
Struktura wyświetlacza TFT LCD
Panel ciekłokrystaliczny (Panel):To główna część wyświetlacza, odpowiedzialna za prezentację obrazu. Panel ciekłokrystaliczny składa się z dwóch szklanych płyt z warstwą ciekłego kryształu umieszczoną między nimi, zwaną komórką ciekłokrystaliczną.
Filtry polaryzacyjne:Elementy te znajdują się po obu stronach komórki z ciekłym kryształem i ich zadaniem jest przetwarzanie światła przechodzącego przez komórkę.
Filtr kolorów: Zazwyczaj wykonany na jednej ze szklanych płyt uszczelnionej komórki ciekłokrystalicznej; służy do wyświetlania kolorów.
Cienkowarstwowa matryca tranzystorów (TFT):Umieszczony na drugiej szklanej płytce uszczelnionej komórki ciekłokrystalicznej, odgrywa aktywną rolę w sterowaniu wyświetlaczem.
Podświetlenie:Źródło światła umieszczone za modułem wyświetlacza TFT-LCD zapewnia światło niezbędne do wytworzenia widocznego obrazu przez komórkę ciekłokrystaliczną.
Zewnętrzny obwód napędowy:Obwody te odpowiadają za zarządzanie sygnałami wejściowymi obrazu w celu odpowiedniego sterowania matrycą TFT i podświetleniem.

Proces produkcyjny wyświetlaczy TFT LCD
Formacja filmowa:Techniki takie jak rozpylanie (SPT) i osadzanie chemiczne z fazy gazowej (CVD) pozwalają na osadzanie wielu warstw na podłożu.
Fotolitografia:Nakładanie, naświetlanie i wywoływanie fotorezystu w celu utworzenia mikrostruktur.
Akwaforta:Metody trawienia na mokro i na sucho rzeźbią podłoże poprzez usuwanie określonych obszarów.
Rozbieranie:Po wykonaniu wzoru nadmiar materiałów jest usuwany w celu oczyszczenia podłoża.
Dodatkowe kroki procesu:
Czyszczenie:Zapewnia, że podłoże jest wolne od zanieczyszczeń.
Oznaczanie i ekspozycja:Identyfikuje i przygotowuje krawędzie podłoża.
Automatyczna inspekcja optyczna (AOI):Stosowany do kontroli defektów.
Inspekcja mikroskopowa i inspekcja makroskopowa (Mic/Mac):Sprawdzanie szczegółów.
Testowanie wydajności filmu:Posługuje się narzędziami takimi jak mierniki rezystancji powierzchniowej, profilometry, reflektometr/elipsometria i spektroskopia w podczerwieni z transformacją Fouriera.
Testowanie elektryczne stanu otwartego/zwartego (O/S):Sprawdzanie ciągłości obwodów i zwarć. Testowanie elektryczne grupy elementów testowych (TEG): testowanie wydajności elektrycznej elementów.
Testowanie elektryczne tablic:Zapewnia funkcjonalność elektryczną macierzy.
Naprawa laserowa:Usuwa wszelkie wady zgodnie z wynikami kontroli.
Przeróbka fotorezystu (przeróbka PR):W razie potrzeby dostosowuje lub powtarza kroki fotolitografii.
Przeróbka filmu: W razie potrzeby zmienia lub udoskonala proces powstawania filmu.

Warstwa OC chroni i przygotowuje wzory filtrów kolorów.
Warstwa RGB tworzenie poprzez sekwencje powlekania, naświetlania i wywoływania.
Warstwa BM (Czarna Matryca) zwiększa kontrast i ogranicza wyciek światła.
Warstwa PS (Photo Spacer) utrzymuje precyzyjną szczelinę między podłożami, co ma kluczowe znaczenie dla jakości obrazu.
Warstwa informatyczna dodaje przezroczystą powłokę przewodzącą, zapewniającą przewodnictwo elektryczne i funkcjonalność dotykową.

Wyrównanie i orientacja poliimidu (PI):Nakładanie i orientowanie warstwy PI w celu wyrównania kryształu ciekłego.
ODF (Folia do wyświetlaczy optycznych) poprawia efekty wizualne.
Czyszczenie i aplikacja uszczelniacza ramy:Przygotowanie do wprowadzenia kropli ciekłego kryształu.
Wtrysk ciekłego kryształu:Precyzyjne dozowanie ciekłych kryształów na wyświetlaczu.
Laminowanie TFT i CF:Połączenie ze sobą elementów TFT i CF.
Utwardzanie UV i obróbka termiczna:Utwardzanie i równomierne rozprowadzanie ciekłego kryształu za pomocą światła ultrafioletowego i obróbki cieplnej.
Cięcie, testowanie elektryczne i wygładzanie krawędzi:Kształtowanie podłoża, wykonywanie kontroli elektrycznych i wygładzanie krawędzi.
Mocowanie polaryzatora i usuwanie pęcherzyków powietrza:Nakładanie folii polaryzacyjnej i usuwanie pęcherzyków powietrza, w razie potrzeby dopuszcza się poprawkę.

Cięcie laserowe i testowanie elektryczne:Zapewnienie precyzyjnego kształtu i integralności elektrycznej.
Łączenie COG (Chip On Glass), łączenie i testowanie FPC (Flexible Printed Circuit):Instalowanie i testowanie obwodów sterujących.
Montaż i testowanie elektryczne:Połączenie wszystkich części modułu wyświetlacza i wykonanie końcowych testów elektrycznych.
Starzenie się:Długotrwałe zasilanie gwarantujące niezawodność produktu.
Opakowanie i wysyłka:Przygotowanie gotowego produktu do dostawy.

Przepływ segmentu tablicy
G: Izolator bramki wykonany z SiNx (azotku krzemu) zapewnia niezbędną izolację pomiędzy bramką i innymi warstwami.
I: Warstwa kanałowa, a-Si (krzem amorficzny), w której zachodzi przełączanie elektroniczne.
N: Warstwa n+ a-Si jest domieszkowana wysokim stężeniem fosfiny (PH3). Domieszkowanie to zmniejsza barierę potencjału na granicy faz, zapewniając kontakt omowy, który jest kluczowy dla niezawodnej pracy urządzenia.

Brama metalowa (AlNd/MoN)

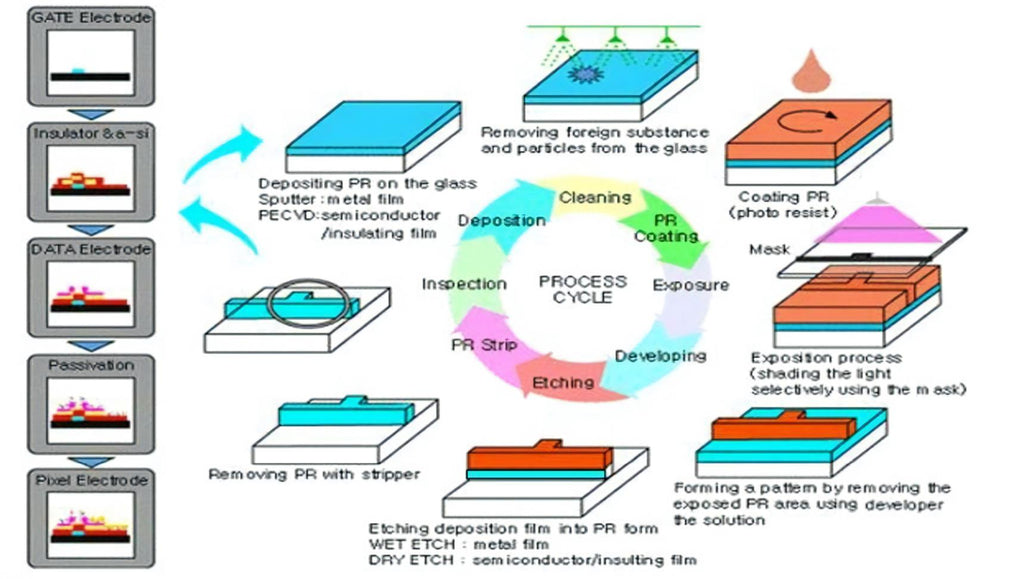
GIN (SiNx / a-Si / n+ a-Si)

Metale S/D (Mo \Al\Mo)
Formowanie elektrod źródłowych i odpływowych (S/D), elektrody danych i kanału obejmuje określone procedury, takie jak nakładanie warstw azotku molibdenu (MoN) i czystego aluminium (dla źródła i odpływu), rozpylanie warstwy metalu S/D, fotolitografia S/D, trawienie na mokro S/D i trawienie na sucho kanału. Poprzez te procesy elektrody źródłowe i odpływowe, kanał i linie danych TFT formują się na podłożu szklanym. Na tym etapie kończy się budowa TFT. Wynikowy projekt i proces są następujące:
Rozpylanie S/D:To kluczowy krok w tworzeniu elektrod źródłowych/odpływowych. Podczas tego procesu gęsta warstwa elektrod metalowych jest formowana przez rozpylanie jonów metali ciężkich na podłoże.
Czyszczenie przed nałożeniem powłoki PR:Przed nałożeniem fotorezystu podłoże musi zostać oczyszczone z kurzu i pozostałości, co zapewni dobre rezultaty powłoki.
DHP (Płyta grzewcza)Aby lepiej przymocować fotorezyst do podłoża, przed procesem powlekania podłoże jest podgrzewane na gorącej płycie.
Powłoka odporna: Na podgrzane wcześniej podłoże nanieść warstwę fotorezystu, która posłuży do późniejszego nadania wzoru.
Wstępne utwardzanie (SHP)Podłoże pokryte fotorezystem jest wstępnie utwardzane, co sprawia, że fotorezyst jest bardziej jednolity i mocniejszy.
Ekspozycja Steppera:Na tym etapie kontroluje się ilość światła, aby utwardzić określone obszary fotorezystu i stworzyć pożądany wzór.
Rozwijanie:Naświetlony fotorezyst jest poddawany obróbce w celu ujawnienia wzoru.
Wypiekanie fotorezystu (HHP):Wzór fotorezystu jest dalej utwardzany i bardziej widoczny poprzez kolejny proces ogrzewania. Może to również poprawić jego odporność na korozję chemiczną i zużycie.
Rozwijanie inspekcji:Po wywołaniu wzoru konieczna jest szczegółowa kontrola w celu sprawdzenia jego dokładności oraz szybkiego wykrycia i rozwiązania wszelkich problemów.
Mokre trawienie:Jest to proces reakcji chemicznej, w którym żrąca ciecz jest wykorzystywana do wytrawiania materiału w obszarach niechronionych w celu utworzenia wzoru obwodu.
Trawienie kanałowe na sucho:Pomiędzy źródłem a odpływem tworzy się kanał. W tym procesie krzem w obszarze kanału jest wytrawiany do wymaganego kształtu za pomocą techniki wytrawiania na sucho.
Pasek oporowy:Na koniec, aby oczyścić powierzchnię podłoża, usuwa się z niego warstwę fotorezystu.
Po wykonaniu powyższych kroków elektrody źródłowe/odpływowe, elektrody danych i kanał TFT zostają ostatecznie utworzone na podłożu szklanym.
Pasywacja (SiNx)
Tworzenie warstwy pasywacyjnej (SiNx), często nazywanej ochronną warstwą izolacyjną, wraz z przelotkami, obejmuje określone operacje, takie jak formowanie filmu PECVD, fotolitografia i suche trawienie w celu utworzenia przelotek. Po przejściu przez te procedury, ochronna warstwa izolacyjna dla kanału TFT i przewodzących przelotek jest ostatecznie formowana na szklanym podłożu. Obrazy i proces uzyskany po zakończeniu tych kroków są następujące:
2. Czyszczenie przed nałożeniem powłoki - W tym miejscu podłoże jest czyszczone przed nałożeniem fotorezystu.
3. Wstępne pieczenie na płycie grzewczej (DHP) – polega na wykorzystaniu płyty grzejnej do wstępnego podgrzania podłoża w celu przygotowania go do nakładania powłoki.
4. Powłoka fotorezystu - Na tym etapie na podłoże nakładana jest warstwa fotorezystu.
5. Miękkie pieczenie (SHP) - Podłoże pokryte fotorezystem poddawane jest procesowi wstępnego utwardzania w celu zestalenia warstwy.
6. Ekspozycja steppera - W tym przypadku do naświetlenia fotorezystu i uformowania wzorów wykorzystano technologię litografii krokowej.
7. Rozwój - Naświetlony fotorezyst jest poddawany obróbce w celu ujawnienia wzoru.
8. Twarde pieczenie (HHP) - Wzór fotorezystu jest utwardzany poprzez obróbkę końcową.
9. Kontrola po opracowaniu - Na tym etapie przeprowadza się kontrolę opracowanego podłoża w celu potwierdzenia dokładności wzorów.
10. Trawienie na mokro - Niechciane materiały cienkowarstwowe są usuwane za pomocą procesu trawienia chemicznego na mokro w celu wytworzenia wzorów obwodów.
11. Usuwanie fotorezystu - Usuwamy fotorezyst i czyścimy powierzchnię podłoża.
12. Trawienie otworów kontaktowych (TRAWIENIE CH) - Wymagane otwory przelotowe formowane są poprzez proces trawienia na sucho.
Poniżej przedstawiono szczegółowe kroki przygotowania podłoża do zastosowań TFT, mające na celu ochronę aktywnego kanału TFT i utworzenie przewodzących otworów przelotowych.
Tworzenie przezroczystej elektrody pikselowej ITO (tlenek indu i cyny)
Tworzenie przezroczystych elektrod pikselowych w wyświetlaczach TFT to skomplikowany proces, rozpoczynający się od osadzania tlenku indu-cyny (ITO). Etapy są precyzyjnie zaprojektowane i obejmują rozpylanie warstwy ITO w celu uzyskania przezroczystości, a następnie fotolitografię w celu uzyskania skomplikowanych wzorów i kończą się trawieniem na mokro w celu sfinalizowania struktury pikseli. Ta skrupulatna sekwencja kończy się formowaniem elektrod pikselowych, bezbłędnie zintegrowanych z podłożem szklanym, co oznacza kluczowe zakończenie procesu matrycowego. Poniższy przepływ pracy szczegółowo opisuje udoskonalenie i kolejność operacji po zakończeniu procesu.
Osadzanie warstw pikselowych (rozpylanie ITO) – Tworzy przezroczystą, przewodzącą warstwę ITO (tlenku indu i cyny) do późniejszego tworzenia wzorów pikseli.
Czyszczenie podłoża (czyszczenie przed nałożeniem powłoki ochronnej) – Zapewnia czystość podłoża przed nałożeniem materiału fotorezystywnego.
Podgrzewanie podłoża (płyta grzewcza do odwadniania, DHP) – Przygotowuje podłoże poprzez etap wstępnego wypalania w celu zapewnienia optymalnej przyczepności fotorezystu.
Aplikacja Reist (powłoka) – Nakłada równomierną warstwę fotorezystu na podłoże.
Miękkie pieczenie (wstępne utwardzanie SHP) – Przeprowadza wstępne utwardzanie w celu zestalenia fotorezystu przed formowaniem wzoru.
Precyzyjna ekspozycja (ekspozycja krokowa) – Wykorzystuje fotolitografię krokową do naświetlenia fotorezystu, tworząc pożądany wzór.
Rozwój wzorca (Rozwój) – Wywołuje odsłonięty fotorezyst, aby odsłonić skomplikowany wzór pikseli.
Resist Harden (wypiekanie po ekspozycji, twarde wypiekanie HHP) – Utwardza wzorzysty fotorezyst, zwiększając odporność na wytrawianie.
Kontrola wzoru (kontrola po opracowaniu) – Sprawdza dokładność i integralność opracowanych wzorców.
Transfer wzoru (trawienie ITO) – Przenosi wzór poprzez wytrawienie warstwy ITO w celu utworzenia elektrod pikselowych.
Usuwanie oporów (pasek) – Usuwa fotorezyst, pozostawiając czystą powierzchnię podłoża.
Poprawa wydajności (wyżarzanie) – Wyżarza elementy w celu poprawy właściwości elektrycznych tranzystorów cienkowarstwowych.
Kontrola jakości (test TEG) – Wykonuje testy elektryczne elementów testowych w celu monitorowania jakości w trakcie produkcji.
Ta usprawniona sekwencja działań stanowi podstawę wysokiej jakości wyświetlaczy TFT o optymalnej charakterystyce elektrycznej.

Proces filtra kolorów (CF)
Podłoże szklane: Podstawowa warstwa bazowa zapewniająca wsparcie mechaniczne.
Czarna matryca (BM): Wykonany z materiału pochłaniającego światło, wyodrębnia każdy piksel i minimalizuje międzypikselowe przecieki światła, co poprawia kontrast.
Warstwy żywicy kolorowej: Jako rzeczywiste filtry w kolorze czerwonym, zielonym i niebieskim, warstwy te określają kolory pikseli. Są wykonane z barwionego, przezroczystego materiału żywicznego.
Warstwa wierzchnia (OC): Warstwa ochronna nakładana na żywice kolorowe, wyrównuje powierzchnię i chroni filtry przed uszkodzeniami fizycznymi i chemicznymi.
Elektroda ITO (tlenek indu i cyny): Dzięki tej przezroczystej warstwie przewodzącej panel może działać jak elektroda, regulując ilość przechodzącego przez niego światła.

Przygotowanie podłoża: Czystość podłoża szklanego ma pierwszorzędne znaczenie, dlatego poddaje się je dokładnemu czyszczeniu w celu usunięcia zanieczyszczeń, które mogłyby wpłynąć na jakość szkła węglowego.
Formacja Czarnej Macierzy: Nakładając warstwę fotorezystu na oczyszczone podłoże, fotolitografia jest wykorzystywana do zarysowania wzoru BM. Po naświetleniu, nierozwinięte obszary są ujawniane i wypełniane czarnym pigmentem, a następnie utwardzane.
Zastosowanie żywicy kolorowej: Kolejne nakładanie żywic w kolorze czerwonym, zielonym i niebieskim w obrębie BM odbywa się przy użyciu odrębnego procesu fotolitografii dla każdej warstwy koloru. Po powlekaniu i naświetlaniu obszary bez fotorezystu są wywoływane i wypełniane żywicą, a następnie utwardzane.
Aplikacja warstwy wierzchniej: Warstwa OC jest nakładana na żywicę w celu jej ochrony i uzyskania gładkiej powierzchni do późniejszego osadzania elektrod ITO.
Osadzanie elektrod ITO: Przezroczysta elektroda ITO jest nanoszona na warstwę OC metodą rozpylania jonowego, a następnie formowana w celu ustrukturyzowania architektury elektrody.
Kontrola i testowanie: Podczas produkcji skrupulatne kontrole i testy zapewniają jakość CF. Dokładnie badane są takie wskaźniki, jak wierność kolorów, jednolitość i poziomy defektów.
Integracja: Po przeprowadzeniu kontroli jakości filtr kolorów jest precyzyjnie wyrównywany i laminowany ze składnikami panelu TFT-LCD, takimi jak matryca TFT i warstwa ciekłokrystaliczna.

Przepływ segmentów CELL
Proces produkcyjny w ramach aspektu „komórki” wyświetlacza TFT można podzielić na cztery główne etapy: Wyrównanie, Boxing, Cięcie i Mocowanie polaryzatora. Cele i podstawowe procedury tych etapów są pokrótce opisane w następujący sposób:
Proces wyrównywania
Celem procesu Alignment jest utworzenie warstwy przezroczystej folii PI (poliimidowej) na podłożach TFT i CF. Poprzez późniejszy proces tarcia warstwa ta wpływa na cząsteczki ciekłego kryształu, aby wyrównały się w kierunku tarcia. Aby lepiej zrozumieć podstawowe zasady, zainteresowani czytelnicy powinni zapoznać się z odpowiednią literaturą. Dlatego też na tym etapie wyraźnie występują dwa główne procesy: drukowanie PI i pocieranie.
Drukowanie PI (poliimidowe)
Poliimid (PI) to wysokowydajny, transparentny organiczny materiał polimerowy składający się z łańcuchów głównych i bocznych. Po nałożeniu i wypaleniu mocno przylega do powierzchni podłoży CF i TFT. Powłoka PI wykorzystuje specjalną technikę druku wklęsłego. Oprócz podstawowego procesu druku wklęsłego druk PI obejmuje kilka procesów pomocniczych, w tym czyszczenie podłoża przed drukowaniem, wstępne wypalanie po drukowaniu, automatyczną kontrolę optyczną, utwardzanie, a także proces przeróbki PI, jeśli jest to konieczne.
1. Czyszczenie przed PI:Ten etap obejmuje dokładne oczyszczenie podłoża przed drukowaniem, aby upewnić się, że jest wolne od kurzu, tłuszczu i innych zanieczyszczeń, aby przygotować je do kolejnych kroków.
2. Drukowanie PI:W tym przypadku materiał PI (poliimid) jest nakładany na podłoże, podobnie jak w przypadku drukowania wzoru na papierze, z tą różnicą, że „atrament” jest specjalnym materiałem, który tworzy warstwę ochronną.3.Wstępne pieczenie:Należy to uważać za wstępną fazę wypiekania, która częściowo suszy warstwę PI, aby zapewnić odpowiednią przyczepność do podłoża.
4.Inspekcja PI:Na tym etapie zadrukowane warstwy są poddawane dokładnej kontroli w celu wykrycia plam, nierówności lub defektów – w sposób przypominający badanie niedoskonałości pomalowanej ściany.
5. Przeróbka PI:Jeśli podczas inspekcji zostaną zidentyfikowane jakiekolwiek problemy, ten krok wiąże się z koniecznością skorygowania niedoskonałości, co można porównać do wymazywania błędów na szkicu.
6. Utwardzanie PI:Na koniec warstwa PI zostaje całkowicie utwardzona w procesie wypalania, podobnym do procesu utwardzania gliny w piecu, co czyni ją wytrzymałą i trwałą.
Ten etap ma na celu usunięcie kurzu i cząstek z podłoża za pomocą ultradźwiękowego urządzenia czyszczącego, które wykorzystuje fale ultradźwiękowe do dokładnego czyszczenia. Zapewnia to, że podłoże jest wolne od wszelkich zanieczyszczeń przed przejściem do następnych kroków.
2. Wyrównanie:
Faza wyrównywania dostosowuje orientację podłoża, aby spełnić wymagania wizualne. Ten proces jest prosty, skupia się na prawidłowym ustawieniu podłoża do kolejnych zabiegów.
3. Pocieranie:
Podczas etapu pocierania, do pocierania warstwy PI używa się aksamitnej szmatki. Działanie to wyrównuje łańcuchy boczne PI w jednolitym kierunku, organizując strukturę molekularną w celu uzyskania pożądanych właściwości powierzchni.
4. Czyszczenie ultradźwiękowe po pocieraniu (USC):
Po pocieraniu podłoże może mieć cząstki stałe lub pozostałości. Czyszczenie USC po pocieraniu usuwa te pozostałości, zapewniając nieskazitelną czystość powierzchni podłoża. Ten krok jest krytyczny dla utrzymania jakości produktu końcowego, ponieważ wykorzystuje fale ultradźwiękowe do usuwania wszelkich cząstek lub pozostałości przyklejonych podczas procesu pocierania.

Proces kapsułkowania ODF (One Drop Fill)
1. Aplikacja uszczelniacza i pasty srebrnej:Klej utwardzany promieniami UV jest stosowany jako uszczelniacz, nakładany wzdłuż krawędzi podłoży szklanych CF i TFT, aby zapewnić, że oba podłoża są mocno połączone i określić grubość ogniwa. Jednocześnie nałożenie pasty srebrnej służy do łączenia wspólnych elektrod na CF i TFT, aby zapewnić łączność elektryczną.
2. Powłoka ciekłokrystaliczna:Materiał ciekłokrystaliczny jest nanoszony na podłoże TFT, które zostało już pokryte uszczelniaczem. Materiał ciekłokrystaliczny odgrywa kluczową rolę w procesie wyświetlania; dostosowuje stan przechodzącego światła, zmieniając jego układ, kontrolując w ten sposób kolor i jasność pikseli.
3. Spajanie próżniowe:Podłoże CF, które zostało pokryte uszczelniaczem, pastą srebrną i ciekłym kryształem, jest łączone z podłożem TFT w środowisku próżniowym. Ten krok pomaga zapobiegać tworzeniu się pęcherzyków i zapewnia ścisłe, bezszczelinowe połączenie między dwoma podłożami.
Utwardzanie termiczne:Po zakończeniu utwardzania UV podłoża przechodzą proces termiczny w celu dalszego wzmocnienia przyczepności uszczelniacza. Ten krok jest szczególnie ukierunkowany na obszary, do których światło UV nie dociera w pełni, takie jak obszary pod przewodami, zapewniając dokładne utwardzenie tych części.

1. Cięcie
Ze względu na określony rozmiar podłoża szklanego i różnorodność rozmiarów produktów, wiele komórek produktu jest rozmieszczonych na jednym podłożu szklanym. Cięcie odbywa się poprzez przesuwanie tarczy diamentowej po powierzchni szkła. Zazwyczaj po cięciu następuje proces odklejania, ale dzięki postępom w technologii tarcz tnących istnieje obecnie technika, która tworzy bardzo głęboki ślad cięcia, eliminując potrzebę odklejania.
2.Obrzeże
Po pocięciu szkła na pojedyncze sita, krawędzie każdego sita mają wiele drobnych pęknięć. Aby zapobiec pęknięciom spowodowanym przez zderzenia podczas późniejszego przenoszenia, konieczne jest obróbka krawędzi.
3.Pomiary elektryczne
Pomiar elektryczny to pomocniczy proces stosowany wielokrotnie w trakcie produkcji, ale jest on szczególnie istotny, ponieważ jest to pierwszy raz, gdy elektryczność jest stosowana do testowania wydajności wyświetlacza LCD. Zasada testowania jest prosta: należy podać elektryczność do poszczególnych pikseli wyświetlacza i obserwować wydajność wyświetlacza komórki przez folię polaryzacyjną. Zazwyczaj krótki pręt używany do testowania matrycy jest naelektryzowany. Po testach elektrycznych ekrany, które nie spełniają norm, są usuwane, aby zapobiec marnotrawstwu materiałów na późniejszych etapach.
Dodatkowe procesy pomocnicze obejmują wizualną kontrolę po cięciu i czyszczenie krawędzi.
Proces montażu modułu wyświetlacza TFT
Podstawowe procesy związane z montażem modułów wyświetlacza TFT obejmują nakładanie folii polaryzacyjnej, łączenie COG i FPC, montaż i różne procesy pomocnicze. Poniżej znajduje się szczegółowy wstęp do każdego z nich:
1. Wiązanie COG i FPC
COG (Chip on Glass) i FPC (Flexible Printed Circuit) to metody łączenia obwodów. Ze względu na mnogość elektrod tradycyjne połączenia przewodowe jeden do jednego są trudne. Obecna praktyka polega na tworzeniu układu elektrod na szkle, z odpowiadającym mu układem na IC/FPC i użyciu anizotropowej folii przewodzącej (ACF) do łączenia każdej elektrody IC/FPC z elektrodą szklaną, jedna po drugiej.2. Nakładanie folii polaryzacyjnej
Ponieważ działanie LCD opiera się na spolaryzowanym świetle, przymocowanie folii polaryzacyjnej jest niezbędnym procesem. Ta folia kontroluje światło przechodzące przez komórki ciekłokrystaliczne, aby wytwarzać obrazy.
3.Montaż
Montaż łączy podświetlenie, ekran, płytkę sterującą i inne komponenty, takie jak ekrany dotykowe, tworząc kompletny moduł wyświetlacza. Zazwyczaj odbywa się to ręcznie przez wykwalifikowanych techników, którzy odgrywają kluczową rolę w zapewnieniu jakości zmontowanych modułów.
Oprócz procesów głównych segment modułowy obejmuje szereg procesów pomocniczych, takich jak:
1.Cięcie laserowe i pomiary elektryczne po cięciu
Po precyzyjnym wycięciu komponentów za pomocą lasera przeprowadza się testy ich funkcji elektrycznych, aby upewnić się, że spełniają wymagane specyfikacje.2. Pomiary elektryczne łączenia i połączenia
Po procesie łączenia COG i FPC przeprowadza się również testy elektryczne w celu sprawdzenia integralności tych połączeń.
3.Inspekcja mikroskopowa
Po cięciu laserowym i spajaniu przeprowadzane są kontrole mikroskopowe (lub automatyczna kontrola optyczna (AOI) w przypadku spajania FPC), aby wykryć wszelkie wady lub problemy.
4. Test wytrzymałości na odrywanie
Po połączeniu IC i FPC przeprowadzane są testy wytrzymałości na odrywanie w celu oceny trwałości połączeń.
5. Starzenie się po montażu
Zmontowane moduły przechodzą proces starzenia z doprowadzeniem prądu w celu zapewnienia długoterminowej niezawodności.
6. Opakowanie i wysyłka
Gdy moduły przejdą wszystkie testy i kontrole, są pakowane i wysyłane do klienta lub do kolejnego etapu produkcji.

Najnowsze artykuły
-
OLED Technology 2025: Ultimate Guide, Price Analysis, and Future Trends
OLED Technology 2025: Ultimate Guide, Price Analysis, and Future Trends