
TFT एलसीडी डिस्प्ले की संरचना
लिक्विड क्रिस्टल पैनल (पैनल): यह डिस्प्ले का मुख्य भाग है, जो छवि को प्रस्तुत करने के लिए जिम्मेदार है। लिक्विड क्रिस्टल पैनल दो ग्लास प्लेटों से बना होता है, जिनके बीच लिक्विड क्रिस्टल की एक परत होती है, जिसे लिक्विड क्रिस्टल सेल के रूप में जाना जाता है।
ध्रुवीकरण फिल्टर:ये घटक लिक्विड क्रिस्टल सेल के दोनों ओर स्थित होते हैं और सेल से गुजरने वाले प्रकाश को संसाधित करने का कार्य करते हैं।
रंग फ़िल्टरआमतौर पर सीलबंद लिक्विड क्रिस्टल सेल की कांच की प्लेटों में से एक पर निर्मित, इसका उपयोग रंगीन प्रदर्शन के लिए किया जाता है।
पतली फिल्म ट्रांजिस्टर सरणी (TFT सरणी)सीलबंद लिक्विड क्रिस्टल सेल की दूसरी ग्लास प्लेट पर स्थित, यह डिस्प्ले को चलाने में सक्रिय भूमिका निभाता है।
बैकलाइट:टीएफटी-एलसीडी डिस्प्ले मॉड्यूल के पीछे स्थित प्रकाश स्रोत, लिक्विड क्रिस्टल सेल के माध्यम से दृश्यमान छवि उत्पन्न करने के लिए आवश्यक प्रकाश प्रदान करता है।
बाह्य ड्राइव सर्किटरी:ये सर्किट TFT सरणी और बैकलाइट को उचित रूप से चलाने के लिए इनपुट छवि संकेतों को प्रबंधित करने के प्रभारी होते हैं।

टीएफटी एलसीडी डिस्प्ले की विनिर्माण प्रक्रिया
फिल्म निर्माणस्पटरिंग (एसपीटी) और रासायनिक वाष्प जमाव (सीवीडी) जैसी तकनीकें सब्सट्रेट पर कई परतें जमा करती हैं।
फोटोलिथोग्राफीसूक्ष्म संरचनाएं बनाने के लिए फोटोरेसिस्ट का प्रयोग, उजागर करना और विकास करना।
एचिंगगीली और सूखी नक्काशी विधियां विशिष्ट क्षेत्रों को हटाकर सब्सट्रेट को आकार देती हैं।
अलग करनापैटर्निंग के बाद, सब्सट्रेट को साफ करने के लिए अतिरिक्त सामग्री को हटा दिया जाता है।
सहायक प्रक्रिया चरण:
सफाई:यह सुनिश्चित करता है कि सब्सट्रेट संदूषण से मुक्त है।
अंकन और एक्सपोजर:सब्सट्रेट किनारों की पहचान करना और उन्हें तैयार करना।
स्वचालित ऑप्टिकल निरीक्षण (एओआई):दोष निरीक्षण के लिए उपयोग किया जाता है।
सूक्ष्म निरीक्षण और स्थूल निरीक्षण (माइक/मैक):विस्तार से जाँच.
फिल्म प्रदर्शन परीक्षण:शीट प्रतिरोध मीटर, प्रोफिलोमीटर, रिफ्लेक्टोमीटर/इलिप्सोमेट्री, फूरियर-ट्रांसफॉर्म इन्फ्रारेड स्पेक्ट्रोस्कोपी जैसे उपकरणों का उपयोग करता है।
खुला/लघु (ओ/एस) विद्युत परीक्षण:सर्किट निरंतरता और शॉर्ट्स की जांच करता है। टेस्ट एलिमेंट ग्रुप (टीईजी) इलेक्ट्रिकल परीक्षण: तत्वों के विद्युत प्रदर्शन का परीक्षण करता है।
ऐरे विद्युत परीक्षण:सरणी की विद्युत कार्यक्षमता सुनिश्चित करता है।
लेज़र मरम्मत:निरीक्षण परिणामों के अनुसार किसी भी दोष को ठीक करता है।
फोटोरेसिस्ट रीवर्क (पीआर रीवर्क):यदि आवश्यक हो तो फोटोलिथोग्राफी चरणों को समायोजित या दोहराता है।
फिल्म पुनर्रचना: यदि आवश्यक हो तो फिल्म निर्माण प्रक्रिया में परिवर्तन या सुधार किया जाता है।

ओसी परत रंग फिल्टर पैटर्न की सुरक्षा और तैयारी करता है।
आरजीबी परत कोटिंग, एक्सपोजर और विकास अनुक्रम के माध्यम से गठन।
बीएम (ब्लैक मैट्रिक्स) परत कंट्रास्ट को बढ़ाता है और प्रकाश रिसाव को सीमित करता है।
पीएस (फोटो स्पेसर) परत सबस्ट्रेट्स के बीच सटीक अंतराल बनाए रखता है, जो छवि गुणवत्ता के लिए महत्वपूर्ण है।
आईटी परत विद्युत चालन और स्पर्श कार्यक्षमता के लिए एक पारदर्शी प्रवाहकीय फिल्म जोड़ता है।

पॉलीमाइड (पीआई) संरेखण और अभिविन्यास: लिक्विड क्रिस्टल संरेखण के लिए PI परत को लागू करना और उन्मुख करना।
ओडीएफ (ऑप्टिकल डिस्प्ले फिल्म) दृश्य प्रभाव में सुधार करता है.
सफ़ाई और फ़्रेम सीलेंट अनुप्रयोग: लिक्विड क्रिस्टल बूंद डालने की तैयारी।
लिक्विड क्रिस्टल इंजेक्शन: डिस्प्ले पर लिक्विड क्रिस्टल को सटीक रूप से वितरित करना।
टीएफटी और सीएफ लेमिनेशन: टीएफटी और सीएफ घटकों को एक साथ जोड़ना।
यूवी क्योरिंग और थर्मल प्रसंस्करणपराबैंगनी प्रकाश और ताप उपचार द्वारा लिक्विड क्रिस्टल को ठोस बनाना और समान रूप से वितरित करना।
काटना, विद्युत परीक्षण, और किनारा चिकना करनासब्सट्रेट को आकार देना, विद्युतीय जांच करना, और किनारों को चिकना करना।
पोलराइज़र अटैचमेंट और डिबबलिंगध्रुवीकरण फिल्म लगाना और हवा के बुलबुले हटाना, यदि आवश्यक हो तो पुनः कार्य की अनुमति।

लेजर कटिंग और इलेक्ट्रिकल परीक्षणसटीक आकार और विद्युत अखंडता सुनिश्चित करना।
सीओजी (चिप ऑन ग्लास) बॉन्डिंग, एफपीसी (फ्लेक्सिबल प्रिंटेड सर्किट) बॉन्डिंग और परीक्षणड्राइविंग सर्किटरी की स्थापना और परीक्षण।
असेंबली और इलेक्ट्रिकल परीक्षणसभी डिस्प्ले मॉड्यूल भागों को संयोजित करना और अंतिम विद्युत परीक्षण करना।
उम्र बढ़नाउत्पाद की विश्वसनीयता सुनिश्चित करने के लिए दीर्घकालिक विद्युत आपूर्ति।
पैकेजिंग और शिपिंग: तैयार उत्पाद को डिलीवरी के लिए तैयार करना।

सरणी खंड प्रवाह
G: SiNx (सिलिकॉन नाइट्राइड) से बना गेट इन्सुलेटर, गेट और अन्य परतों के बीच आवश्यक इन्सुलेशन प्रदान करता है।
I: चैनल परत, a-Si (अनाकार सिलिकॉन), जहां इलेक्ट्रॉनिक स्विचिंग होती है।
एन: एन+ ए-एसआई परत को फॉस्फीन (पीएच3) की उच्च सांद्रता के साथ डोप किया जाता है। यह डोपिंग इंटरफ़ेस पर संभावित अवरोध को कम करता है, जिससे ओमिक संपर्क सुनिश्चित होता है जो विश्वसनीय डिवाइस संचालन के लिए महत्वपूर्ण है।

गेट मेटल (AlNd/MoN)

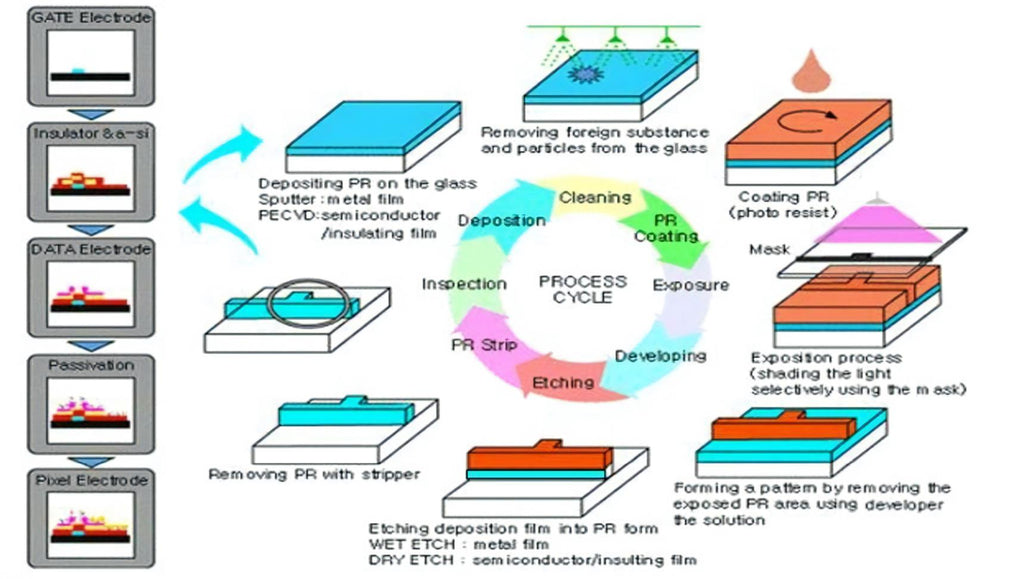
जीआईएन (SiNx / a-Si / n+ a-Si)

एस/डी धातु (Mo \Al\Mo)
स्रोत और नाली इलेक्ट्रोड (एस/डी), डेटा इलेक्ट्रोड और चैनल के निर्माण में मोलिब्डेनम नाइट्राइड (एमओएन) और शुद्ध एल्युमीनियम (स्रोत और नाली के लिए) के साथ लेयरिंग, एस/डी धातु परत की स्पटरिंग, एस/डी फोटोलिथोग्राफी, एस/डी गीली नक्काशी और चैनल सूखी नक्काशी जैसी विशिष्ट प्रक्रियाएं शामिल हैं। इन प्रक्रियाओं के माध्यम से, TFT के स्रोत और नाली इलेक्ट्रोड, चैनल और डेटा लाइनें ग्लास सब्सट्रेट पर बनती हैं। इस चरण में, TFT का निर्माण पूरा हो जाता है। परिणामी डिज़ाइन और प्रक्रिया इस प्रकार है:
एस/डी स्पटरिंग: यह स्रोत/नाली इलेक्ट्रोड बनाने के लिए एक महत्वपूर्ण कदम है। इस प्रक्रिया के दौरान, सब्सट्रेट पर भारी धातु आयनों को छिड़ककर धातु इलेक्ट्रोड की एक घनी परत बनाई जाती है।
पीआर कोटिंग से पहले सफाईफोटोरेसिस्ट लगाने से पहले, धूल और अवशेषों को हटाने के लिए सब्सट्रेट को साफ किया जाना चाहिए, ताकि अच्छे कोटिंग परिणाम सुनिश्चित हो सकें।
डीएचपी (हॉट प्लेट)फोटोरेसिस्ट को सब्सट्रेट से बेहतर ढंग से जोड़ने के लिए, कोटिंग प्रक्रिया से पहले सब्सट्रेट को गर्म प्लेट पर पहले से गरम किया जाता है।
प्रतिरोधी कोटिंगपूर्व-गर्म सब्सट्रेट पर फोटोरेसिस्ट की एक परत लगाएं, जिसका उपयोग बाद में पैटर्निंग के लिए किया जाता है।
प्री-क्योरिंग (एसएचपी)फोटोरेसिस्ट लेपित सब्सट्रेट को फोटोरेसिस्ट को अधिक एकसमान और मजबूत बनाने के लिए पूर्व-उपचारित किया जाता है।
स्टेपर एक्सपोजरइस चरण में, फोटोरेसिस्ट के कुछ क्षेत्रों को कठोर बनाने और वांछित पैटर्न बनाने के लिए प्रकाश के संपर्क की मात्रा को नियंत्रित किया जाता है।
विकासशीलउजागर फोटोरेसिस्ट को पैटर्न को प्रकट करने के लिए संसाधित किया जाता है।
फोटोरेसिस्ट पोस्ट बेकिंग (HHP)फोटोरेसिस्ट पैटर्न को एक और हीटिंग प्रक्रिया के माध्यम से और अधिक कठोर और अधिक प्रमुख बनाया जाता है। इससे रासायनिक क्षरण और घिसाव का प्रतिरोध करने की इसकी क्षमता में भी सुधार हो सकता है।
निरीक्षण का विकासविकसित करने के बाद, पैटर्न की सटीकता सुनिश्चित करने और किसी भी मुद्दे का तुरंत पता लगाने और उसका समाधान करने के लिए विस्तृत निरीक्षण की आवश्यकता होती है।
गीली नक्काशीयह एक रासायनिक प्रतिक्रिया प्रक्रिया है जिसमें संक्षारक तरल का उपयोग गैर-संरक्षित क्षेत्रों में सामग्री को खोदकर सर्किट पैटर्न बनाने के लिए किया जाता है।
चैनल ड्राई एचिंगस्रोत और नाली के बीच एक चैनल बनाया जाता है। इस प्रक्रिया में, चैनल क्षेत्र में सिलिकॉन को सूखी नक्काशी तकनीक का उपयोग करके आवश्यक आकार में उकेरा जाता है।
प्रतिरोध पट्टीअंत में, सब्सट्रेट की सतह को साफ करने के लिए, सब्सट्रेट पर लगे फोटोरेज़िस्ट को हटा दिया जाता है।
उपरोक्त चरणों के बाद, TFT के स्रोत/नाली इलेक्ट्रोड, डेटा इलेक्ट्रोड और चैनल अंततः ग्लास सब्सट्रेट पर बनाए जाते हैं।
निष्क्रियता (SiNx)
पैसिवेशन लेयर (SiNx) के निर्माण में, जिसे अक्सर सुरक्षात्मक इन्सुलेशन परत के रूप में जाना जाता है, विआस के साथ-साथ PECVD फिल्म निर्माण, फोटोलिथोग्राफी और विआ निर्माण के लिए सूखी नक्काशी जैसे विशिष्ट ऑपरेशन शामिल हैं। इन प्रक्रियाओं से गुजरने के बाद, TFT चैनल और प्रवाहकीय विआस के लिए सुरक्षात्मक इन्सुलेशन परत अंततः ग्लास सब्सट्रेट पर बनाई जाती है। इन चरणों के पूरा होने के बाद प्राप्त चित्र और प्रक्रिया इस प्रकार हैं:
2. कोटिंग से पहले सफाई - यह वह स्थान है जहां फोटोरेसिस्ट अनुप्रयोग से पहले सब्सट्रेट को साफ किया जाता है।
3. हॉटप्लेट प्रीबेक (डीएचपी) - इसमें कोटिंग चरण के लिए सब्सट्रेट को पहले से गर्म करने हेतु हॉटप्लेट का उपयोग किया जाता है।
4. फोटोरेसिस्ट कोटिंग - इस चरण के दौरान सब्सट्रेट पर फोटोरेसिस्ट की एक परत लगाई जाती है।
5. सॉफ्ट बेक (SHP) - फोटोरेसिस्ट से लेपित सब्सट्रेट, परत को ठोस बनाने के लिए प्री-क्योर प्रक्रिया से गुजरता है।
6. स्टेपर एक्सपोजर - यहां, फोटोरेसिस्ट को उजागर करने और पैटर्न बनाने के लिए स्टेपर लिथोग्राफी तकनीक का उपयोग किया जाता है।
7. विकासशील - उजागर फोटोरेजिस्ट को पैटर्न को प्रकट करने के लिए संसाधित किया जाता है।
8. हार्ड बेक (एचएचपी) - फोटोरेसिस्ट पैटर्न को पोस्ट-बेक उपचार के माध्यम से कठोर बनाया जाता है।
9. विकास के बाद निरीक्षण - इस चरण में पैटर्न की सटीकता की पुष्टि करने के लिए विकसित सब्सट्रेट का निरीक्षण करना शामिल है।
10. गीली नक्काशी - सर्किट पैटर्न बनाने के लिए गीली रासायनिक नक़्काशी प्रक्रिया के माध्यम से अवांछित पतली फिल्म सामग्री को हटा दिया जाता है।
11. फोटोरेसिस्ट स्ट्रिपिंग - फोटोरेसिस्ट को हटा दिया जाता है और सब्सट्रेट की सतह को साफ कर दिया जाता है।
12. संपर्क छेद नक़्क़ाशी (सीएच एचिंग) - आवश्यक विआज़ को शुष्क एचिंग प्रक्रिया के माध्यम से बनाया जाता है।
ये TFT अनुप्रयोगों के लिए सब्सट्रेट तैयार करने में शामिल विस्तृत चरण हैं, जिससे सक्रिय TFT चैनल की सुरक्षा और प्रवाहकीय मार्ग का निर्माण होता है।
पारदर्शी पिक्सेल इलेक्ट्रोड आईटीओ (इंडियम-टिन-ऑक्साइड) का निर्माण
TFT डिस्प्ले में पारदर्शी पिक्सेल इलेक्ट्रोड का निर्माण एक जटिल प्रक्रिया है, जिसकी शुरुआत इंडियम-टिन-ऑक्साइड (ITO) के जमाव से होती है। इसमें शामिल चरण सटीक रूप से इंजीनियर किए गए हैं और इसमें पारदर्शिता प्राप्त करने के लिए ITO परत को स्पटर करना, उसके बाद जटिल पैटर्निंग के लिए फोटोलिथोग्राफी और पिक्सेल संरचना को अंतिम रूप देने के लिए गीली नक्काशी के साथ समापन शामिल है। यह सावधानीपूर्वक अनुक्रम पिक्सेल इलेक्ट्रोड के निर्माण के साथ समाप्त होता है, जो ग्लास सब्सट्रेट पर दोषरहित रूप से एकीकृत होता है, जो सरणी प्रक्रिया के निर्णायक समापन को चिह्नित करता है। निम्नलिखित वर्कफ़्लो प्रक्रिया के पूरा होने के बाद संचालन के परिशोधन और अनुक्रम का विवरण देता है।
पिक्सेल परत अवक्षेपण (आईटीओ स्पटरिंग) - बाद में पिक्सेल पैटर्निंग के लिए आईटीओ (इंडियम टिन ऑक्साइड) की एक पारदर्शी प्रवाहकीय फिल्म स्थापित करता है।
सब्सट्रेट की सफाई (प्री-रेज़िस्ट कोटिंग क्लीन) - फोटोरेसिस्ट सामग्री को लागू करने से पहले सब्सट्रेट की शुद्धता सुनिश्चित करता है।
सब्सट्रेट प्रीहीटिंग (डिहाइड्रेशन हॉट प्लेट, डीएचपी) - इष्टतम फोटोरेसिस्ट आसंजन के लिए प्री-बेक चरण के साथ सब्सट्रेट तैयार करता है।
प्रतिरोध अनुप्रयोग (कोटिंग) - सब्सट्रेट पर एक समान फोटोरेसिस्ट परत लागू करता है।
सॉफ्ट बेक (प्री-क्योरिंग एसएचपी) - पैटर्निंग से पहले फोटोरेसिस्ट को ठोस बनाने के लिए प्री-क्योरिंग का संचालन करता है।
सटीक एक्सपोज़र (स्टेपर एक्सपोज़र) - फोटोरेसिस्ट को उजागर करने के लिए स्टेपर फोटोलिथोग्राफी का उपयोग करता है, जिससे वांछित पैटर्न बनता है।
पैटर्न विकास (विकासशील) - जटिल पिक्सेल पैटर्न को प्रकट करने के लिए उजागर फोटोरेजिस्ट विकसित करता है।
प्रतिरोध कठोरता (पोस्ट-एक्सपोजर बेक, हार्ड बेक एचएचपी) - नक़्काशी प्रतिरोध में सुधार करने के लिए पैटर्नयुक्त फोटोरेसिस्ट को कठोर बनाता है।
पैटर्न निरीक्षण (विकास के बाद निरीक्षण) – सटीकता और अखंडता के लिए विकसित पैटर्न का निरीक्षण करता है।
पैटर्न स्थानांतरण (आईटीओ एचिंग) - पिक्सेल इलेक्ट्रोड बनाने के लिए आईटीओ परत को नक्काशी करके पैटर्न को स्थानांतरित करता है।
प्रतिरोध हटाना (स्ट्रिप) - फोटोरेसिस्ट को हटा देता है, जिससे सब्सट्रेट की सतह साफ रह जाती है।
प्रदर्शन संवर्धन (एनीलिंग) - पतली फिल्म ट्रांजिस्टर के विद्युत गुणों को बढ़ाने के लिए घटकों को एनीलिंग करता है।
गुणवत्ता नियंत्रण (टीईजी परीक्षण) – उत्पादन के दौरान गुणवत्ता की निगरानी के लिए परीक्षण तत्वों पर विद्युत परीक्षण करता है।
यह सुव्यवस्थित अनुक्रम इष्टतम विद्युत प्रदर्शन के साथ उच्च गुणवत्ता वाले TFT डिस्प्ले के लिए आधार तैयार करता है।

रंग फ़िल्टर (सीएफ) प्रक्रिया
ग्लास सब्सट्रेट: आधारभूत आधार परत जो यांत्रिक समर्थन प्रदान करती है।
ब्लैक मैट्रिक्स (बीएम): प्रकाश-अवशोषित सामग्री से निर्मित, यह प्रत्येक पिक्सेल को चित्रित करता है और अंतर-पिक्सल प्रकाश रिसाव को न्यूनतम करता है, जिससे कंट्रास्ट में सुधार होता है।
रंग राल परतें: वास्तविक लाल, हरे और नीले रंग के फिल्टर के रूप में, ये परतें पिक्सेल के रंगों को निर्धारित करती हैं। इन्हें रंगे हुए पारदर्शी रेज़िन मटेरियल से तैयार किया जाता है।
ओवरकोट परत (OC): सतह को समतल करने और फिल्टर को भौतिक और रासायनिक नुकसान से बचाने के लिए रंगीन रेजिन पर एक सुरक्षात्मक परत चढ़ाई जाती है।
आईटीओ (इंडियम टिन ऑक्साइड) इलेक्ट्रोड: यह पारदर्शी प्रवाहकीय परत पैनल को इलेक्ट्रोड के रूप में कार्य करने में सक्षम बनाती है, जो इसके माध्यम से गुजरने वाले प्रकाश को नियंत्रित करती है।

सब्सट्रेट तैयारी: कांच के सब्सट्रेट की सफाई सर्वोपरि है, इसलिए सीएफ की गुणवत्ता से समझौता करने वाली अशुद्धियों को दूर करने के लिए इसकी गहन सफाई की जाती है।
ब्लैक मैट्रिक्स गठन: साफ किए गए सब्सट्रेट पर फोटोरेजिस्ट परत लगाकर, BM पैटर्न की रूपरेखा बनाने के लिए फोटोलिथोग्राफी का उपयोग किया जाता है। एक्सपोजर के बाद, अविकसित क्षेत्रों को उजागर किया जाता है और काले रंगद्रव्य से भर दिया जाता है, फिर ठीक किया जाता है।
रंग राल अनुप्रयोग: बीएम सीमाओं के भीतर लाल, हरे और नीले रंग के रेजिन का क्रमिक अनुप्रयोग प्रत्येक रंग परत के लिए एक अलग फोटोलिथोग्राफी प्रक्रिया का उपयोग करके किया जाता है। कोटिंग और एक्सपोज़र के बाद, फोटोरेसिस्ट के बिना क्षेत्रों को विकसित किया जाता है और राल से भर दिया जाता है, उसके बाद इलाज किया जाता है।
ओवरकोट परत अनुप्रयोग: रेजिन रंगों को सुरक्षित रखने तथा बाद में आईटीओ इलेक्ट्रोड जमाव के लिए चिकनी सतह स्थापित करने के लिए उनके ऊपर एक ओसी परत लगाई जाती है।
आईटीओ इलेक्ट्रोड जमाव: पारदर्शी आईटीओ इलेक्ट्रोड को ओसी परत पर जमा किया जाता है, फिर इलेक्ट्रोड संरचना की संरचना के लिए पैटर्न किया जाता है।
जांच और परीक्षण: उत्पादन के दौरान, सावधानीपूर्वक निरीक्षण और परीक्षण CF गुणवत्ता सुनिश्चित करते हैं। रंग निष्ठा, एकरूपता और दोष स्तर जैसे मेट्रिक्स की पूरी तरह से जांच की जाती है।
एकीकरण: गुणवत्ता आश्वासन के बाद, कलर फिल्टर को TFT-LCD पैनल घटकों जैसे TFT सरणी और लिक्विड क्रिस्टल परत के साथ सटीक रूप से संरेखित और लेमिनेट किया जाता है।

सेल खंड प्रवाह
TFT डिस्प्ले के 'सेल' पहलू के भीतर उत्पादन प्रक्रिया को मोटे तौर पर चार प्रमुख चरणों में विभाजित किया जा सकता है: संरेखण, बॉक्सिंग, कटिंग और पोलराइज़र अटैचमेंट। इन चरणों के उद्देश्य और प्राथमिक प्रक्रियाओं को संक्षेप में इस प्रकार बताया गया है:
संरेखण प्रक्रिया
संरेखण प्रक्रिया का उद्देश्य TFT और CF दोनों सब्सट्रेट पर पारदर्शी PI (पॉलीमाइड) फिल्म की एक परत बनाना है। बाद की घर्षण प्रक्रिया के माध्यम से, यह परत लिक्विड क्रिस्टल अणुओं को घर्षण की दिशा में संरेखित करने के लिए प्रभावित करती है। अंतर्निहित सिद्धांतों की गहरी समझ के लिए, इच्छुक पाठकों को प्रासंगिक साहित्य का संदर्भ लेना चाहिए। इसलिए, इस चरण में दो प्राथमिक प्रक्रियाएँ प्रमुख रूप से शामिल हैं: PI प्रिंटिंग और रबिंग।
पीआई (पॉलीइमाइड) मुद्रण
पॉलीइमाइड (PI) एक उच्च-प्रदर्शन, पारदर्शी कार्बनिक बहुलक पदार्थ है जिसमें मुख्य और साइड चेन शामिल हैं। आवेदन और बेकिंग के बाद, यह CF और TFT सब्सट्रेट की सतहों पर मजबूती से चिपक जाता है। PI की कोटिंग एक विशेष ग्रेव्योर प्रिंटिंग तकनीक का उपयोग करती है। प्राथमिक ग्रेव्योर प्रिंटिंग प्रक्रिया के अलावा, PI प्रिंटिंग में कई सहायक प्रक्रियाएँ शामिल हैं जिनमें प्रिंटिंग से पहले सब्सट्रेट की सफाई, प्रिंटिंग के बाद प्री-बेकिंग, स्वचालित ऑप्टिकल निरीक्षण, इलाज, साथ ही यदि आवश्यक हो तो PI रीवर्क प्रक्रिया शामिल है।
1.प्री-पीआई सफाईइस चरण में मुद्रण से पहले सब्सट्रेट को अच्छी तरह से साफ करना शामिल है, यह सुनिश्चित करना कि यह धूल, ग्रीस और अन्य संदूषकों से मुक्त है ताकि इसे अगले चरणों के लिए तैयार किया जा सके।
2.पीआई प्रिंटिंगयहां, पीआई (पॉलीइमाइड) सामग्री को सब्सट्रेट पर लागू किया जाता है, जो कागज पर एक डिजाइन को प्रिंट करने के समान है, सिवाय इसके कि 'स्याही' एक विशेष सामग्री है जो एक सुरक्षात्मक परत बनाती है।3. प्री-बेकिंगइसे प्रारंभिक बेकिंग चरण मानें, जो सब्सट्रेट पर उचित आसंजन सुनिश्चित करने के लिए PI परत को आंशिक रूप से सुखाता है।
4.पीआई निरीक्षणइस बिंदु पर, मुद्रित परतों की किसी भी प्रकार के धब्बे, असमान क्षेत्रों या दोषों के लिए बारीकी से जांच की जाती है, जो कि खामियों के लिए एक चित्रित दीवार का निरीक्षण करने के समान है।
5.पीआई पुनर्कार्ययदि निरीक्षण के दौरान कोई समस्या पाई जाती है, तो इस चरण में उन खामियों को ठीक करना शामिल है, ठीक वैसे ही जैसे किसी स्केच में गलतियों को मिटाना।
6.पीआई इलाजअंत में, पीआई परत को बेकिंग प्रक्रिया के माध्यम से पूरी तरह से कठोर कर दिया जाता है, ठीक उसी तरह जैसे मिट्टी को भट्ठी में कठोर किया जाता है, जिससे यह मजबूत और टिकाऊ हो जाती है।
इस चरण का उद्देश्य अल्ट्रासोनिक क्लीनर का उपयोग करके सब्सट्रेट से धूल और कणों को हटाना है, जो पूरी तरह से सफाई के लिए अल्ट्रासोनिक तरंगों का उपयोग करता है। यह सुनिश्चित करता है कि अगले चरणों पर आगे बढ़ने से पहले सब्सट्रेट किसी भी संदूषक से मुक्त हो।
2. संरेखण:
संरेखण चरण दृश्य आवश्यकताओं को पूरा करने के लिए सब्सट्रेट के अभिविन्यास को समायोजित करता है। यह प्रक्रिया सीधी है, जो बाद के उपचारों के लिए सब्सट्रेट को सही ढंग से रखने पर ध्यान केंद्रित करती है।
3. रगड़ना:
रगड़ने के चरण के दौरान, PI परत पर रगड़ने के लिए मखमली कपड़े का उपयोग किया जाता है। यह क्रिया PI की साइड चेन को एकीकृत दिशा में संरेखित करती है, जिससे वांछित सतह गुणों को प्राप्त करने के लिए आणविक संरचना को व्यवस्थित किया जाता है।
4. पोस्ट-रबिंग अल्ट्रासोनिक सफाई (यूएससी):
रगड़ने के बाद, सब्सट्रेट में कण पदार्थ या अवशेष हो सकते हैं। रगड़ने के बाद USC सफाई इन अवशेषों को हटा देती है, जिससे यह सुनिश्चित होता है कि सब्सट्रेट की सतह पूरी तरह से साफ है। यह कदम अंतिम उत्पाद की गुणवत्ता बनाए रखने के लिए महत्वपूर्ण है, क्योंकि यह रगड़ने की प्रक्रिया के दौरान चिपके किसी भी कण या अवशेष को हटाने और हटाने के लिए अल्ट्रासोनिक तरंगों का उपयोग करता है।

ओडीएफ (वन ड्रॉप फिल) एनकैप्सुलेशन प्रक्रिया
1. सीलेंट और सिल्वर पेस्ट अनुप्रयोग:यूवी-क्यूरेबल एडहेसिव का उपयोग सीलेंट के रूप में किया जाता है, जिसे सीएफ और टीएफटी ग्लास सबस्ट्रेट्स के किनारों पर लगाया जाता है, ताकि यह सुनिश्चित किया जा सके कि दोनों सबस्ट्रेट्स मजबूती से बंधे हुए हैं और सेल की मोटाई को परिभाषित किया जा सके। साथ ही, सिल्वर पेस्ट का उपयोग सीएफ और टीएफटी पर आम इलेक्ट्रोड को जोड़ने के लिए किया जाता है ताकि विद्युत कनेक्टिविटी सुनिश्चित की जा सके।
2. लिक्विड क्रिस्टल कोटिंग:लिक्विड क्रिस्टल मटेरियल को TFT सब्सट्रेट पर गिराया जाता है, जिस पर पहले से ही सीलेंट की कोटिंग की गई होती है। लिक्विड क्रिस्टल मटेरियल डिस्प्ले प्रक्रिया में महत्वपूर्ण भूमिका निभाता है; यह प्रकाश की स्थिति को बदलकर उसकी व्यवस्था को समायोजित करता है, जिससे पिक्सल के रंग और चमक को नियंत्रित किया जा सकता है।
3. वैक्यूम बॉन्डिंग:CF सब्सट्रेट, जिसे सीलेंट, सिल्वर पेस्ट और लिक्विड क्रिस्टल के साथ लेपित किया गया है, वैक्यूम वातावरण में TFT सब्सट्रेट के साथ जुड़ा हुआ है। यह कदम बुलबुले के गठन को रोकने में मदद करता है और यह सुनिश्चित करता है कि दो सब्सट्रेट के बीच एक तंग, गैपलेस बॉन्ड है।
थर्मल क्योरिंग:यूवी क्योरिंग पूरा होने के बाद, सब्सट्रेट को सीलेंट के आसंजन को और मजबूत करने के लिए एक थर्मल प्रक्रिया से गुजरना पड़ता है। यह कदम विशेष रूप से उन क्षेत्रों पर लक्षित है जो यूवी प्रकाश द्वारा पूरी तरह से नहीं पहुँच पाते हैं, जैसे कि लीड के नीचे, यह सुनिश्चित करना कि ये हिस्से पूरी तरह से ठीक हो गए हैं।

1.काटना
ग्लास सब्सट्रेट के निश्चित आकार और उत्पाद के आकार में विविधता के कारण, एक ही ग्लास सब्सट्रेट पर कई उत्पाद सेल व्यवस्थित किए जाते हैं। कांच की सतह पर हीरे के पहिये को खिसकाकर कटिंग की जाती है। आम तौर पर कटिंग के बाद एक डीबॉन्डिंग प्रक्रिया होती है, लेकिन कटिंग व्हील तकनीक में प्रगति के साथ, अब एक ऐसी तकनीक है जो बहुत गहरा कट मार्क बनाती है, जिससे डीबॉन्डिंग की आवश्यकता समाप्त हो जाती है।
2. किनारा
कांच को अलग-अलग स्क्रीन में काटने के बाद, प्रत्येक स्क्रीन के किनारों पर कई बारीक दरारें होती हैं। बाद में हैंडलिंग में टकराव के कारण इन दरारों के टूटने से बचने के लिए, किनारों का उपचार आवश्यक है।
3.विद्युत माप
विद्युत मापन एक सहायक प्रक्रिया है जिसका उपयोग उत्पादन के दौरान कई बार किया जाता है, लेकिन यह यहाँ विशेष रूप से महत्वपूर्ण है क्योंकि यह पहली बार है जब एलसीडी के प्रदर्शन प्रदर्शन का परीक्षण करने के लिए बिजली का उपयोग किया जाता है। परीक्षण सिद्धांत सरल है: अलग-अलग डिस्प्ले पिक्सल पर बिजली लागू करें और एक ध्रुवीकरण फिल्म के माध्यम से सेल के प्रदर्शन प्रदर्शन का निरीक्षण करें। आम तौर पर, सरणी परीक्षण के लिए उपयोग की जाने वाली एक छोटी पट्टी को विद्युतीकृत किया जाता है। विद्युत परीक्षण के बाद, बाद के चरणों में सामग्री की बर्बादी को रोकने के लिए मानकों को पूरा नहीं करने वाली स्क्रीन को हटा दिया जाता है।
अतिरिक्त सहायक प्रक्रियाओं में काटने के बाद दृश्य निरीक्षण और किनारा लगाने के बाद सफाई शामिल है।
टीएफटी डिस्प्ले मॉड्यूल असेंबली प्रक्रिया
TFT डिस्प्ले मॉड्यूल की असेंबली में शामिल प्राथमिक प्रक्रियाओं में ध्रुवीकरण फिल्म, COG और FPC बॉन्डिंग, असेंबली और विभिन्न सहायक प्रक्रियाओं का अनुप्रयोग शामिल है। नीचे प्रत्येक का विस्तृत परिचय दिया गया है:
1.सीओजी और एफपीसी बॉन्डिंग
COG (चिप ऑन ग्लास) और FPC (फ्लेक्सिबल प्रिंटेड सर्किट) सर्किट को जोड़ने के तरीके दर्शाते हैं। इलेक्ट्रोड की बहुलता के कारण, पारंपरिक एक-से-एक तार कनेक्शन चुनौतीपूर्ण हैं। वर्तमान अभ्यास में ग्लास पर एक इलेक्ट्रोड सरणी बनाना, IC/FPC पर एक संगत सरणी बनाना और प्रत्येक IC/FPC इलेक्ट्रोड को एक-एक करके ग्लास इलेक्ट्रोड से जोड़ने के लिए अनिसोट्रोपिक कंडक्टिव फिल्म (ACF) का उपयोग करना शामिल है।2. ध्रुवीकरण फिल्म लगाना
चूंकि एलसीडी का संचालन ध्रुवीकृत प्रकाश पर आधारित है, इसलिए ध्रुवीकरण फिल्म का जुड़ना एक आवश्यक प्रक्रिया है। यह फिल्म लिक्विड क्रिस्टल कोशिकाओं से गुज़रने वाले प्रकाश को नियंत्रित करती है ताकि छवियां बनाई जा सकें।
3.असेंबली
असेंबली बैकलाइट, स्क्रीन, कंट्रोल सर्किट बोर्ड और टचस्क्रीन जैसे अन्य घटकों को एक साथ लाकर एक पूर्ण डिस्प्ले मॉड्यूल बनाती है। यह आमतौर पर कुशल तकनीशियनों द्वारा मैन्युअल रूप से किया जाता है, जो इकट्ठे मॉड्यूल की गुणवत्ता सुनिश्चित करने में महत्वपूर्ण भूमिका निभाते हैं।
मुख्य प्रक्रियाओं के अतिरिक्त, मॉड्यूल खंड में कई सहायक प्रक्रियाएं शामिल हैं, जैसे:
1.लेजर कटिंग और कटिंग के बाद विद्युत माप
लेज़र का उपयोग करके घटकों को सटीक रूप से काटने के बाद, उनके विद्युत कार्यों का परीक्षण किया जाता है ताकि यह सुनिश्चित किया जा सके कि वे आवश्यक विनिर्देशों को पूरा करते हैं।2.बॉन्डिंग और पोस्ट-बॉन्डिंग विद्युत माप
इन कनेक्शनों की अखंडता को सत्यापित करने के लिए सीओजी और एफपीसी बॉन्डिंग प्रक्रियाओं के बाद विद्युत परीक्षण भी किया जाता है।
3.सूक्ष्म निरीक्षण
लेजर कटिंग और बॉन्डिंग के बाद, किसी भी दोष या समस्या की जांच के लिए सूक्ष्म निरीक्षण (या एफपीसी बॉन्डिंग के लिए स्वचालित ऑप्टिकल निरीक्षण (एओआई)) किया जाता है।
4.छीलने की शक्ति परीक्षण
आईसी बॉन्डिंग और एफपीसी बॉन्डिंग के बाद, बॉन्ड के स्थायित्व का मूल्यांकन करने के लिए पील स्ट्रेंथ परीक्षण किया जाता है।
5.असेंबली के बाद उम्र बढ़ना
संयोजित मॉड्यूल्स को दीर्घकालिक विश्वसनीयता सुनिश्चित करने के लिए शक्ति प्रदान करते हुए आयु-वृद्धि प्रक्रिया से गुजरना पड़ता है।
6. पैकेजिंग और शिपमेंट
एक बार जब मॉड्यूल सभी परीक्षणों और निरीक्षणों में सफल हो जाते हैं, तो उन्हें पैक करके ग्राहक या उत्पादन के अगले चरण में भेज दिया जाता है।

नवीनतम लेख
-
OLED Technology 2025: Ultimate Guide, Price Analysis, and Future Trends
OLED Technology 2025: Ultimate Guide, Price Analysis, and Future Trends