
La structure de l'écran LCD TFT
Panneau à cristaux liquides (panneau):Il s'agit de la partie principale de l'écran, chargée de présenter l'image. Le panneau à cristaux liquides est formé de deux plaques de verre entre lesquelles est intercalée une couche de cristaux liquides, appelée cellule à cristaux liquides.
Filtres polarisants :Ces composants sont situés de part et d’autre de la cellule à cristaux liquides et sont chargés de traiter la lumière qui traverse la cellule.
Filtre de couleur:Habituellement fabriqué sur l'une des plaques de verre de la cellule à cristaux liquides scellée, il est utilisé pour l'affichage couleur.
Réseau de transistors à couches minces (réseau TFT):Posté sur l'autre plaque de verre de la cellule à cristaux liquides scellée, il joue un rôle actif dans le pilotage de l'affichage.
Rétroéclairage :La source lumineuse située derrière le module d'affichage TFT-LCD fournit la lumière nécessaire à la production de l'image visible à travers la cellule à cristaux liquides.
Circuit de lecteur externe :Ces circuits sont chargés de gérer les signaux d'image d'entrée pour piloter de manière appropriée la matrice TFT et le rétroéclairage.

Le processus de fabrication des écrans LCD TFT
Formation cinématographique:Des techniques telles que la pulvérisation cathodique (SPT) et le dépôt chimique en phase vapeur (CVD) déposent plusieurs couches sur le substrat.
Photolithographie:Application, exposition et développement de résine photosensible pour former des microstructures.
Gravure:Les méthodes de gravure humide et sèche sculptent le substrat en supprimant des zones spécifiques.
Décapage:Après le modelage, les matériaux excédentaires sont retirés pour nettoyer le substrat.
Étapes auxiliaires du processus :
Nettoyage:Assure que le substrat est exempt de contamination.
Marquage et exposition :Identifie et prépare les bords du substrat.
Inspection optique automatisée (AOI) :Utilisé pour l'inspection des défauts.
Inspection microscopique et inspection macroscopique (Mic/Mac) :Vérification détaillée.
Test de performance du film :Utilise des outils tels que des compteurs de résistance de feuille, des profilomètres, des réflectomètres/ellipsométrie, la spectroscopie infrarouge à transformée de Fourier.
Tests électriques ouverts/courts-circuits (O/S) :Vérifie la continuité du circuit et les courts-circuits. Test électrique du groupe d'éléments de test (TEG) : teste les performances électriques des éléments.
Tests électriques du réseau :Assure la fonctionnalité électrique du réseau.
Réparation au laser :Corrige tous les défauts en fonction des résultats de l’inspection.
Retouche de résine photosensible (Retouche PR) :Ajuste ou répète les étapes de photolithographie si nécessaire.
Refonte du film : modifie ou perfectionne le processus de formation du film si nécessaire.

Couche OC protège et prépare les motifs des filtres de couleur.
Couche RVB formation via des séquences de revêtement, d'exposition et de développement.
Couche BM (Black Matrix) améliore le contraste et limite les fuites de lumière.
Couche PS (Photo Spacer) maintient un espace précis entre les substrats, crucial pour la qualité de l'image.
Couche informatique ajoute un film conducteur transparent pour la conduction électrique et la fonctionnalité tactile.

Alignement et orientation du polyimide (PI):Application et orientation de la couche PI pour l'alignement des cristaux liquides.
ODF (Film d'affichage optique) améliore les effets visuels.
Nettoyage et application du produit d'étanchéité du cadre:Préparation à l'insertion de gouttelettes de cristaux liquides.
Injection de cristaux liquides:Distribuer avec précision le cristal liquide sur l'écran.
Laminage TFT et CF: Liaison des composants TFT et CF ensemble.
Séchage UV et traitement thermique:Solidification et répartition uniforme du cristal liquide avec lumière ultraviolette et traitement thermique.
Découpe, test électrique et lissage des bords: Mise en forme du substrat, réalisation de contrôles électriques et lissage des bords.
Fixation du polariseur et débullage:Application de films polarisants et élimination des bulles d'air, avec reprise autorisée si nécessaire.

Découpe laser et tests électriques: Assurer une forme précise et une intégrité électrique.
Collage COG (puce sur verre), collage et test FPC (circuit imprimé flexible):Installation et test du circuit de pilotage.
Assemblage et tests électriques:Combinaison de toutes les pièces du module d'affichage et réalisation des tests électriques finaux.
Vieillissement:Alimentation électrique à long terme pour garantir la fiabilité du produit.
Emballage et expédition:Préparation du produit fini pour la livraison.

Flux de segments de tableau
G : L'isolant de grille, fabriqué en SiNx (nitrure de silicium), fournit l'isolation nécessaire entre la grille et les autres couches.
I : La couche de canal, a-Si (silicium amorphe), où a lieu la commutation électronique.
N : La couche n+ a-Si est dopée avec une forte concentration de phosphine (PH3). Ce dopage réduit la barrière de potentiel à l'interface, garantissant un contact ohmique essentiel au fonctionnement fiable de l'appareil.

Métal de grille (AlNd/MoN)

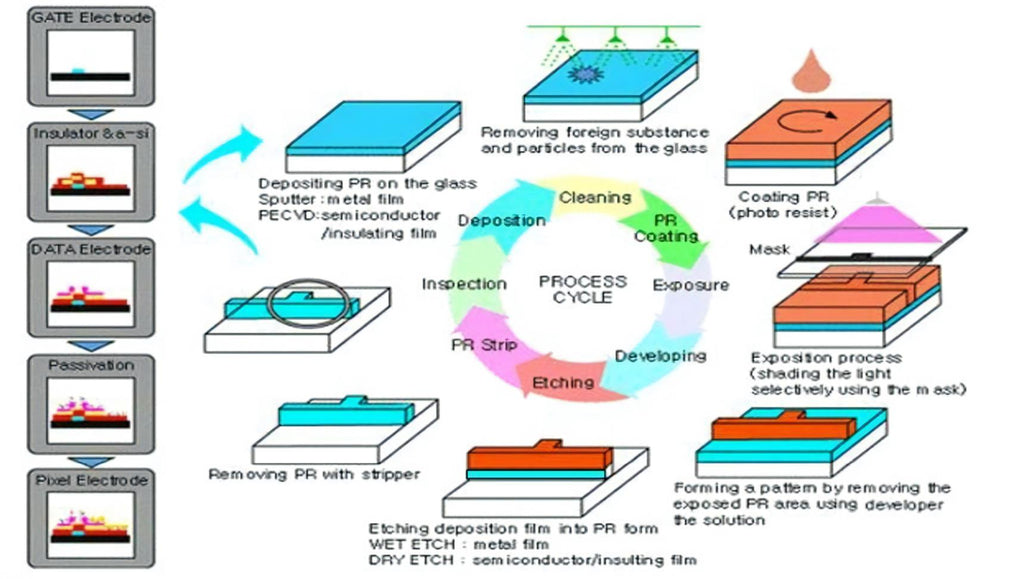
GIN (SiNx / a-Si / n+ a-Si)

Métal S/D (Mo\Al\Mo)
La formation des électrodes source et drain (S/D), de l'électrode de données et du canal comprend des procédures spécifiques telles que la stratification avec du nitrure de molybdène (MoN) et de l'aluminium pur (pour la source et le drain), la pulvérisation cathodique de la couche métallique S/D, la photolithographie S/D, la gravure humide S/D et la gravure sèche du canal. Grâce à ces processus, les électrodes source et drain, le canal et les lignes de données du TFT se forment sur le substrat en verre. À ce stade, la construction du TFT est terminée. La conception et le processus qui en résultent sont les suivants :
Pulvérisation S/D:Il s'agit d'une étape cruciale pour former des électrodes source/drain. Au cours de ce processus, une couche dense d'électrodes métalliques est formée en pulvérisant des ions de métaux lourds sur le substrat.
Nettoyage avant revêtement PR:Avant d'appliquer la résine photosensible, le substrat doit être nettoyé pour éliminer la poussière et les résidus, garantissant ainsi de bons résultats de revêtement.
DHP (plaque chauffante):Pour mieux fixer la résine photosensible au substrat, le substrat est préchauffé sur une plaque chauffante avant le processus de revêtement.
Revêtement résistant:Appliquez une couche de résine photosensible sur le substrat préchauffé, qui sera utilisée pour le dessin ultérieur des motifs.
Pré-durcissement (SHP):Le substrat revêtu de résine photosensible est pré-durci pour rendre la résine photosensible plus uniforme et plus résistante.
Exposition au stepper:Dans cette étape, la quantité d’exposition à la lumière est contrôlée pour durcir certaines zones de la résine photosensible et créer le motif souhaité.
Développement:La résine photosensible exposée est traitée pour révéler le motif.
Photorésist post-cuisson (HHP):Le motif de résine photosensible est encore durci et rendu plus visible grâce à un autre processus de chauffage. Cela peut également améliorer sa capacité à résister à la corrosion chimique et à l'usure.
Développement de l'inspection:Après le développement, une inspection détaillée est nécessaire pour garantir l'exactitude du modèle et détecter et résoudre rapidement tout problème.
Gravure humide:Il s’agit d’un processus de réaction chimique dans lequel un liquide corrosif est utilisé pour graver le matériau dans les zones non protégées afin de former le motif du circuit.
Gravure à sec du canal:Un canal est formé entre la source et le drain. Dans ce processus, le silicium dans la région du canal est gravé à la forme requise à l'aide d'une technique de gravure sèche.
Bande de résistance:Enfin, pour nettoyer la surface du substrat, la résine photosensible du substrat est retirée.
Après les étapes ci-dessus, les électrodes source/drain, les électrodes de données et le canal du TFT sont finalement formés sur le substrat en verre.
Passivation (SiNx)
La formation de la couche de passivation (SiNx), souvent appelée couche d'isolation protectrice, ainsi que des vias, comprend des opérations spécifiques telles que la formation de film PECVD, la photolithographie et la gravure à sec pour la création des vias. Après avoir suivi ces procédures, la couche d'isolation protectrice du canal TFT et les vias conducteurs sont finalement formés sur le substrat en verre. Les images et le processus obtenus après l'achèvement de ces étapes sont les suivants :
2. Nettoyage avant revêtement - C'est ici que le substrat est nettoyé avant l'application de la résine photosensible.
3. Précuisson sur plaque chauffante (DHP) - Cela implique l'utilisation d'une plaque chauffante pour préchauffer le substrat afin de le préparer à l'étape de revêtement.
4. Revêtement photosensible - Une couche de résine photosensible est appliquée sur le substrat au cours de cette étape.
5. Cuisson douce (SHP) - Le substrat, recouvert de résine photosensible, subit un processus de pré-durcissement pour solidifier la couche.
6. Exposition au stepper - Ici, la technologie de lithographie pas à pas est utilisée pour exposer la résine photosensible et former des motifs.
7. Développement - La résine photosensible exposée est traitée pour révéler le motif.
8. Cuisson dure (HHP) - Le motif photorésistant est durci grâce à un traitement post-cuisson.
9. Inspection post-développement - Cette étape consiste à inspecter le substrat développé pour confirmer l'exactitude des motifs.
10. Gravure humide - Les matériaux de couche mince indésirables sont éliminés via un processus de gravure chimique humide pour créer des motifs de circuit.
11. Décapage de résine photosensible - La résine photosensible est retirée et la surface du substrat est nettoyée.
12. Gravure des trous de contact (Gravure CH) - Les vias requis sont formés grâce à un processus de gravure à sec.
Voici les étapes détaillées impliquées dans la préparation du substrat pour les applications TFT, conduisant à la protection du canal TFT actif et à la formation de vias conducteurs.
Formation d'électrodes de pixels transparentes ITO (oxyde d'indium et d'étain)
La création d'électrodes de pixels transparentes dans les écrans TFT est un processus sophistiqué, qui commence par le dépôt d'oxyde d'indium-étain (ITO). Les étapes impliquées sont conçues avec précision et comprennent la pulvérisation de la couche d'ITO pour obtenir la transparence, suivie d'une photolithographie pour un motif complexe et se termine par une gravure humide pour finaliser la structure du pixel. Cette séquence méticuleuse se termine par la formation des électrodes de pixels, parfaitement intégrées sur le substrat en verre, marquant l'achèvement crucial du processus de matrice. Le flux de travail suivant détaille le raffinement et la séquence des opérations après l'achèvement du processus.
Dépôt de couches de pixels (pulvérisation ITO) – Établit un film conducteur transparent d’ITO (oxyde d’étain et d’indium) pour la création ultérieure de motifs de pixels.
Nettoyage du substrat (nettoyage avant revêtement de résine) – Assure la pureté du substrat avant d’appliquer le matériau photorésistant.
Préchauffage du substrat (plaque chauffante de déshydratation, DHP) – Prépare le substrat avec une étape de pré-cuisson pour une adhérence optimale de la résine photosensible.
Application de la résistance (revêtement) – Applique une couche uniforme de résine photosensible sur le substrat.
Soft Bake (pré-durcissement SHP) – Effectue un pré-durcissement pour solidifier la résine photosensible avant le modelage.
Exposition de précision (exposition pas à pas) – Utilise la photolithographie pas à pas pour exposer la résine photosensible, créant ainsi le motif souhaité.
Développement de modèles (en développement) – Développe la résine photosensible exposée pour révéler le motif de pixels complexe.
Résistance au durcissement (cuisson post-exposition, cuisson dure HHP) – Durcit la résine photosensible à motifs pour améliorer la résistance à la gravure.
Inspection des modèles (inspection post-développement) – Inspecte les modèles développés pour en vérifier l’exactitude et l’intégrité.
Transfert de motifs (gravure ITO) – Transfère le motif par gravure de la couche ITO pour former des électrodes de pixels.
Retrait de la résistance (bande) – Enlève la résine photosensible, laissant une surface de substrat propre.
Amélioration des performances (recuit) – Recuit les composants pour améliorer les propriétés électriques des transistors à couches minces.
Contrôle de qualité (test TEG) – Effectue des tests électriques sur les éléments d’essai pour surveiller la qualité pendant la production.
Cette séquence simplifiée pose les bases d’écrans TFT de haute qualité avec des performances électriques optimales.

Processus de filtrage de couleur (CF)
Substrat en verre : La couche de base fondamentale qui fournit un support mécanique.
Matrice noire (BM) : Constitué d'un matériau absorbant la lumière, il délimite chaque pixel et minimise les fuites de lumière entre les pixels, améliorant ainsi le contraste.
Couches de résine de couleur : En tant que filtres rouges, verts et bleus, ces couches déterminent les couleurs des pixels. Elles sont fabriquées à partir d'un matériau en résine transparente teintée.
Couche de recouvrement (OC) : Une couche protectrice superposée sur les résines de couleur pour uniformiser la surface et protéger les filtres des dommages physiques et chimiques.
Électrode ITO (oxyde d'étain et d'indium) : Cette couche conductrice transparente permet au panneau de fonctionner comme une électrode, régulant la lumière qui la traverse.

Préparation du substrat : La propreté du substrat en verre est primordiale, il subit donc un nettoyage en profondeur pour éradiquer les impuretés qui pourraient compromettre la qualité du CF.
Formation de la matrice noire : En appliquant une couche de résine photosensible sur le substrat nettoyé, la photolithographie est utilisée pour délimiter le motif BM. Après exposition, les zones non développées sont révélées et remplies de pigment noir, puis durcies.
Application de la résine colorée : L'application successive de résines de couleur rouge, verte et bleue dans les limites du BM est réalisée à l'aide d'un procédé de photolithographie distinct pour chaque couche de couleur. Après revêtement et exposition, les zones sans résine photosensible sont développées et remplies de résine, puis durcies.
Application de la couche de finition : Une couche OC est appliquée sur les couleurs de résine pour les protéger et établir une surface lisse pour le dépôt ultérieur d'électrodes ITO.
Dépôt d'électrodes ITO : L'électrode ITO transparente est déposée par pulvérisation cathodique sur la couche OC, puis modelée pour structurer l'architecture de l'électrode.
Inspection et test : Tout au long de la production, des contrôles et des tests minutieux garantissent la qualité du CF. Des paramètres tels que la fidélité des couleurs, l'uniformité et les niveaux de défauts sont minutieusement examinés.
Intégration: Après l'assurance qualité, le filtre couleur est précisément aligné et laminé avec les composants du panneau TFT-LCD tels que la matrice TFT et la couche de cristaux liquides.

Flux de segments CELL
Le processus de production de l'aspect « cellule » d'un écran TFT peut être grossièrement divisé en quatre étapes clés : l'alignement, la mise en boîte, la découpe et la fixation du polariseur. Les objectifs et les principales procédures de ces étapes sont brièvement décrits comme suit :
Le processus d'alignement
L'objectif du processus d'alignement est de créer une couche de film transparent PI (polyimide) sur les substrats TFT et CF. Grâce à un processus de friction ultérieur, cette couche influence les molécules de cristaux liquides pour qu'elles s'alignent dans la direction du frottement. Pour une compréhension plus approfondie des principes sous-jacents, les lecteurs intéressés doivent se référer à la littérature pertinente. Par conséquent, cette étape met en évidence deux processus principaux : l'impression PI et le frottement.
Impression PI (polyimide)
Le polyimide (PI) est un matériau polymère organique transparent à hautes performances composé de chaînes principales et latérales. Après application et cuisson, il adhère fermement aux surfaces des substrats CF et TFT. Le revêtement du PI utilise une technique d'impression par héliogravure spéciale. Outre le processus d'impression par héliogravure primaire, l'impression PI implique plusieurs processus auxiliaires, notamment le nettoyage du substrat avant l'impression, la précuisson après l'impression, l'inspection optique automatique, le durcissement, ainsi qu'un processus de retouche du PI si nécessaire.
1.Nettoyage pré-PI:Cette étape consiste à nettoyer soigneusement le support avant l’impression, en s’assurant qu’il est exempt de poussière, de graisse et d’autres contaminants pour le préparer aux étapes suivantes.
2.Impression PI:Ici, le matériau PI (polyimide) est appliqué sur le substrat, de manière analogue à l'impression d'un dessin sur du papier, sauf que « l'encre » est un matériau spécial qui forme une couche protectrice.3.Pré-cuisson:Considérez ceci comme une phase de cuisson préliminaire, qui sèche partiellement la couche PI pour assurer une bonne adhérence au substrat.
4.Inspection PI:À ce stade, les couches imprimées subissent un examen attentif pour détecter d’éventuelles taches, zones inégales ou défauts, un peu comme si l’on inspectait un mur peint à la recherche d’imperfections.
5. Refonte de PI:Si des problèmes sont identifiés lors de l’inspection, cette étape consiste à corriger ces imperfections, de la même manière que pour effacer les erreurs sur un croquis.
6. Durcissement PI:Enfin, la couche PI est entièrement durcie grâce à un processus de cuisson, un peu comme l’argile est durcie dans un four, la rendant solide et durable.
Cette étape vise à éliminer la poussière et les particules du substrat à l'aide d'un nettoyeur à ultrasons, qui utilise des ondes ultrasoniques pour un nettoyage en profondeur. Cela garantit que le substrat est exempt de tout contaminant avant de passer aux étapes suivantes.
2. Alignement :
La phase d'alignement permet d'ajuster l'orientation du substrat pour répondre aux exigences visuelles. Ce processus est simple et se concentre sur le positionnement correct du substrat pour les traitements ultérieurs.
3. Frottement :
Lors de l'étape de frottement, un chiffon de velours est utilisé pour frotter la couche de PI. Cette action aligne les chaînes latérales du PI dans une direction unifiée, organisant la structure moléculaire pour obtenir les propriétés de surface souhaitées.
4. Nettoyage par ultrasons après frottement (USC) :
Après le frottement, le substrat peut contenir des particules ou des résidus. Le nettoyage USC après frottement élimine ces résidus, garantissant ainsi une surface du substrat impeccablement propre. Cette étape est essentielle pour maintenir la qualité du produit final, car elle utilise des ondes ultrasoniques pour déloger et éliminer toutes les particules ou résidus collés pendant le processus de frottement.

Processus d'encapsulation ODF (One Drop Fill)
1. Application du mastic et de la pâte d'argent :Un adhésif durcissable aux UV est utilisé comme produit d'étanchéité, appliqué le long des bords des substrats en verre CF et TFT, pour garantir que les deux substrats sont fermement liés et pour définir l'épaisseur de la cellule. Simultanément, l'application de pâte d'argent sert à connecter les électrodes communes sur CF et TFT pour assurer la connectivité électrique.
2. Revêtement à cristaux liquides :Le matériau à cristaux liquides est déposé sur le substrat TFT déjà recouvert du produit d'étanchéité. Le matériau à cristaux liquides joue un rôle essentiel dans le processus d'affichage ; il ajuste l'état de la lumière qui le traverse en modifiant sa disposition, contrôlant ainsi la couleur et la luminosité des pixels.
3. Collage sous vide :Le substrat CF, qui a été recouvert de mastic, de pâte d'argent et de cristaux liquides, est lié au substrat TFT dans un environnement sous vide. Cette étape permet d'éviter la formation de bulles et garantit une liaison étanche et sans espace entre les deux substrats.
Durcissement thermique :Une fois le séchage UV terminé, les substrats subissent un traitement thermique pour renforcer encore l'adhérence du mastic. Cette étape vise particulièrement les zones qui ne sont pas entièrement atteintes par la lumière UV, comme sous les fils, afin de garantir que ces parties sont parfaitement durcies.

1. Découpe
En raison de la taille définie du substrat en verre et de la diversité des tailles de produits, plusieurs cellules de produits sont disposées sur un seul substrat en verre. La découpe est effectuée en faisant glisser une meule diamantée sur la surface du verre. Il y a généralement un processus de décollement après la découpe, mais grâce aux progrès de la technologie des meules de coupe, il existe désormais une technique qui crée une marque de coupe très profonde, éliminant ainsi le besoin de décollement.
2.Bordure
Une fois le verre découpé en panneaux individuels, les bords de chaque panneau présentent de nombreuses fissures fines. Pour éviter que ces fissures ne provoquent des bris dus à des collisions lors des manipulations ultérieures, un traitement des bords est nécessaire.
3. Mesure électrique
La mesure électrique est un processus auxiliaire utilisé à plusieurs reprises au cours de la production, mais elle est particulièrement cruciale ici, car c'est la première fois que l'électricité est appliquée pour tester les performances de l'écran LCD. Le principe de test est simple : appliquer de l'électricité aux pixels d'affichage individuels et observer les performances d'affichage de la cellule à travers un film polarisant. En général, une courte barre utilisée pour les tests de matrice est électrifiée. Après les tests électriques, les écrans qui ne répondent pas aux normes sont retirés pour éviter le gaspillage de matériaux lors des étapes ultérieures.
Les processus auxiliaires supplémentaires comprennent l'inspection visuelle après la coupe et le nettoyage après le bordage.
Processus d'assemblage du module d'affichage TFT
Les principaux processus impliqués dans l'assemblage des modules d'affichage TFT comprennent l'application du film polarisant, le collage COG et FPC, l'assemblage et divers processus de support. Vous trouverez ci-dessous une introduction détaillée à chacun d'eux :
1.Collage COG et FPC
Les circuits imprimés flexibles (COG, Chip on Glass) et les circuits imprimés flexibles (FPC, Flexible Printed Circuit) sont des méthodes de connexion de circuits. En raison de la multitude d'électrodes, les connexions filaires traditionnelles un à un sont difficiles. La pratique actuelle consiste à former un réseau d'électrodes sur le verre, avec un réseau correspondant sur le CI/FPC, et à utiliser un film conducteur anisotrope (ACF, Anisotropic Conductive Film) pour connecter chaque électrode du CI/FPC à l'électrode en verre une par une.2. Application du film polarisant
Le fonctionnement des écrans LCD étant basé sur la lumière polarisée, la fixation d'un film polarisant est un processus essentiel. Ce film contrôle la lumière traversant les cellules à cristaux liquides pour produire des images.
3.Assemblage
L'assemblage consiste à réunir le rétroéclairage, l'écran, le circuit imprimé de commande et d'autres composants tels que les écrans tactiles pour former un module d'affichage complet. Cette opération est généralement effectuée manuellement par des techniciens qualifiés, qui jouent un rôle crucial pour garantir la qualité des modules assemblés.
En plus des processus principaux, le segment du module comprend plusieurs processus auxiliaires, tels que :
1.Découpe laser et mesure électrique après découpe
Une fois les composants découpés avec précision au laser, leurs fonctions électriques sont testées pour garantir qu'ils répondent aux spécifications requises.2. Mesure électrique de liaison et de post-liaison
Des tests électriques sont également effectués après les processus de liaison COG et FPC pour vérifier l'intégrité de ces connexions.
3. Inspection microscopique
Après la découpe et le collage au laser, des inspections microscopiques (ou inspection optique automatisée (AOI) pour le collage FPC) sont effectuées pour vérifier d'éventuels défauts ou problèmes.
4. Test de résistance au pelage
Après le collage des circuits intégrés et des circuits intégrés flottants, des tests de résistance au pelage sont effectués pour évaluer la durabilité des liaisons.
5. Vieillissement après assemblage
Les modules assemblés subissent un processus de vieillissement sous tension pour garantir une fiabilité à long terme.
6. Emballage et expédition
Une fois que les modules ont passé tous les tests et inspections, ils sont emballés et expédiés au client ou à la phase suivante de production.

Derniers articles
-
OLED Technology 2025: Ultimate Guide, Price Analysis, and Future Trends
OLED Technology 2025: Ultimate Guide, Price Analysis, and Future Trends