
Struktur layar TFT LCD
Panel Kristal Cair (Panel): Ini adalah bagian utama dari layar, yang bertanggung jawab untuk menampilkan gambar. Panel kristal cair dibentuk oleh dua pelat kaca dengan lapisan kristal cair yang diapit di antara keduanya, yang dikenal sebagai sel kristal cair.
Filter polarisasi:Komponen-komponen ini terletak di kedua sisi sel kristal cair dan bertugas memproses cahaya yang melewati sel.
Filter Warna: Biasanya dibuat pada salah satu pelat kaca sel kristal cair tertutup, ini digunakan untuk tampilan warna.
Rangkaian Transistor Film Tipis (Rangkaian TFT): Diposisikan pada pelat kaca lain dari sel kristal cair yang disegel, ia memainkan peran aktif dalam menggerakkan tampilan.
Lampu latar:Sumber cahaya yang terletak di belakang modul tampilan TFT-LCD menyediakan cahaya yang diperlukan agar gambar tampak dapat dihasilkan melalui sel kristal cair.
Sirkuit Penggerak Eksternal:Rangkaian ini bertugas mengelola sinyal gambar masukan untuk menggerakkan susunan TFT dan lampu latar secara tepat.

Proses pembuatan layar LCD TFT
Pembentukan Film:Teknik seperti Sputtering (SPT) dan Chemical Vapor Deposition (CVD) menghasilkan beberapa lapisan pada substrat.
Fotolitografi: Mengaplikasikan, memaparkan, dan mengembangkan photoresist untuk membentuk mikrostruktur.
Etsa: Metode etsa basah dan kering memahat substrat dengan menghilangkan area tertentu.
Pengupasan: Setelah pola dibuat, bahan yang berlebih dibuang untuk membersihkan substrat.
Langkah-langkah proses tambahan:
Pembersihan:Memastikan substrat bebas dari kontaminasi.
Penandaan dan Pemaparan:Mengidentifikasi dan mempersiapkan tepi substrat.
Inspeksi Optik Otomatis (AOI):Digunakan untuk pemeriksaan cacat.
Inspeksi Mikroskopis dan Inspeksi Makroskopis (Mic/Mac):Pemeriksaan detail.
Pengujian Kinerja Film:Menggunakan peralatan seperti meteran resistansi lembaran, profilometer, reflektometer/elipsometri, spektroskopi inframerah transformasi Fourier.
Pengujian Listrik Terbuka/Pendek (O/S):Memeriksa kontinuitas sirkuit dan hubungan arus pendek. Pengujian Listrik Kelompok Elemen Uji (TEG): Menguji kinerja kelistrikan elemen.
Pengujian Listrik Array:Memastikan fungsionalitas kelistrikan array.
Perbaikan Laser:Memperbaiki segala cacat berdasarkan hasil pemeriksaan.
Pengerjaan Ulang Photoresist (Pengerjaan Ulang PR):Menyesuaikan atau mengulangi langkah fotolitografi jika diperlukan.
Pengerjaan Ulang Film: Mengubah atau menyempurnakan proses pembentukan film jika diperlukan.

Lapisan OC melindungi dan mempersiapkan pola filter warna.
Lapisan RGB pembentukan melalui tahapan pelapisan, pemaparan, dan pengembangan.
Lapisan BM (Matriks Hitam) meningkatkan kontras dan membatasi kebocoran cahaya.
Lapisan PS (Pengatur Jarak Foto) mempertahankan jarak yang tepat antara substrat, penting untuk kualitas gambar.
Lapisan TI menambahkan film konduktif transparan untuk konduksi listrik dan fungsi sentuhan.

Penjajaran & Orientasi Polimida (PI): Menerapkan dan mengarahkan lapisan PI untuk penyelarasan kristal cair.
ODF (Film Tampilan Optik) meningkatkan efek visual.
Pembersihan dan Aplikasi Sealant Bingkai: Mempersiapkan penyisipan tetesan kristal cair.
Injeksi Kristal Cair:Menyalurkan kristal cair secara tepat pada layar.
Laminasi TFT & CF:Mengikat komponen TFT dan CF bersama-sama.
Pengeringan UV dan Pemrosesan Termal: Memadat dan mendistribusikan kristal cair secara merata dengan sinar ultraviolet dan perlakuan panas.
Pemotongan, Pengujian Listrik, & Perataan Tepi: Membentuk substrat, melakukan pemeriksaan kelistrikan, dan menghaluskan tepi.
Pemasangan Polarizer & Pembersihan: Menerapkan film polarisasi dan menghilangkan gelembung udara, dengan pengerjaan ulang diperbolehkan jika diperlukan.

Pemotongan Laser & Pengujian Listrik: Memastikan bentuk yang tepat dan integritas kelistrikan.
Pengikatan COG (Chip On Glass), Pengikatan & Pengujian FPC (Flexible Printed Circuit): Memasang dan menguji sirkuit penggerak.
Perakitan & Pengujian Listrik: Menggabungkan semua bagian modul tampilan dan melakukan uji kelistrikan akhir.
Penuaan: Pasokan daya jangka panjang untuk memastikan keandalan produk.
Pengemasan & Pengiriman: Mempersiapkan produk jadi untuk pengiriman.

Aliran segmen array
G: Isolator gerbang, terbuat dari SiNx (Silikon Nitrida), menyediakan isolasi yang diperlukan antara gerbang dan lapisan lainnya.
I: Lapisan saluran, a-Si (Silikon amorf), tempat terjadinya peralihan elektronik.
N: Lapisan n+ a-Si didoping dengan konsentrasi tinggi Fosfin (PH3). Doping ini mengurangi penghalang potensial pada antarmuka, memastikan kontak Ohmik yang sangat penting untuk pengoperasian perangkat yang andal.

Logam Gerbang (AlNd/MoN)

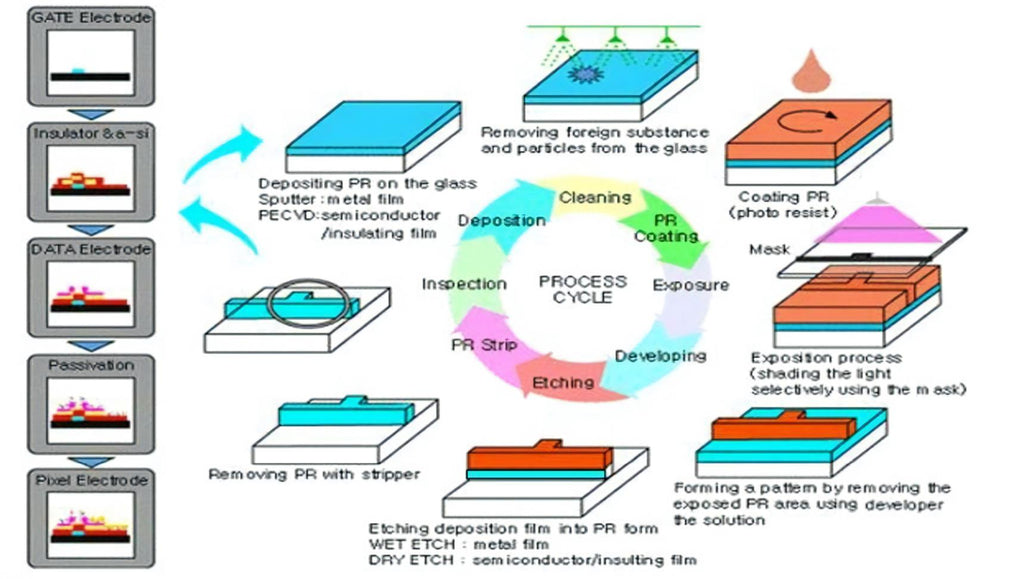
GIN (SiNx / a-Si / n+ a-Si)

Logam S/D (Mo\Al\Mo)
Pembentukan elektroda sumber dan drain (S/D), elektroda data, dan saluran mencakup prosedur khusus seperti pelapisan dengan Molibdenum Nitrida (MoN) dan Aluminium murni (untuk sumber dan drain), sputtering lapisan logam S/D, fotolitografi S/D, etsa basah S/D, dan etsa kering saluran. Melalui proses ini, elektroda sumber dan drain, saluran, dan jalur data TFT terbentuk pada substrat kaca. Pada tahap ini, konstruksi TFT selesai. Desain dan proses yang dihasilkan adalah sebagai berikut:
S/D Menyemprotkan: Ini adalah langkah penting untuk membentuk elektroda sumber/drainase. Selama proses ini, lapisan elektroda logam yang padat dibentuk dengan menyemprotkan ion logam berat ke substrat.
Pembersihan sebelum Pelapisan PR: Sebelum mengaplikasikan photoresist, substrat harus dibersihkan untuk menghilangkan debu dan residu, guna memastikan hasil pelapisan yang baik.
DHP (Pelat Panas): Untuk melekatkan photoresist pada substrat dengan lebih baik, substrat dipanaskan terlebih dahulu di atas pelat panas sebelum proses pelapisan.
Pelapis Tahan: Oleskan lapisan photoresist ke substrat yang telah dipanaskan terlebih dahulu, yang digunakan untuk pola selanjutnya.
Pra-pengerasan (SHP): Substrat yang dilapisi photoresist diawetkan terlebih dahulu untuk membuat photoresist lebih seragam dan kuat.
Paparan Stepper: Pada langkah ini, jumlah paparan cahaya dikontrol untuk mengeraskan area tertentu pada photoresist dan menciptakan pola yang diinginkan.
Berkembang: Photoresist yang terekspos diproses untuk memperlihatkan polanya.
Pasca Pemanggangan Fotoresist (HHP): Pola photoresist semakin diperkeras dan dibuat lebih menonjol melalui proses pemanasan lainnya. Hal ini juga dapat meningkatkan kemampuannya untuk menahan korosi dan keausan kimia.
Mengembangkan Inspeksi:Setelah berkembang, pemeriksaan terperinci diperlukan untuk memastikan keakuratan pola dan segera mendeteksi serta mengatasi masalah apa pun.
Etsa Basah: Ini adalah proses reaksi kimia di mana cairan korosif digunakan untuk mengukir material di area yang tidak terlindungi untuk membentuk pola sirkuit.
Saluran Etching Kering: Sebuah saluran terbentuk antara sumber dan saluran pembuangan. Dalam proses ini, silikon di wilayah saluran diukir ke dalam bentuk yang diinginkan menggunakan teknik etsa kering.
Tahan Strip: Terakhir, untuk membersihkan permukaan substrat, photoresist pada substrat dilepaskan.
Setelah langkah-langkah di atas, elektroda sumber/drainase, elektroda data, dan saluran TFT akhirnya dibentuk pada substrat kaca.
Pasivasi (SiNx)
Pembentukan lapisan pasivasi (SiNx), yang sering dikenal sebagai lapisan insulasi pelindung, beserta vias, mencakup operasi khusus seperti pembentukan film PECVD, fotolitografi, dan etsa kering untuk pembuatan vias. Setelah melalui prosedur ini, lapisan insulasi pelindung untuk saluran TFT dan vias konduktif akhirnya terbentuk pada substrat kaca. Gambar dan proses yang diperoleh setelah penyelesaian langkah-langkah ini adalah sebagai berikut:
2. Pembersihan Pra-Pelapisan - Di sinilah substrat dibersihkan sebelum aplikasi photoresist.
3. Panggangan Panas (DHP) - Ini melibatkan penggunaan hotplate untuk memanaskan terlebih dahulu substrat guna mempersiapkan langkah pelapisan.
4. Pelapisan Photoresist - Lapisan photoresist diaplikasikan di atas substrat selama tahap ini.
5. Panggang Lembut (SHP) - Substrat yang dilapisi dengan photoresist menjalani proses pra-pengerasan untuk memadatkan lapisan tersebut.
6. Paparan Stepper - Di sini, teknologi litografi stepper digunakan untuk memaparkan photoresist dan membentuk pola.
7. Mengembangkan - Photoresist yang terekspos diproses untuk memperlihatkan polanya.
8. Panggang Keras (HHP) - Pola photoresist dikeraskan melalui perawatan pasca-pemanggangan.
9. Inspeksi Pasca Pengembangan Tahap ini melibatkan pemeriksaan substrat yang dikembangkan untuk memastikan keakuratan pola.
10. Etsa Basah - Bahan film tipis yang tidak diinginkan dihilangkan melalui proses etsa kimia basah untuk membuat pola sirkuit.
11. Pelepasan Fotoresist - Photoresist dilepaskan dan permukaan substrat dibersihkan.
12. Penggoresan Lubang Kontak (CH Etching) - Vias yang diperlukan dibentuk melalui proses etsa kering.
Ini adalah langkah-langkah terperinci yang terlibat dalam menyiapkan substrat untuk aplikasi TFT, yang mengarah pada perlindungan saluran TFT aktif dan pembentukan via konduktif.
Pembentukan elektroda piksel transparan ITO (Indium-Tin-Oxide)
Pembuatan elektroda piksel transparan dalam tampilan TFT merupakan proses yang canggih, dimulai dengan pengendapan Indium-Tin-Oxide (ITO). Tahapan yang terlibat direkayasa secara presisi dan meliputi penyemprotan lapisan ITO untuk mencapai transparansi, diikuti oleh fotolitografi untuk pembuatan pola yang rumit, dan diakhiri dengan pengetsaan basah untuk menyelesaikan struktur piksel. Urutan yang cermat ini diakhiri dengan pembentukan elektroda piksel, yang terintegrasi dengan sempurna ke substrat kaca, yang menandai penyelesaian penting dari proses array. Alur kerja berikut merinci penyempurnaan dan urutan operasi pasca-penyelesaian proses.
Deposisi Lapisan Piksel (ITO Sputtering) – Membentuk lapisan konduktif transparan ITO (Indium Tin Oxide) untuk pola piksel selanjutnya.
Pembersihan Substrat (Pembersihan Lapisan Pra-Resist) – Memastikan kemurnian substrat sebelum menerapkan bahan photoresist.
Pemanasan Awal Substrat (Pelat Panas Dehidrasi, DHP) – Mempersiapkan substrat dengan langkah pra-panggang untuk daya rekat photoresist yang optimal.
Aplikasi Tahan (Pelapisan) – Menerapkan lapisan photoresist yang seragam pada substrat.
Soft Bake (Pra-pengerasan SHP) – Melakukan pra-pengerasan untuk memadatkan photoresist sebelum pembuatan pola.
Eksposur Presisi (Eksposur Stepper) – Memanfaatkan fotolitografi stepper untuk memaparkan photoresist, sehingga tercipta pola yang diinginkan.
Pengembangan Pola (Pengembangan) – Mengembangkan photoresist yang terekspos untuk memperlihatkan pola piksel yang rumit.
Tahan Pengerasan (Panggang Pasca-paparan, Panggang Keras HHP) – Memperkeras photoresist berpola untuk meningkatkan ketahanan terhadap goresan.
Pemeriksaan Pola (Pemeriksaan Pasca Pengembangan) – Memeriksa pola yang dikembangkan untuk akurasi dan integritas.
Transfer Pola (Etching ITO) – Mentransfer pola melalui pengetsaan lapisan ITO untuk membentuk elektroda piksel.
Pelepasan Resist (Strip) – Melepas photoresist, meninggalkan permukaan substrat yang bersih.
Peningkatan Kinerja (Annealing) – Anil komponen untuk meningkatkan sifat kelistrikan transistor film tipis.
Kontrol Kualitas (Uji TEG) – Melakukan uji kelistrikan pada elemen uji untuk memantau kualitas selama produksi.
Urutan yang disederhanakan ini meletakkan dasar untuk tampilan TFT berkualitas tinggi dengan kinerja kelistrikan yang optimal.

Proses Filter Warna (CF)
Substrat Kaca: Lapisan dasar fundamental yang memberikan dukungan mekanis.
Matriks Hitam (BM): Terbuat dari bahan penyerap cahaya, ia menggambarkan setiap piksel dan meminimalkan kebocoran cahaya antar piksel, sehingga meningkatkan kontras.
Lapisan Resin Warna: Seperti filter berwarna merah, hijau, dan biru yang sebenarnya, lapisan ini menentukan warna piksel. Lapisan ini dibuat dari bahan resin transparan yang diwarnai.
Lapisan Mantel (OC): Lapisan pelindung yang dilapisi pada resin warna untuk meratakan permukaan dan melindungi filter dari kerusakan fisik dan kimia.
Elektroda ITO (Indium Tin Oxide): Lapisan konduktif transparan ini memungkinkan panel berfungsi sebagai elektroda, mengatur cahaya yang melewatinya.

Persiapan Substrat: Kebersihan substrat kaca merupakan hal terpenting, sehingga harus dibersihkan secara menyeluruh untuk menghilangkan kotoran yang dapat menurunkan kualitas CF.
Pembentukan Matriks Hitam: Dengan mengaplikasikan lapisan photoresist ke substrat yang telah dibersihkan, fotolitografi digunakan untuk menguraikan pola BM. Setelah terpapar, area yang belum berkembang akan terlihat dan diisi dengan pigmen hitam, lalu diawetkan.
Aplikasi Resin Warna: Aplikasi resin warna merah, hijau, dan biru secara berurutan dalam batas BM dilakukan menggunakan proses fotolitografi yang berbeda untuk setiap lapisan warna. Setelah pelapisan dan pemaparan, area tanpa fotoresist dikembangkan dan diisi dengan resin, diikuti dengan pengerasan.
Aplikasi Lapisan Mantel: Lapisan OC diaplikasikan di atas warna resin untuk melindunginya dan menghasilkan permukaan halus untuk pengendapan elektroda ITO berikutnya.
Deposisi Elektroda ITO: Elektroda ITO yang transparan diendapkan secara sputter pada lapisan OC, lalu diberi pola untuk menyusun arsitektur elektroda.
Inspeksi dan Pengujian: Selama proses produksi, inspeksi dan pengujian yang cermat memastikan kualitas CF. Metrik seperti ketepatan warna, keseragaman, dan tingkat cacat diperiksa secara menyeluruh.
Integrasi: Pasca jaminan kualitas, Filter Warna disejajarkan dan dilaminasi secara tepat dengan komponen panel TFT-LCD seperti susunan TFT dan lapisan kristal cair.

Aliran Segmen SEL
Proses produksi dalam aspek 'Sel' pada layar TFT secara garis besar dapat dibagi menjadi empat tahap utama: Penyelarasan, Pengepakan, Pemotongan, dan Pemasangan Polarizer. Tujuan dan prosedur utama dari tahap-tahap ini diuraikan secara singkat sebagai berikut:
Proses Penyelarasan
Tujuan dari proses Alignment adalah untuk membuat lapisan film PI (Polyimide) yang transparan pada substrat TFT dan CF. Melalui proses gesekan berikutnya, lapisan ini memengaruhi molekul kristal cair agar sejajar dengan arah gesekan. Untuk pemahaman yang lebih mendalam tentang prinsip-prinsip yang mendasarinya, pembaca yang tertarik harus merujuk ke literatur yang relevan. Oleh karena itu, tahap ini secara mencolok menampilkan dua proses utama: PI Printing dan Rubbing.
Pencetakan PI (Polimida)
Polimida (PI) adalah bahan polimer organik transparan berkinerja tinggi yang terdiri dari rantai utama dan rantai samping. Setelah diaplikasikan dan dipanggang, bahan ini melekat kuat pada permukaan substrat CF dan TFT. Pelapisan PI menggunakan teknik cetak gravure khusus. Selain proses cetak gravure primer, pencetakan PI melibatkan beberapa proses tambahan termasuk pembersihan substrat sebelum pencetakan, pra-pemanggangan setelah pencetakan, inspeksi optik otomatis, pengawetan, serta proses pengerjaan ulang PI jika diperlukan.
1. Pembersihan Pra-PI:Langkah ini melibatkan pembersihan substrat secara menyeluruh sebelum mencetak, memastikan substrat bebas dari debu, minyak, dan kontaminan lain guna mempersiapkannya untuk langkah berikutnya.
2. Pencetakan PI:Di sini, bahan PI (Polimida) diaplikasikan ke substrat, analog dengan mencetak desain di atas kertas, kecuali 'tinta' adalah bahan khusus yang membentuk lapisan pelindung.3. Pra-Pemanggangan:Anggap ini sebagai fase pemanggangan awal, yang mengeringkan sebagian lapisan PI untuk memastikan daya rekat yang tepat pada substrat.
4. Inspeksi PI:Pada titik ini, lapisan cetakan akan menjalani pemeriksaan ketat untuk mengetahui adanya noda, area yang tidak rata, atau cacat, mirip seperti memeriksa ketidaksempurnaan pada dinding yang dicat.
5. Pengerjaan Ulang PI:Jika ada masalah yang teridentifikasi selama pemeriksaan, langkah ini memerlukan perbaikan atas ketidaksempurnaan tersebut, mirip dengan menghapus kesalahan pada sketsa.
6.Penyembuhan PI:Terakhir, lapisan PI dikeraskan sepenuhnya melalui proses pemanggangan, seperti tanah liat yang dikeraskan dalam tungku, menjadikannya kuat dan tahan lama.
Tahap ini bertujuan untuk menghilangkan debu dan partikel dari substrat menggunakan pembersih ultrasonik, yang menggunakan gelombang ultrasonik untuk pembersihan menyeluruh. Ini memastikan substrat bebas dari kontaminan apa pun sebelum melanjutkan ke langkah berikutnya.
2. Penyelarasan:
Tahap penyelarasan menyesuaikan orientasi substrat untuk memenuhi persyaratan visual. Proses ini mudah, dengan fokus pada penempatan substrat yang benar untuk perawatan selanjutnya.
3. Menggosok:
Selama tahap penggosokan, kain beludru digunakan untuk menggosok lapisan PI. Tindakan ini menyelaraskan rantai samping PI dalam satu arah, mengatur struktur molekuler untuk mencapai sifat permukaan yang diinginkan.
4. Pembersihan Ultrasonik Pasca-Gosok (USC):
Setelah digosok, substrat mungkin memiliki partikel atau residu. Pembersihan USC pasca-penggosokan menghilangkan residu ini, memastikan permukaan substrat bersih tanpa cela. Langkah ini penting untuk menjaga kualitas produk akhir, karena menggunakan gelombang ultrasonik untuk melepaskan dan menghilangkan partikel atau residu yang menempel selama proses penggosokan.

Proses Enkapsulasi ODF (One Drop Fill)
1. Aplikasi Sealant dan Pasta Perak:Perekat yang dapat diawetkan dengan sinar UV digunakan sebagai sealant, diaplikasikan di sepanjang tepi substrat kaca CF dan TFT, untuk memastikan bahwa kedua substrat terikat dengan kuat dan untuk menentukan ketebalan sel. Secara bersamaan, aplikasi pasta perak digunakan untuk menghubungkan elektroda umum pada CF dan TFT guna memastikan konektivitas listrik.
2. Pelapisan Kristal Cair:Material kristal cair diteteskan ke substrat TFT yang telah dilapisi dengan sealant. Material kristal cair memainkan peran penting dalam proses tampilan; material ini menyesuaikan kondisi cahaya yang lewat dengan mengubah susunannya, sehingga mengendalikan warna dan kecerahan piksel.
3. Ikatan Vakum:Substrat CF, yang telah dilapisi dengan sealant, pasta perak, dan kristal cair, diikat dengan substrat TFT dalam lingkungan vakum. Langkah ini membantu mencegah pembentukan gelembung dan memastikan adanya ikatan yang rapat dan tanpa celah antara kedua substrat.
Pengeringan Termal:Setelah proses pengeringan UV selesai, substrat menjalani proses termal untuk lebih memperkuat daya rekat sealant. Langkah ini khususnya ditujukan pada area yang tidak sepenuhnya terjangkau oleh sinar UV, seperti di bawah kabel, untuk memastikan bahwa bagian-bagian ini benar-benar kering.

1.Pemotongan
Karena ukuran substrat kaca yang pasti dan variasi ukuran produk, beberapa sel produk disusun pada substrat kaca tunggal. Pemotongan dilakukan dengan menggeser roda berlian melintasi permukaan kaca. Biasanya ada proses debonding setelah pemotongan, tetapi dengan kemajuan teknologi roda pemotong, sekarang ada teknik yang menciptakan tanda potong yang sangat dalam, sehingga menghilangkan kebutuhan untuk debonding.
2. Tepi
Setelah kaca dipotong menjadi layar individual, setiap tepi layar memiliki banyak retakan halus. Untuk mencegah retakan ini menyebabkan kerusakan karena benturan dalam penanganan selanjutnya, diperlukan perawatan tepi.
3.Pengukuran Listrik
Pengukuran listrik merupakan proses tambahan yang digunakan beberapa kali selama produksi, tetapi sangat penting di sini karena ini adalah pertama kalinya listrik digunakan untuk menguji kinerja layar LCD. Prinsip pengujiannya sederhana: gunakan listrik ke piksel layar individual dan amati kinerja layar sel melalui film polarisasi. Biasanya, batang pendek yang digunakan untuk pengujian array dialiri listrik. Setelah pengujian listrik, layar yang tidak memenuhi standar disingkirkan untuk mencegah pemborosan bahan pada tahap selanjutnya.
Proses tambahan tambahan mencakup pemeriksaan visual pasca pemotongan dan pembersihan pasca pembuatan tepi.
Proses Perakitan Modul Tampilan TFT
Proses utama yang terlibat dalam perakitan modul tampilan TFT meliputi penerapan film polarisasi, pengikatan COG & FPC, perakitan, dan berbagai proses pendukung. Berikut adalah penjelasan terperinci untuk masing-masing:
1.Ikatan COG & FPC
COG (Chip on Glass) dan FPC (Flexible Printed Circuit) merupakan metode penyambungan sirkuit. Karena banyaknya elektroda, penyambungan kabel satu-ke-satu yang tradisional menjadi tantangan. Praktik saat ini melibatkan pembentukan susunan elektroda pada kaca, dengan susunan yang sesuai pada IC/FPC, dan menggunakan Anisotropic Conductive Film (ACF) untuk menyambungkan setiap elektroda IC/FPC dengan elektroda kaca satu per satu.2.Mengaplikasikan Film Polarisasi
Karena pengoperasian LCD didasarkan pada cahaya terpolarisasi, pemasangan film polarisasi merupakan proses yang penting. Film ini mengendalikan cahaya yang melewati sel kristal cair untuk menghasilkan gambar.
3. Perakitan
Perakitan menyatukan lampu latar, layar, papan sirkuit kontrol, dan komponen lain seperti layar sentuh untuk membentuk modul tampilan yang lengkap. Hal ini biasanya dilakukan secara manual oleh teknisi terampil, yang memegang peranan penting dalam memastikan kualitas modul yang dirakit.
Selain proses utama, segmen modul mencakup beberapa proses tambahan, seperti:
1Pemotongan Laser dan Pengukuran Listrik Pasca Pemotongan
Setelah komponen dipotong secara tepat menggunakan laser, fungsi kelistrikannya diuji untuk memastikan komponen memenuhi spesifikasi yang dibutuhkan.2.Pengukuran Listrik Ikatan dan Pasca Ikatan
Pengujian kelistrikan juga dilakukan setelah proses pengikatan COG dan FPC untuk memverifikasi integritas sambungan ini.
3.Pemeriksaan Mikroskopis
Setelah pemotongan dan pengikatan laser, pemeriksaan mikroskopis (atau Pemeriksaan Optik Otomatis (AOI) untuk pengikatan FPC) dilakukan untuk memeriksa adanya cacat atau masalah.
4.Uji Kekuatan Kupas
Setelah ikatan IC dan ikatan FPC, uji kekuatan kelupas dilakukan untuk mengevaluasi daya tahan ikatan.
5. Penuaan Setelah Perakitan
Modul yang dirakit menjalani proses penuaan dengan daya yang diterapkan untuk memastikan keandalan jangka panjang.
6. Pengemasan dan Pengiriman
Setelah modul lulus semua pengujian dan inspeksi, modul tersebut dikemas dan dikirim ke pelanggan atau fase produksi berikutnya.

Latest articles
-
OLED Technology 2025: Ultimate Guide, Price Analysis, and Future Trends
OLED Technology 2025: Ultimate Guide, Price Analysis, and Future Trends