
La struttura del display LCD TFT
Pannello a cristalli liquidi (pannello): Questa è la parte principale del display, responsabile della presentazione dell'immagine. Il pannello a cristalli liquidi è formato da due lastre di vetro con uno strato di cristalli liquidi inserito tra di loro, noto come cella a cristalli liquidi.
Filtri polarizzatori:Questi componenti si trovano su entrambi i lati della cella a cristalli liquidi e hanno il compito di elaborare la luce che attraversa la cella.
Filtro colore: Solitamente realizzato su una delle piastre di vetro della cella a cristalli liquidi sigillata, viene utilizzato per la visualizzazione a colori.
Matrice di transistor a pellicola sottile (matrice TFT): Posizionato sull'altra lastra di vetro della cella a cristalli liquidi sigillata, svolge un ruolo attivo nel pilotaggio del display.
Retroilluminazione:La sorgente luminosa situata dietro il modulo display TFT-LCD fornisce la luce necessaria per produrre l'immagine visibile attraverso la cella a cristalli liquidi.
Circuito dell'unità esterna:Questi circuiti sono incaricati di gestire i segnali delle immagini in ingresso per pilotare in modo appropriato la matrice TFT e la retroilluminazione.

Il processo di fabbricazione dei display LCD TFT
Formazione del film:Tecniche come lo sputtering (SPT) e la deposizione chimica da vapore (CVD) depositano più strati sul substrato.
Fotolitografia: Applicazione, esposizione e sviluppo di fotoresist per formare microstrutture.
Acquaforte: I metodi di incisione a secco e a umido scolpiscono il substrato rimuovendo aree specifiche.
Spogliarello: Dopo la modellazione, i materiali in eccesso vengono rimossi per pulire il substrato.
Fasi del processo ausiliario:
Pulizia:Garantisce che il substrato sia privo di contaminazione.
Marcatura ed esposizione:Identifica e prepara i bordi del substrato.
Ispezione ottica automatizzata (AOI):Utilizzato per l'ispezione dei difetti.
Ispezione microscopica e ispezione macroscopica (Mic/Mac):Controllo dei dettagli.
Test delle prestazioni della pellicola:Utilizza strumenti quali misuratori di resistenza di foglio, profilometri, riflettometri/ellissometri, spettroscopia infrarossa a trasformata di Fourier.
Test elettrico aperto/cortocircuito (O/S):Controlla la continuità del circuito e i cortocircuiti. Test elettrico del Test Element Group (TEG): verifica le prestazioni elettriche degli elementi.
Test elettrico array:Garantisce la funzionalità elettrica dell'array.
Riparazione laser:Corregge eventuali difetti in base ai risultati dell'ispezione.
Rielaborazione del fotoresist (rielaborazione PR):Se necessario, regola o ripete i passaggi della fotolitografia.
Rielaborazione della pellicola: modifica o perfeziona il processo di formazione della pellicola, se necessario.

Strato OC protegge e prepara i modelli dei filtri colore.
Livello RGB formazione tramite sequenze di rivestimento, esposizione e sviluppo.
Strato BM (matrice nera) migliora il contrasto e limita la dispersione della luce.
Livello PS (distanziatore fotografico) mantiene uno spazio preciso tra i substrati, fondamentale per la qualità dell'immagine.
QUESTO strato aggiunge una pellicola conduttiva trasparente per la conduzione elettrica e la funzionalità tattile.

Allineamento e orientamento della poliimmide (PI): Applicazione e orientamento dello strato PI per l'allineamento dei cristalli liquidi.
ODF (pellicola per visualizzazione ottica) migliora gli effetti visivi.
Pulizia e applicazione del sigillante per telaio: Preparazione per l'inserimento delle gocce di cristalli liquidi.
Iniezione di cristalli liquidi: Distribuzione precisa dei cristalli liquidi sul display.
Laminazione TFT e CF: Unire insieme i componenti TFT e CF.
Polimerizzazione UV e lavorazione termica: Solidificazione e distribuzione uniforme dei cristalli liquidi con luce ultravioletta e trattamento termico.
Taglio, test elettrici e levigatura dei bordi: Modellatura del substrato, esecuzione di controlli elettrici e levigatura dei bordi.
Attacco polarizzatore e debubbing: Applicazione di pellicole polarizzanti ed eliminazione delle bolle d'aria, con possibilità di rilavorazione se necessario.

Taglio laser e test elettrici: Garantire la forma precisa e l'integrità elettrica.
Incollaggio COG (chip su vetro), incollaggio e collaudo FPC (circuito stampato flessibile): Installazione e collaudo del circuito di pilotaggio.
Assemblaggio e collaudo elettrico: Combinazione di tutte le parti del modulo display ed esecuzione dei test elettrici finali.
Invecchiamento: Alimentazione a lungo termine per garantire l'affidabilità del prodotto.
Imballaggio e spedizione: Preparazione del prodotto finito per la consegna.

Flusso del segmento di array
G: L'isolante di gate, realizzato in SiNx (nitruro di silicio), fornisce l'isolamento necessario tra il gate e gli altri strati.
I: Lo strato del canale, a-Si (silicio amorfo), dove avviene la commutazione elettronica.
N: Lo strato n+ a-Si è drogato con un'elevata concentrazione di fosfina (PH3). Questo drogaggio riduce la barriera di potenziale all'interfaccia, assicurando un contatto ohmico che è fondamentale per un funzionamento affidabile del dispositivo.

Metallo di porta (AlNd/MoN)

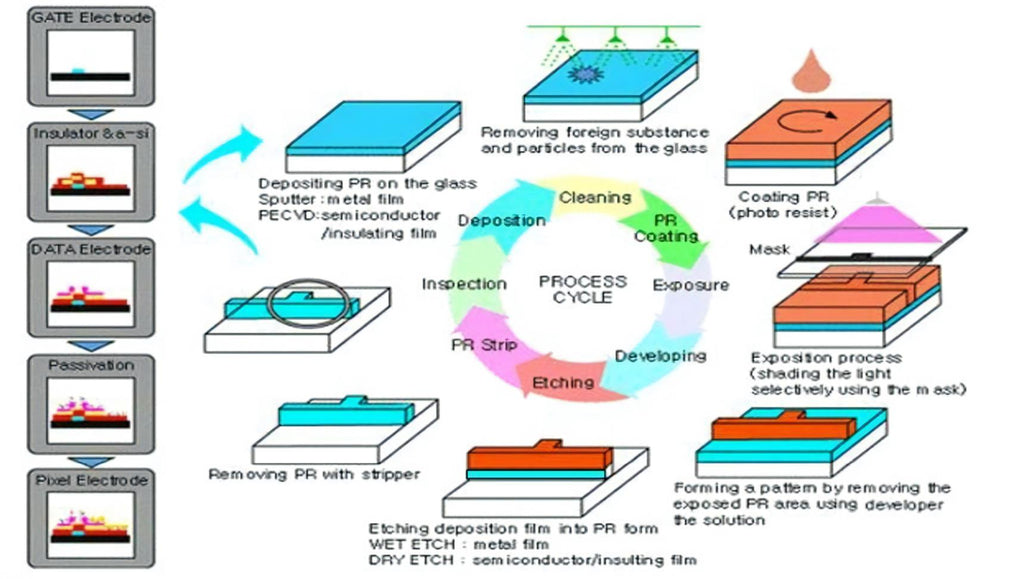
GIN (SiNx / a-Si / n+ a-Si)

Metallo S/D (Mo \Al\Mo)
La formazione degli elettrodi sorgente e drain (S/D), dell'elettrodo dati e del canale include procedure specifiche come la stratificazione con nitruro di molibdeno (MoN) e alluminio puro (per sorgente e drain), lo sputtering dello strato metallico S/D, la fotolitografia S/D, l'incisione a umido S/D e l'incisione a secco del canale. Attraverso questi processi, gli elettrodi sorgente e drain, il canale e le linee dati del TFT si formano sul substrato di vetro. In questa fase, la costruzione del TFT è conclusa. Il design e il processo risultanti sono i seguenti:
Sputtering S/D: Questo è un passaggio cruciale per formare elettrodi source/drain. Durante questo processo, uno strato denso di elettrodi metallici viene formato spruzzando ioni di metallo pesante sul substrato.
Pulizia prima del rivestimento PR: Prima di applicare il fotoresist, è necessario pulire il substrato per rimuovere polvere e residui, per garantire buoni risultati di rivestimento.
DHP (piastra riscaldante): Per far aderire meglio il fotoresist al substrato, quest'ultimo viene preriscaldato su una piastra calda prima del processo di rivestimento.
Rivestimento resistente: Applicare uno strato di fotoresist al substrato preriscaldato, che verrà utilizzato per la successiva modellazione.
Pre-polimerizzazione (SHP): Il substrato rivestito di fotoresist viene pre-polimerizzato per rendere il fotoresist più uniforme e resistente.
Esposizione del passo-passo: In questa fase, la quantità di esposizione alla luce viene controllata per indurire determinate aree del fotoresist e creare il motivo desiderato.
In via di sviluppo: Il fotoresist esposto viene elaborato per rivelare il motivo.
Fotoresist post cottura (HHP): Il pattern del fotoresist viene ulteriormente indurito e reso più evidente tramite un altro processo di riscaldamento. Ciò può anche migliorare la sua capacità di resistere alla corrosione chimica e all'usura.
Sviluppo dell'ispezione:Dopo lo sviluppo, è necessaria un'ispezione dettagliata per garantire l'accuratezza del modello e rilevare e risolvere tempestivamente eventuali problemi.
Incisione a umido: Si tratta di un processo di reazione chimica in cui un liquido corrosivo viene utilizzato per incidere il materiale nelle aree non protette, formando così lo schema del circuito.
Incisione a secco del canale: Si forma un canale tra la sorgente e il drain. In questo processo, il silicio nella regione del canale viene inciso nella forma richiesta utilizzando una tecnica di incisione a secco.
Striscia di resistenza: Infine, per pulire la superficie del substrato, si rimuove il fotoresist dal substrato.
Dopo i passaggi sopra descritti, gli elettrodi sorgente/drain, gli elettrodi dati e il canale TFT vengono infine formati sul substrato di vetro.
Passivazione (SiNx)
La formazione dello strato di passivazione (SiNx), spesso noto come strato di isolamento protettivo, insieme alle vie, include operazioni specifiche come la formazione di film PECVD, la fotolitografia e l'incisione a secco per la creazione delle vie. Dopo aver eseguito queste procedure, lo strato di isolamento protettivo per il canale TFT e le vie conduttive vengono infine formati sul substrato di vetro. Le immagini e il processo ottenuti dopo il completamento di questi passaggi sono i seguenti:
2. Pulizia pre-rivestimento - Questa è la fase in cui il substrato viene pulito prima dell'applicazione del fotoresist.
3. Precottura sulla piastra riscaldante (DHP) - Comporta l'utilizzo di una piastra riscaldante per preriscaldare il substrato e prepararlo alla fase di rivestimento.
4. Rivestimento fotoresistente - Durante questa fase viene applicato uno strato di fotoresist sul substrato.
5. Cottura morbida (SHP) - Il substrato, rivestito con fotoresist, viene sottoposto a un processo di pre-polimerizzazione per solidificare lo strato.
6. Esposizione del passo-passo - In questo caso, si utilizza la tecnologia della litografia stepper per esporre il fotoresist e formare i modelli.
7. Sviluppo - Il fotoresist esposto viene elaborato per rivelare il motivo.
8. Cottura dura (HHP) - Il modello fotoresist viene indurito tramite un trattamento post-cottura.
9. Ispezione post-sviluppo - Questa fase prevede l'ispezione del substrato sviluppato per confermare l'accuratezza dei modelli.
10. Incisione a umido - I materiali indesiderati a pellicola sottile vengono rimossi tramite un processo di incisione chimica a umido per creare schemi di circuiti.
11. Rimozione del fotoresist - Il fotoresist viene rimosso e la superficie del substrato viene pulita.
12. Incisione dei fori di contatto (Incisione CH) - I fori necessari vengono formati tramite un processo di incisione a secco.
Di seguito sono riportati i passaggi dettagliati coinvolti nella preparazione del substrato per le applicazioni TFT, che portano alla protezione del canale TFT attivo e alla formazione di vie conduttive.
Formazione di elettrodo pixel trasparente ITO (ossido di indio-stagno)
La creazione di elettrodi pixel trasparenti nei display TFT è un processo sofisticato, che inizia con la deposizione di ossido di indio-stagno (ITO). Le fasi coinvolte sono progettate con precisione e includono lo sputtering dello strato ITO per ottenere la trasparenza, seguito dalla fotolitografia per una modellazione intricata e concluso con l'incisione a umido per finalizzare la struttura dei pixel. Questa sequenza meticolosa si conclude con la formazione degli elettrodi pixel, perfettamente integrati sul substrato di vetro, che segna il completamento fondamentale del processo di array. Il seguente flusso di lavoro descrive in dettaglio la raffinatezza e la sequenza delle operazioni post-completamento del processo.
Deposizione di strati di pixel (ITO Sputtering) – Crea una pellicola conduttiva trasparente di ITO (ossido di indio e stagno) per la successiva modellazione dei pixel.
Pulizia del substrato (pulizia del rivestimento pre-resist) – Garantisce la purezza del substrato prima di applicare il materiale fotoresist.
Preriscaldamento del substrato (piastra riscaldante per disidratazione, DHP) – Prepara il substrato con una fase di pre-cottura per un'adesione ottimale del fotoresist.
Applicazione di resistenza (rivestimento) – Applica uno strato uniforme di fotoresist sul substrato.
Soft Bake (pre-polimerizzazione SHP) – Esegue la pre-polimerizzazione per solidificare il fotoresist prima della modellazione.
Esposizione di precisione (esposizione stepper) – Utilizza la fotolitografia stepper per esporre il fotoresist, creando il motivo desiderato.
Sviluppo del modello (in via di sviluppo) – Sviluppa il fotoresist esposto per rivelare l'intricato schema dei pixel.
Resist Harden (cottura post-esposizione, cottura dura HHP) – Indurisce il fotoresist modellato per migliorarne la resistenza all'incisione.
Ispezione del modello (ispezione post-sviluppo) – Ispeziona i modelli sviluppati per verificarne l'accuratezza e l'integrità.
Trasferimento del modello (incisione ITO) – Trasferisce il modello tramite l'incisione dello strato ITO per formare elettrodi pixel.
Rimozione della resistenza (striscia) – Rimuove il fotoresist, lasciando una superficie del substrato pulita.
Miglioramento delle prestazioni (ricottura) – Ricottura dei componenti per migliorare le proprietà elettriche dei transistor a film sottile.
Controllo di qualità (test TEG) – Esegue test elettrici sugli elementi di prova per monitorarne la qualità durante la produzione.
Questa sequenza semplificata getta le basi per display TFT di alta qualità con prestazioni elettriche ottimali.

Processo di filtro colore (CF)
Substrato di vetro: Lo strato di base fondamentale che fornisce supporto meccanico.
Matrice Nera (BM): Realizzato in un materiale che assorbe la luce, delinea ogni pixel e riduce al minimo la dispersione di luce tra i pixel, migliorando il contrasto.
Strati di resina colorata: Come i veri filtri colorati di rosso, verde e blu, questi strati determinano i colori dei pixel. Sono realizzati in un materiale di resina trasparente tinto.
Strato di soprabito (OC): Uno strato protettivo sovrapposto alle resine colorate per uniformare la superficie e proteggere i filtri da danni fisici e chimici.
Elettrodo ITO (ossido di indio e stagno): Questo strato conduttivo trasparente consente al pannello di funzionare come un elettrodo, regolando la luce che lo attraversa.

Preparazione del substrato: La pulizia del substrato di vetro è fondamentale, pertanto viene sottoposto a una pulizia approfondita per eliminare le impurità che potrebbero compromettere la qualità del CF.
Formazione della matrice nera: Applicando uno strato di fotoresist al substrato pulito, la fotolitografia viene utilizzata per delineare il pattern BM. Dopo l'esposizione, le aree non sviluppate vengono rivelate e riempite con pigmento nero, quindi polimerizzate.
Applicazione della resina colorata: L'applicazione successiva di resine di colore rosso, verde e blu all'interno dei confini BM viene eseguita utilizzando un processo di fotolitografia distinto per ogni strato di colore. Dopo il rivestimento e l'esposizione, le aree senza fotoresist vengono sviluppate e riempite con la resina, seguite dalla polimerizzazione.
Applicazione dello strato di soprabito: Uno strato di OC viene applicato sopra i colori della resina per proteggerli e creare una superficie liscia per la successiva deposizione dell'elettrodo ITO.
Deposizione dell'elettrodo ITO: L'elettrodo ITO trasparente viene depositato mediante sputtering sullo strato OC, quindi modellato per strutturare l'architettura dell'elettrodo.
Ispezione e collaudo: Durante la produzione, ispezioni e test meticolosi garantiscono la qualità CF. Parametri come fedeltà del colore, uniformità e livelli di difetto vengono esaminati attentamente.
Integrazione: Dopo la garanzia di qualità, il filtro colorato viene allineato con precisione e laminato con i componenti del pannello TFT-LCD, come la matrice TFT e lo strato di cristalli liquidi.

Flusso del segmento CELL
Il processo di produzione nell'aspetto "Cell" di un display TFT può essere suddiviso approssimativamente in quattro fasi chiave: allineamento, boxing, taglio e fissaggio del polarizzatore. Gli obiettivi e le procedure principali di queste fasi sono delineati brevemente come segue:
Il processo di allineamento
L'obiettivo del processo di allineamento è creare uno strato di pellicola PI (poliimmide) trasparente su entrambi i substrati TFT e CF. Attraverso un successivo processo di attrito, questo strato influenza le molecole di cristalli liquidi ad allinearsi nella direzione dell'attrito. Per una comprensione più approfondita dei principi sottostanti, i lettori interessati dovrebbero fare riferimento alla letteratura pertinente. Pertanto, questa fase presenta in modo prominente due processi primari: stampa PI e sfregamento.
Stampa PI (poliimmide)
La poliimmide (PI) è un materiale polimerico organico trasparente ad alte prestazioni costituito da catene principali e laterali. Dopo l'applicazione e la cottura, aderisce saldamente alle superfici dei substrati CF e TFT. Il rivestimento di PI utilizza una speciale tecnica di stampa rotocalco. Oltre al processo primario di stampa rotocalco, la stampa PI comporta diversi processi ausiliari tra cui la pulizia del substrato prima della stampa, la pre-cottura dopo la stampa, l'ispezione ottica automatica, la polimerizzazione e, se necessario, un processo di rilavorazione PI.
1. Pulizia pre-PI:Questa fase prevede la pulizia accurata del substrato prima della stampa, assicurandosi che sia privo di polvere, grasso e altri contaminanti per prepararlo alle fasi successive.
2.PI Stampa:In questo caso, il materiale PI (poliimmide) viene applicato sul substrato, in modo analogo alla stampa di un disegno su carta, solo che l'inchiostro è un materiale speciale che forma uno strato protettivo.3.Pre-cottura:Considerate questa una fase di cottura preliminare, che asciuga parzialmente lo strato di PI per garantire una corretta adesione al substrato.
4. Ispezione PI:A questo punto, gli strati stampati vengono esaminati attentamente per individuare eventuali macchie, aree irregolari o difetti, un po' come quando si ispeziona una parete dipinta per individuare eventuali imperfezioni.
5.Rielaborazione PI:Se durante l'ispezione vengono individuati dei problemi, questa fase comporta la correzione delle imperfezioni, in modo simile alla cancellazione degli errori su uno schizzo.
6.PI Polimerizzazione:Infine, lo strato PI viene completamente indurito tramite un processo di cottura, proprio come l'argilla viene indurita in una fornace, diventando così resistente e durevole.
Questa fase è finalizzata alla rimozione di polvere e particelle dal substrato mediante un pulitore a ultrasuoni, che impiega onde ultrasoniche per una pulizia approfondita. Ciò garantisce che il substrato sia privo di contaminanti prima di procedere alle fasi successive.
2. Allineamento:
La fase di allineamento regola l'orientamento del substrato per soddisfare i requisiti visivi. Questo processo è semplice e si concentra sul posizionamento corretto del substrato per i trattamenti successivi.
3. Strofinamento:
Durante la fase di sfregamento, si usa un panno di velluto per strofinare lo strato di PI. Questa azione allinea le catene laterali del PI in una direzione unificata, organizzando la struttura molecolare per ottenere le proprietà superficiali desiderate.
4. Pulizia ad ultrasuoni post-sfregamento (USC):
Dopo lo sfregamento, il substrato potrebbe presentare particelle o residui. La pulizia USC post-sfregamento rimuove questi residui, assicurando che la superficie del substrato sia impeccabilmente pulita. Questo passaggio è fondamentale per mantenere la qualità del prodotto finale, poiché utilizza onde ultrasoniche per rimuovere e rimuovere eventuali particelle o residui aderiti durante il processo di sfregamento.

Processo di incapsulamento ODF (One Drop Fill)
1. Applicazione del sigillante e della pasta d'argento:L'adesivo UV-curable è utilizzato come sigillante, applicato lungo i bordi dei substrati di vetro CF e TFT, per garantire che i due substrati siano saldamente legati e per definire lo spessore della cella. Contemporaneamente, l'applicazione di pasta d'argento serve per collegare gli elettrodi comuni su CF e TFT per garantire la connettività elettrica.
2. Rivestimento a cristalli liquidi:Il materiale a cristalli liquidi viene lasciato cadere sul substrato TFT che è già stato rivestito con il sigillante. Il materiale a cristalli liquidi svolge un ruolo critico nel processo di visualizzazione; regola lo stato della luce che lo attraversa modificandone la disposizione, controllando così il colore e la luminosità dei pixel.
3. Saldatura sotto vuoto:Il substrato CF, rivestito con sigillante, pasta d'argento e cristalli liquidi, viene legato al substrato TFT in un ambiente sotto vuoto. Questo passaggio aiuta a prevenire la formazione di bolle e garantisce che vi sia un legame stretto e senza spazi tra i due substrati.
Polimerizzazione termica:Una volta completata la polimerizzazione UV, i substrati vengono sottoposti a un processo termico per rafforzare ulteriormente l'adesione del sigillante. Questo passaggio è particolarmente mirato alle aree non completamente raggiunte dalla luce UV, come sotto i cavi, assicurando che queste parti siano completamente polimerizzate.

1.Taglio
A causa delle dimensioni definite del substrato di vetro e della varietà di dimensioni del prodotto, più celle di prodotto sono disposte su un singolo substrato di vetro. Il taglio viene eseguito facendo scorrere una mola diamantata sulla superficie del vetro. In genere, dopo il taglio si verifica un processo di debonding, ma con i progressi nella tecnologia delle mole di taglio, ora esiste una tecnica che crea un segno di taglio molto profondo, eliminando la necessità di debonding.
2.Bordo
Dopo che il vetro è stato tagliato in schermi individuali, i bordi di ogni schermo presentano molte piccole crepe. Per evitare che queste crepe causino rotture dovute a collisioni nella successiva movimentazione, è necessario un trattamento di bordatura.
3. Misurazione elettrica
La misurazione elettrica è un processo ausiliario utilizzato più volte durante la produzione, ma è particolarmente cruciale qui perché è la prima volta che si applica l'elettricità per testare le prestazioni del display LCD. Il principio di test è semplice: applicare l'elettricità ai singoli pixel del display e osservare le prestazioni del display della cella attraverso una pellicola polarizzante. In genere, una barra corta utilizzata per il test dell'array viene elettrificata. Dopo il test elettrico, gli schermi che non soddisfano gli standard vengono rimossi per evitare sprechi di materiali nelle fasi successive.
Ulteriori processi ausiliari includono l'ispezione visiva post-taglio e la pulizia post-bordatura.
Processo di assemblaggio del modulo display TFT
I processi principali coinvolti nell'assemblaggio dei moduli display TFT includono l'applicazione della pellicola polarizzante, la saldatura COG e FPC, l'assemblaggio e vari processi di supporto. Di seguito è riportata un'introduzione dettagliata a ciascuno:
1. Legame COG e FPC
COG (Chip on Glass) e FPC (Flexible Printed Circuit) rappresentano metodi di collegamento dei circuiti. A causa della moltitudine di elettrodi, i tradizionali collegamenti uno a uno dei fili sono difficili. La pratica attuale prevede la formazione di una matrice di elettrodi sul vetro, con una matrice corrispondente sull'IC/FPC e l'utilizzo di un film conduttivo anisotropico (ACF) per collegare ogni elettrodo IC/FPC con l'elettrodo di vetro uno alla volta.2.Applicazione della pellicola polarizzante
Poiché il funzionamento LCD si basa sulla luce polarizzata, l'applicazione di una pellicola polarizzante è un processo essenziale. Questa pellicola controlla la luce che passa attraverso le celle a cristalli liquidi per produrre immagini.
3.Assemblaggio
L'assemblaggio unisce la retroilluminazione, lo schermo, la scheda di controllo e altri componenti come i touchscreen per formare un modulo display completo. Questo viene solitamente eseguito manualmente da tecnici qualificati, che svolgono un ruolo cruciale nel garantire la qualità dei moduli assemblati.
Oltre ai processi principali, il segmento del modulo comprende diversi processi ausiliari, quali:
1.Taglio laser e misurazione elettrica post-taglio
Dopo che i componenti sono stati tagliati con precisione tramite laser, le loro funzioni elettriche vengono testate per garantire che soddisfino le specifiche richieste.2. Misurazione elettrica di bonding e post-bonding
Dopo i processi di incollaggio COG e FPC vengono eseguiti anche test elettrici per verificare l'integrità di queste connessioni.
3. Ispezione microscopica
Dopo il taglio laser e l'incollaggio, vengono eseguite ispezioni microscopiche (o ispezioni ottiche automatizzate (AOI) per l'incollaggio FPC) per verificare eventuali difetti o problemi.
4.Test di resistenza alla pelatura
Dopo la saldatura dei circuiti integrati e la saldatura FPC, vengono eseguiti test di resistenza alla pelatura per valutare la durata delle saldature.
5. Invecchiamento dopo l'assemblaggio
I moduli assemblati vengono sottoposti a un processo di invecchiamento con alimentazione elettrica per garantirne l'affidabilità a lungo termine.
6. Imballaggio e spedizione
Una volta superati tutti i test e le ispezioni, i moduli vengono imballati e spediti al cliente o alla fase successiva della produzione.

Latest articles
-
OLED Technology 2025: Ultimate Guide, Price Analysis, and Future Trends
OLED Technology 2025: Ultimate Guide, Price Analysis, and Future Trends