reiniging na het afwerken.
TFT-schermmodule-assemblageproces
De primaire processen die betrokken zijn bij de assemblage van TFT-displaymodules omvatten de toepassing van de polariserende film, COG & FPC-binding, assemblage en verschillende ondersteunende processen. Hieronder vindt u een gedetailleerde introductie van elk:
1.COG- en FPC-binding
COG (Chip on Glass) en FPC (Flexible Printed Circuit) vertegenwoordigen methoden om circuits te verbinden. Vanwege de veelheid aan elektroden zijn traditionele één-op-één draadverbindingen een uitdaging. De huidige praktijk omvat het vormen van een elektrode-array op het glas, met een overeenkomstige array op de IC/FPC, en het gebruiken van Anisotropic Conductive Film (ACF) om elke IC/FPC-elektrode één voor één met de glaselektrode te verbinden.2. Het aanbrengen van de polariserende film
Omdat LCD-werking gebaseerd is op gepolariseerd licht, is het aanbrengen van een polariserende film een essentieel proces. Deze film regelt het licht dat door de vloeibaar-kristalcellen gaat om beelden te produceren.
3.Montage
Assemblage brengt de achtergrondverlichting, het scherm, het besturingscircuitbord en andere componenten zoals touchscreens samen om een complete displaymodule te vormen. Dit wordt doorgaans handmatig gedaan door bekwame technici, die een cruciale rol spelen bij het waarborgen van de kwaliteit van de geassembleerde modules.
Naast de hoofdprocessen omvat het modulesegment verschillende hulpprocessen, zoals:
1.Lasersnijden en elektrische meting na het snijden
Nadat de componenten nauwkeurig met een laser zijn gesneden, worden hun elektrische functies getest om er zeker van te zijn dat ze aan de vereiste specificaties voldoen.2. Elektrische meting van bonding en post-bonding
Na de COG- en FPC-verbindingsprocessen worden ook elektrische tests uitgevoerd om de integriteit van deze verbindingen te verifiëren.
3.Microscopische inspectie
Na het lasersnijden en lijmen worden microscopische inspecties (of automatische optische inspectie (AOI) voor FPC-lijmen) uitgevoerd om te controleren op defecten of problemen.
4. Test op pelsterkte
Na IC- en FPC-binding worden er pelsterktetesten uitgevoerd om de duurzaamheid van de bindingen te evalueren.
5. Veroudering na montage
De geassembleerde modules ondergaan een verouderingsproces waarbij stroom wordt toegepast om de betrouwbaarheid op lange termijn te garanderen.
6. Verpakking en verzending
Zodra de modules alle tests en inspecties hebben doorstaan, worden ze verpakt en verzonden naar de klant of naar de volgende productiefase.

Laatste artikelen
-
OLED Technology 2025: Ultimate Guide, Price Analysis, and Future Trends
OLED Technology 2025: Ultimate Guide, Price Analysis, and Future Trends