
Ang istraktura ng TFT LCD display
Liquid Crystal Panel (Panel): Ito ang pangunahing bahagi ng display, na responsable sa pagpapakita ng imahe. Ang likidong kristal na panel ay nabuo sa pamamagitan ng dalawang salamin na plato na may isang layer ng likidong kristal na nasa pagitan ng mga ito, na kilala bilang likidong kristal na selula.
Mga polarizing filter:Ang mga sangkap na ito ay matatagpuan sa magkabilang panig ng likidong kristal na selula at may tungkuling iproseso ang liwanag na dumadaan sa selula.
Filter ng Kulay: Karaniwang gawa sa isa sa mga glass plate ng selyadong likidong kristal na cell, ito ay ginagamit para sa pagpapakita ng kulay.
Thin Film Transistor Array (TFT Array): Nakaposisyon sa kabilang glass plate ng sealed liquid crystal cell, gumaganap ito ng aktibong papel sa pagmamaneho ng display.
Backlight:Ang pinagmumulan ng liwanag na matatagpuan sa likod ng TFT-LCD display module ay nagbibigay ng liwanag na kinakailangan para sa nakikitang imahe na magawa sa pamamagitan ng likidong kristal na selula.
Panlabas na Drive Circuitry:Ang mga circuit na ito ang namamahala sa mga signal ng input na imahe upang naaangkop na i-drive ang TFT array at backlight.

Ang proseso ng pagmamanupaktura ng TFT LCD display
Pagbuo ng Pelikula: Ang mga diskarte tulad ng Sputtering (SPT) at Chemical Vapor Deposition (CVD) ay nagdeposito ng maraming layer sa substrate.
Photolithography: Paglalapat, paglalantad, at pagbuo ng photoresist upang bumuo ng mga microstructure.
Pag-ukit: Ang basa at tuyo na mga pamamaraan ng pag-ukit ay nililok ang substrate sa pamamagitan ng pag-alis ng mga partikular na lugar.
Paghuhubad: Pagkatapos ng pattern, ang mga labis na materyales ay tinanggal upang linisin ang substrate.
Mga hakbang sa proseso ng auxiliary:
Paglilinis:Tinitiyak na ang substrate ay libre mula sa kontaminasyon.
Pagmamarka at Exposure:Kinikilala at inihahanda ang mga gilid ng substrate.
Automated Optical Inspection (AOI):Ginagamit para sa inspeksyon ng depekto.
Microscopic Inspection at Macroscopic Inspection (Mic/Mac):Pagsusuri ng detalye.
Pagsubok sa Pagganap ng Pelikula:Gumagamit ng mga tool tulad ng sheet resistance meter, profileometers, reflectometers/elipsometry, Fourier-transform infrared spectroscopy.
Open/Short (O/S) Electrical Testing:Sinusuri ang pagpapatuloy ng circuit at shorts.Test Element Group (TEG) Electrical Testing: Sinusuri ang electrical performance ng mga elemento.
Array Electrical Testing:Tinitiyak ang electrical functionality ng array.
Pag-aayos ng Laser:Itinatama ang anumang mga depekto ayon sa mga resulta ng inspeksyon.
Photoresist Rework (PR Rework):Isinasaayos o inuulit ang mga hakbang sa photolithography kung kinakailangan.
Film Rework: Binabago o ginagawang perpekto ang proseso ng pagbuo ng pelikula kung kinakailangan.

OC Layer pinoprotektahan at inihahanda ang mga pattern ng filter ng kulay.
RGB Layer pagbuo sa pamamagitan ng patong, pagkakalantad, at pagkakasunud-sunod ng pag-unlad.
BM (Black Matrix) Layer pinapahusay ang contrast at nililimitahan ang light leakage.
PS (Photo Spacer) Layer nagpapanatili ng tumpak na agwat sa pagitan ng mga substrate, mahalaga para sa kalidad ng imahe.
ITO Layer nagdaragdag ng transparent na conductive film para sa electrical conduction at touch functionality.

Polyimide (PI) Alignment at Oryentasyon: Paglalapat at pag-orient sa layer ng PI para sa pagkakahanay ng likidong kristal.
ODF (Optical Display Film) nagpapabuti ng mga visual effect.
Aplikasyon sa Paglilinis at Frame Sealant: Paghahanda para sa pagpapasok ng likidong kristal na patak.
Liquid Crystal Injection: Eksaktong pag-display ng likidong kristal sa display.
TFT at CF Lamination: Pagsasama-sama ng mga bahagi ng TFT at CF.
UV Curing at Thermal Processing: Pagpapatigas at pantay na pamamahagi ng likidong kristal na may ultraviolet light at heat treatment.
Pagputol, Pagsusuri sa Elektrisidad, at Pagpapakinis ng Gilid: Paghuhubog sa substrate, pagsasagawa ng mga electrical check, at pagpapakinis ng mga gilid.
Polarizer Attachment at Debubbling: Paglalapat ng mga polarizing film at pag-aalis ng mga bula ng hangin, na pinapayagan ang muling paggawa kung kinakailangan.

Laser Cutting at Electrical Testing: Tinitiyak ang tumpak na hugis at integridad ng kuryente.
COG (Chip On Glass) Bonding, FPC (Flexible Printed Circuit) Bonding at Pagsubok: Pag-install at pagsubok sa circuitry sa pagmamaneho.
Assembly at Electrical Testing: Pinagsasama-sama ang lahat ng bahagi ng display module at pagsasagawa ng mga huling pagsusuri sa kuryente.
Pagtanda: Pangmatagalang supply ng kuryente upang matiyak ang pagiging maaasahan ng produkto.
Packaging at Pagpapadala: Paghahanda ng tapos na produkto para sa paghahatid.

Daloy ng segment ng array
G: Ang gate insulator, na gawa sa SiNx (Silicon Nitride), ay nagbibigay ng kinakailangang pagkakabukod sa pagitan ng gate at iba pang mga layer.
I: Ang layer ng channel, a-Si (amorphous Silicon), kung saan nagaganap ang electronic switching.
N: Ang layer ng n+ a-Si ay doped na may mataas na konsentrasyon ng Phosphine (PH3). Binabawasan ng doping na ito ang potensyal na hadlang sa interface, tinitiyak ang isang Ohmic contact na mahalaga para sa maaasahang operasyon ng device.

Gate Metal (AlNd/MoN)

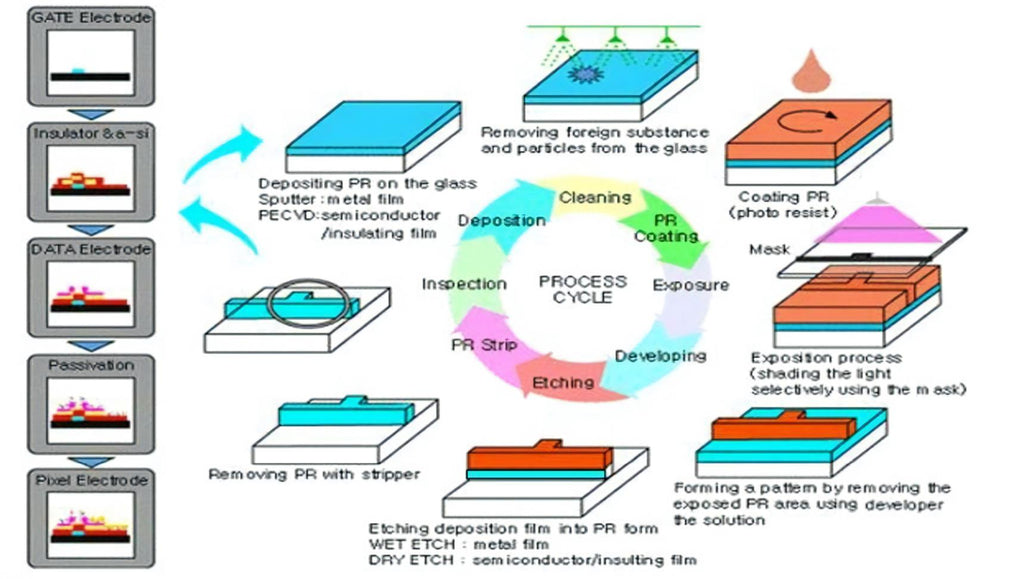
GIN (SiNx / a-Si / n+ a-Si)

S/D Metal (Mo \Al\Mo)
Kasama sa pagbuo ng source at drain electrodes (S/D), data electrode, at channel ang mga partikular na pamamaraan tulad ng layering na may Molybdenum Nitride (MoN) at pure Aluminum (para sa source at drain), sputtering ng S/D metal layer, S/D photolithography, S/D wet etching, at channel dry etching. Sa pamamagitan ng mga prosesong ito, ang source at drain electrodes, channel, at mga linya ng data ng TFT ay nabuo sa glass substrate. Sa yugtong ito, natapos ang pagtatayo ng TFT. Ang resultang disenyo at proseso ay ang mga sumusunod:
S/D Sputtering: Ito ay isang mahalagang hakbang upang makabuo ng mga electrodes na pinagmumulan/alisan ng tubig. Sa prosesong ito, ang isang siksik na layer ng mga metal na electrodes ay nabuo sa pamamagitan ng pag-sputtering ng mga heavy metal ions papunta sa substrate.
Paglilinis bago ang PR Coating: Bago mag-apply ng photoresist, dapat linisin ang substrate upang maalis ang alikabok at residues, na tinitiyak ang magandang resulta ng coating.
DHP (Hot Plate): Upang mas mahusay na ilakip ang photoresist sa substrate, ang substrate ay pre-heated sa isang mainit na plato bago ang proseso ng patong.
Lumalaban sa Patong: Maglagay ng layer ng photoresist sa pre-heated substrate, na ginagamit para sa kasunod na patterning.
Pre-curing (SHP): Ang photoresist coated substrate ay pre-cured para gawing mas pare-pareho at mas malakas ang photoresist.
Stepper Exposure: Sa hakbang na ito, ang dami ng light exposure ay kinokontrol upang tumigas ang ilang bahagi ng photoresist at lumikha ng gustong pattern.
Nagpapaunlad: Ang nakalantad na photoresist ay pinoproseso upang ipakita ang pattern.
Photoresist Post Baking (HHP): Ang pattern ng photoresist ay lalong tumigas at ginawang mas kitang-kita sa pamamagitan ng isa pang proseso ng pag-init. Mapapabuti rin nito ang kakayahang labanan ang kaagnasan at pagkasira ng kemikal.
Pagbuo ng Inspeksyon: Pagkatapos ng pagbuo, kailangan ang isang detalyadong inspeksyon upang matiyak ang katumpakan ng pattern at agad na matukoy at matugunan ang anumang mga isyu.
Basang Ukit: Ito ay isang proseso ng kemikal na reaksyon kung saan ginagamit ang isang corrosive na likido upang mag-ukit ng materyal sa mga hindi protektadong lugar upang mabuo ang pattern ng circuit.
Channel Dry Etching: Ang isang channel ay nabuo sa pagitan ng pinagmulan at alisan ng tubig. Sa prosesong ito, ang silikon sa rehiyon ng channel ay nakaukit sa kinakailangang hugis gamit ang isang dry etching technique.
Labanan ang Strip: Panghuli, upang linisin ang ibabaw ng substrate, ang photoresist sa substrate ay tinanggal.
Pagkatapos ng mga hakbang sa itaas, ang source/drain electrodes, data electrodes, at channel ng TFT ay sa wakas ay nabuo sa glass substrate.
Pasivation (SiNx)
Ang pagbuo ng passivation layer (SiNx), na kadalasang kilala bilang protective insulation layer, kasama ang vias, ay kinabibilangan ng mga partikular na operasyon gaya ng PECVD film formation, photolithography, at dry etching para sa pamamagitan ng paglikha. Matapos dumaan sa mga pamamaraang ito, ang proteksiyon na layer ng pagkakabukod para sa TFT channel at ang conductive vias ay sa wakas ay nabuo sa glass substrate. Ang mga larawan at prosesong nakuha pagkatapos makumpleto ang mga hakbang na ito ay ang mga sumusunod:
2. Pre-Coating Cleaning - Ito ay kung saan ang substrate ay nalinis bago ang photoresist application.
3. Hotplate Prebake (DHP) - Kabilang dito ang paggamit ng isang hotplate upang painitin muna ang substrate upang maghanda para sa hakbang ng patong.
4. Photoresist Coating - Ang isang layer ng photoresist ay inilapat sa ibabaw ng substrate sa yugtong ito.
5. Soft Bake (SHP) - Ang substrate, na pinahiran ng photoresist, ay sumasailalim sa proseso ng pre-cure upang patigasin ang layer.
6. Stepper Exposure - Dito, ginagamit ang teknolohiya ng stepper lithography upang ilantad ang mga pattern ng photoresist at form.
7. Pagbuo - Ang nakalantad na photoresist ay pinoproseso upang ipakita ang pattern.
8. Hard Bake (HHP) - Ang pattern ng photoresist ay tumigas sa pamamagitan ng isang post-bake treatment.
9. Post-Develop Inspection - Ang yugtong ito ay nagsasangkot ng pag-inspeksyon sa nabuong substrate upang kumpirmahin ang katumpakan ng mga pattern.
10. Basang Pag-ukit - Ang mga hindi gustong thin film na materyales ay inaalis sa pamamagitan ng isang wet chemical etching process upang lumikha ng mga pattern ng circuit.
11. Photoresist Stripping - Ang photoresist ay tinanggal at ang ibabaw ng substrate ay nalinis.
12. Contact Hole Etching (CH Etching) - Ang mga kinakailangang vias ay nabuo sa pamamagitan ng dry etching process.
Ito ang mga detalyadong hakbang na kasangkot sa paghahanda ng substrate para sa mga aplikasyon ng TFT, na humahantong sa proteksyon ng aktibong TFT channel at pagbuo ng conductive vias.
Pagbuo ng transparent pixel electrode ITO (Indium-Tin-Oxide)
Ang paglikha ng mga transparent pixel electrodes sa TFT display ay isang sopistikadong proseso, simula sa pag-deposition ng Indium-Tin-Oxide (ITO). Ang mga yugto na kasangkot ay precision-engineered at kasama ang pag-sputtering sa layer ng ITO upang makamit ang transparency, na sinusundan ng photolithography para sa masalimuot na patterning, at nagtapos sa wet etching upang i-finalize ang pixel structure. Ang maselang pagkakasunud-sunod na ito ay nagtatapos sa pagbuo ng mga pixel electrodes, na walang kamali-mali na isinama sa glass substrate, na minarkahan ang pivotal na pagkumpleto ng proseso ng array. Ang sumusunod na daloy ng trabaho ay nagdedetalye ng pagpipino at pagkakasunud-sunod ng mga operasyon pagkatapos ng pagkumpleto ng proseso.
Pixel Layer Deposition (ITO Sputtering) – Nagtatatag ng transparent na conductive film ng ITO (Indium Tin Oxide) para sa kasunod na pixel patterning.
Paglilinis ng Substrate (Pre-Resist Coating Clean) – Tinitiyak ang kadalisayan ng substrate bago ilapat ang materyal na photoresist.
Pag-init ng Substrate (Dehydration Hot Plate, DHP) – Inihahanda ang substrate na may pre-bake step para sa pinakamainam na photoresist adhesion.
Resist Application (Coating) – Naglalagay ng pare-parehong photoresist layer sa substrate.
Soft Bake (Pre-curing SHP) – Nagsasagawa ng pre-curing upang patigasin ang photoresist bago i-pattern.
Precision Exposure (Stepper Exposure) – Gumagamit ng stepper photolithography upang ilantad ang photoresist, na lumilikha ng nais na pattern.
Pagbuo ng Pattern (Pagbuo) - Binubuo ang nakalantad na photoresist upang ipakita ang masalimuot na pattern ng pixel.
Labanan ang Harden (Post-exposure Bake, Hard Bake HHP) – Pinapatigas ang patterned photoresist upang mapabuti ang etch resistance.
Pag-inspeksyon ng Pattern (Pag-inspeksyon pagkatapos ng pag-unlad) – Sinusuri ang mga nabuong pattern para sa katumpakan at integridad.
Paglilipat ng Pattern (ITO Etching) – Inilipat ang pattern sa pamamagitan ng pag-ukit sa layer ng ITO upang bumuo ng mga electrodes ng pixel.
Labanan ang Pag-alis (Strip) – Tinatanggal ang photoresist, na nag-iiwan ng malinis na ibabaw ng substrate.
Pagpapahusay ng Pagganap (Pagsusubo) – Inilalagay ang mga sangkap upang mapahusay ang mga katangian ng elektrikal ng mga transistor ng manipis na pelikula.
Quality Control (TEG Test) – Nagsasagawa ng mga pagsusuring elektrikal sa mga elemento ng pagsubok upang masubaybayan ang kalidad sa panahon ng produksyon.
Ang naka-streamline na pagkakasunud-sunod na ito ay naglalatag ng batayan para sa mga de-kalidad na TFT display na may pinakamainam na pagganap ng kuryente.

Proseso ng Color Filter (CF).
Glass Substrate: Ang foundational base layer na nagbibigay ng mekanikal na suporta.
Black Matrix (BM): Binubuo ng light-absorbing material, binibigyang-diin nito ang bawat pixel at pinapaliit ang inter-pixel light leakage, na pinapabuti ang contrast.
Mga Layer ng Resin ng Kulay: Bilang ang aktwal na pula, berde, at kulay asul na mga filter, tinutukoy ng mga layer na ito ang mga kulay ng pixel. Ang mga ito ay ginawa mula sa isang tinina na transparent na materyal ng dagta.
Overcoat Layer (OC): Isang proteksiyon na layer na naka-overlay sa mga kulay na resin upang pantayin ang ibabaw at protektahan ang mga filter mula sa pisikal at kemikal na pinsala.
ITO (Indium Tin Oxide) Electrode: Ang transparent na conductive layer na ito ay nagbibigay-daan sa panel na gumana bilang isang electrode, na kinokontrol ang liwanag na dumadaan.

Paghahanda ng substrate: Ang kalinisan ng glass substrate ay pinakamahalaga, kaya ito ay sumasailalim sa masusing paglilinis upang matanggal ang mga dumi na maaaring makompromiso ang kalidad ng CF.
Pagbuo ng Black Matrix: Ang paglalapat ng isang photoresist layer sa nalinis na substrate, ang photolithography ay ginagamit upang balangkasin ang pattern ng BM. Pagkatapos ng pagkakalantad, ang mga hindi pa nabuong lugar ay inihayag at napuno ng itim na pigment, pagkatapos ay gumaling.
Application ng Color Resin: Ang sunud-sunod na paglalagay ng pula, berde, at asul na kulay na resins sa loob ng BM confines ay ginagawa gamit ang isang natatanging proseso ng photolithography para sa bawat layer ng kulay. Pagkatapos ng patong at pagkakalantad, ang mga lugar na walang photoresist ay binuo at puno ng dagta, na sinusundan ng paggamot.
Application ng Overcoat Layer: Ang isang layer ng OC ay inilapat sa ibabaw ng mga kulay ng dagta upang protektahan ang mga ito at magtatag ng isang makinis na ibabaw para sa kasunod na ITO electrode deposition.
ITO Electrode Deposition: Ang transparent na elektrod ng ITO ay naka-sputter-deposited papunta sa layer ng OC, pagkatapos ay naka-pattern upang mabuo ang arkitektura ng elektrod.
Inspeksyon at Pagsubok: Sa buong produksyon, tinitiyak ng masusing inspeksyon at pagsusuri ang kalidad ng CF. Ang mga sukatan tulad ng katapatan ng kulay, pagkakapareho, at mga antas ng depekto ay lubusang sinusuri.
Pagsasama: Pagkatapos ng katiyakan sa kalidad, ang Filter ng Kulay ay tiyak na nakahanay at nakalamina sa mga nasasakupan ng TFT-LCD panel tulad ng TFT array at ang likidong kristal na layer.

Daloy ng Segment ng CELL
Ang proseso ng produksyon sa loob ng 'Cell' na aspeto ng isang TFT display ay maaaring halos nahahati sa apat na pangunahing yugto: Alignment, Boxing, Cutting, at Polarizer Attachment. Ang mga layunin at pangunahing pamamaraan ng mga yugtong ito ay binalangkas nang maikli gaya ng sumusunod:
Ang Proseso ng Pag-align
Ang layunin ng proseso ng Alignment ay lumikha ng isang layer ng transparent na PI (Polyimide) na pelikula sa parehong TFT at CF substrates. Sa pamamagitan ng isang kasunod na proseso ng friction, ang layer na ito ay nakakaimpluwensya sa mga likidong kristal na molekula upang ihanay sa direksyon ng friction. Para sa isang mas malalim na pag-unawa sa pinagbabatayan na mga prinsipyo, ang mga interesadong mambabasa ay dapat sumangguni sa mga nauugnay na literatura. Samakatuwid, ang yugtong ito ay kitang-kitang nagtatampok ng dalawang pangunahing proseso: PI Printing at Rubbing.
Pag-imprenta ng PI(Polyimide).
Ang Polyimide (PI) ay isang high-performance, transparent na organikong polymer na materyal na binubuo ng mga pangunahing at side chain. Pagkatapos ng aplikasyon at pagluluto sa hurno, ito ay mahigpit na nakadikit sa mga ibabaw ng CF at TFT substrates. Ang coating ng PI ay gumagamit ng espesyal na gravure printing technique. Bukod sa pangunahing proseso ng pag-print ng gravure, ang pag-print ng PI ay nagsasangkot ng ilang mga pantulong na proseso kabilang ang paglilinis ng substrate bago ang pag-print, pre-baking pagkatapos ng pag-print, awtomatikong optical inspeksyon, paggamot, pati na rin ang proseso ng muling paggawa ng PI kung kinakailangan.
1.Pre-PI Cleaning:Ang hakbang na ito ay nagsasangkot ng masusing paglilinis ng substrate bago mag-print, tinitiyak na ito ay libre mula sa alikabok, grasa, at iba pang mga contaminant upang maihanda ito para sa mga susunod na hakbang.
2.PI Printing: Dito, ang PI (Polyimide) na materyal ay inilapat sa substrate, na kahalintulad sa pag-print ng isang disenyo sa papel, maliban sa 'tinta' ay isang espesyal na materyal na bumubuo ng proteksiyon na layer.3.Pre-Baking:Isaalang-alang ito bilang isang paunang yugto ng pagluluto sa hurno, na bahagyang natutuyo sa layer ng PI upang matiyak ang wastong pagdikit sa substrate.
4.PI Inspeksyon:Sa puntong ito, ang mga naka-print na layer ay sumasailalim sa masusing pagsusuri para sa anumang mga dumi, hindi pantay na lugar, o mga depekto, na katulad ng pag-inspeksyon sa isang pininturahan na pader para sa mga di-kasakdalan.
5.PI Rework:Kung may anumang mga isyu na natukoy sa panahon ng inspeksyon, ang hakbang na ito ay nangangailangan ng pagwawasto sa mga imperpeksyon na iyon, katulad ng pagbubura ng mga pagkakamali sa isang sketch.
6.PI Curing:Sa wakas, ang PI layer ay ganap na tumigas sa pamamagitan ng proseso ng pagbe-bake, katulad ng clay na pinatigas sa isang tapahan, na ginagawa itong malakas at matibay.
Ang yugtong ito ay naglalayong alisin ang alikabok at mga particle mula sa substrate gamit ang isang ultrasonic cleaner, na gumagamit ng mga ultrasonic wave para sa masusing paglilinis. Tinitiyak nito na ang substrate ay libre mula sa anumang mga kontaminant bago magpatuloy sa mga susunod na hakbang.
2. Pag-align:
Inaayos ng yugto ng pagkakahanay ang oryentasyon ng substrate upang matupad ang mga visual na kinakailangan. Ang prosesong ito ay diretso, na nakatuon sa pagpoposisyon ng substrate nang tama para sa mga kasunod na paggamot.
3. Pagkuskos:
Sa yugto ng rubbing, isang velvet cloth ang ginagamit upang kuskusin ang layer ng PI. Ang pagkilos na ito ay nakahanay sa mga side chain ng PI sa isang pinag-isang direksyon, na nag-aayos ng molekular na istraktura upang makamit ang ninanais na mga katangian sa ibabaw.
4. Post-Rubbing Ultrasonic Cleaning (USC):
Pagkatapos kuskusin, ang substrate ay maaaring may particulate matter o residues. Ang post-rubbing USC cleaning ay nag-aalis ng mga nalalabi na ito, na tinitiyak na ang ibabaw ng substrate ay walang kamali-mali na malinis. Ang hakbang na ito ay kritikal para sa pagpapanatili ng kalidad ng panghuling produkto, dahil gumagamit ito ng mga ultrasonic wave upang iwaksi at alisin ang anumang mga particle o residues na nakadikit sa proseso ng pagkuskos.

ODF(One Drop Fill) Proseso ng Encapsulation
1. Aplikasyon ng Sealant at Silver Paste:Ginagamit ang UV-curable adhesive bilang sealant, na inilapat sa mga gilid ng CF at TFT glass substrates, upang matiyak na ang dalawang substrate ay mahigpit na nakagapos at upang tukuyin ang kapal ng cell. Sabay-sabay, ang application ng silver paste ay para sa pagkonekta sa mga karaniwang electrodes sa CF at TFT upang matiyak ang electrical connectivity.
2. Liquid Crystal Coating:Ang likidong kristal na materyal ay ibinabagsak sa TFT substrate na nalagyan na ng sealant. Ang likidong kristal na materyal ay gumaganap ng isang kritikal na papel sa proseso ng pagpapakita; inaayos nito ang estado ng liwanag na dumadaan sa pamamagitan ng pagbabago ng pagkakaayos nito, sa gayon ay kinokontrol ang kulay at ningning ng mga pixel.
3. Vacuum Bonding:Ang substrate ng CF, na pinahiran ng sealant, silver paste, at likidong kristal, ay nakatali sa TFT substrate sa isang vacuum na kapaligiran. Ang hakbang na ito ay nakakatulong na pigilan ang pagbuo ng mga bula at tinitiyak na mayroong masikip, walang gap na buklod sa pagitan ng dalawang substrate.
Thermal Curing:Matapos makumpleto ang UV curing, ang mga substrate ay sumasailalim sa isang thermal na proseso upang higit pang palakasin ang pagdirikit ng sealant. Ang hakbang na ito ay partikular na naglalayong sa mga lugar na hindi ganap na naaabot ng UV light, tulad ng sa ilalim ng mga lead, na tinitiyak na ang mga bahaging ito ay lubusang gumaling.

1.Pagputol
Dahil sa tiyak na laki ng glass substrate at sa iba't ibang laki ng produkto, maraming mga cell ng produkto ang nakaayos sa isang glass substrate. Ang pagputol ay ginagawa sa pamamagitan ng pag-slide ng isang brilyante na gulong sa ibabaw ng salamin. Karaniwang mayroong proseso ng pag-debonding pagkatapos ng pagputol, ngunit sa mga pagsulong sa teknolohiya ng pagputol ng gulong, mayroon na ngayong isang pamamaraan na lumilikha ng napakalalim na marka ng hiwa, na inaalis ang pangangailangan para sa pag-debonding.
2.Edging
Matapos maputol ang salamin sa mga indibidwal na screen, ang mga gilid ng bawat screen ay may maraming pinong bitak. Upang maiwasan ang mga bitak na ito na magdulot ng pagkabasag dahil sa mga banggaan sa kasunod na paghawak, kinakailangan ang edging treatment.
3.Electrical na Pagsukat
Ang pagsukat ng elektrisidad ay isang pantulong na proseso na ginagamit nang maraming beses sa panahon ng produksyon, ngunit ito ay lalong mahalaga dito dahil ito ang unang pagkakataon na gumamit ng kuryente upang subukan ang pagganap ng display ng LCD. Ang prinsipyo ng pagsubok ay simple: maglapat ng kuryente sa mga indibidwal na display pixel at obserbahan ang pagganap ng display ng cell sa pamamagitan ng isang polarizing film. Karaniwan, ang isang maikling bar na ginagamit para sa array testing ay nakuryente. Pagkatapos ng electrical testing, ang mga screen na hindi nakakatugon sa mga pamantayan ay aalisin upang maiwasan ang pag-aaksaya ng mga materyales sa mga susunod na yugto.
Ang mga karagdagang pantulong na proseso ay kinabibilangan ng post-cutting visual inspection at post-edging na paglilinis.
Proseso ng Pagpupulong ng TFT Display Module
Kasama sa mga pangunahing prosesong kasangkot sa pag-assemble ng TFT display modules ang paggamit ng polarizing film, COG at FPC bonding, assembly, at iba't ibang supportive na proseso. Nasa ibaba ang isang detalyadong panimula sa bawat isa:
1.COG at FPC Bonding
Ang COG (Chip on Glass) at FPC (Flexible Printed Circuit) ay kumakatawan sa mga paraan ng pagkonekta ng mga circuit. Dahil sa dami ng mga electrodes, mahirap ang tradisyonal na one-to-one wire connections. Ang kasalukuyang pagsasanay ay nagsasangkot ng pagbuo ng isang electrode array sa salamin, na may kaukulang array sa IC/FPC, at paggamit ng Anisotropic Conductive Film (ACF) upang ikonekta ang bawat IC/FPC electrode sa glass electrode nang paisa-isa.2.Paglalapat Ang Polarizing Film
Dahil ang pagpapatakbo ng LCD ay batay sa polarized na ilaw, ang attachment ng isang polarizing film ay isang mahalagang proseso. Kinokontrol ng pelikulang ito ang liwanag na dumadaan sa mga likidong kristal na selula upang makagawa ng mga imahe.
3.Assembly
Pinagsasama-sama ng Assembly ang backlight, screen, control circuit board, at iba pang bahagi tulad ng mga touchscreen upang bumuo ng kumpletong module ng display. Karaniwan itong ginagawa nang manu-mano ng mga bihasang technician, na gumaganap ng mahalagang papel sa pagtiyak ng kalidad ng mga naka-assemble na module.
Bilang karagdagan sa mga pangunahing proseso, kasama sa segment ng module ang ilang mga pantulong na proseso, tulad ng:
1.Laser Cutting at Post-Cutting Electrical Measurement
Matapos ang mga bahagi ay tiyak na pinutol gamit ang isang laser, ang kanilang mga electrical function ay nasubok upang matiyak na natutugunan nila ang mga kinakailangang detalye.2. Pagsusukat ng Elektrikal na Pagbubuklod at Pagkakatapos ng Pagbubuklod
Ginagawa rin ang electrical testing pagkatapos ng COG at FPC bonding process para ma-verify ang integridad ng mga koneksyong ito.
3.Microscopic Inspection
Pagkatapos ng laser cutting at bonding, ang mga mikroskopikong inspeksyon (o Automated Optical Inspection (AOI) para sa FPC bonding) ay isinasagawa upang suriin kung may mga depekto o isyu.
4.Pagsubok sa Lakas ng Balat
Pagkatapos ng IC bonding at FPC bonding, ang mga pagsusuri sa lakas ng balat ay ginagawa upang suriin ang tibay ng mga bono.
5.Aging After Assembly
Ang mga naka-assemble na module ay sumasailalim sa proseso ng pagtanda na may kapangyarihang inilapat upang matiyak ang pangmatagalang pagiging maaasahan.
6.Packaging at Pagpapadala
Kapag ang mga module ay pumasa sa lahat ng mga pagsubok at inspeksyon, sila ay nakabalot at ipinadala sa customer o sa susunod na yugto ng produksyon.

Mga pinakabagong artikulo
-
OLED Technology 2025: Ultimate Guide, Price Analysis, and Future Trends
OLED Technology 2025: Ultimate Guide, Price Analysis, and Future Trends