
Strukturen för TFT LCD-skärm
Flytande kristallpanel (panel): Detta är huvuddelen av displayen, ansvarig för att presentera bilden. Den flytande kristallpanelen bildas av två glasplattor med ett lager av flytande kristaller inklämt mellan dem, känd som flytande kristallcellen.
Polariserande filter:Dessa komponenter är placerade på båda sidor av den flytande kristallcellen och har till uppgift att bearbeta ljuset som passerar genom cellen.
Färgfilter: Vanligtvis tillverkad på en av glasplattorna i den förseglade flytande kristallcellen, denna används för färgvisning.
Thin Film Transistor Array (TFT Array): Placerad på den andra glasplattan i den förseglade flytande kristallcellen spelar den en aktiv roll för att driva displayen.
Bakgrundsbelysning:Ljuskällan som finns bakom TFT-LCD-displaymodulen ger det ljus som krävs för att den synliga bilden ska produceras genom flytande kristallcellen.
Extern drivkrets:Dessa kretsar är ansvariga för att hantera de ingående bildsignalerna för att på lämpligt sätt driva TFT-matrisen och bakgrundsbelysningen.

Tillverkningsprocessen för TFT LCD-skärmar
Filmbildning: Tekniker som Sputtering (SPT) och Chemical Vapor Deposition (CVD) avsätter flera lager på substratet.
Fotolitografi: Applicering, exponering och framkallning av fotoresist för att bilda mikrostrukturer.
Etsning: Våt- och torretsningsmetoder skulpterar substratet genom att ta bort specifika områden.
Strippning: Efter mönstring avlägsnas överflödigt material för att rengöra underlaget.
Hjälpprocesssteg:
Rengöring:Säkerställer att underlaget är fritt från kontaminering.
Märkning och exponering:Identifierar och förbereder underlagets kanter.
Automatiserad optisk inspektion (AOI):Används för defektkontroll.
Mikroskopisk inspektion och makroskopisk inspektion (Mic/Mac):Detaljkontroll.
Test av filmprestanda:Använder verktyg som arkresistansmätare, profilometrar, reflektometrar/ellipsometri, Fourier-transform infraröd spektroskopi.
Öppen/kort (O/S) elektrisk testning:Kontrollerar kretskontinuitet och kortslutningar.Test Element Group (TEG) Elektrisk testning: Testar elementens elektriska prestanda.
Matris elektrisk testning:Säkerställer arrayens elektriska funktionalitet.
Laserreparation:Åtgärdar eventuella defekter enligt besiktningsresultat.
Photoresist Rework (PR Rework):Justerar eller upprepar fotolitografistegen vid behov.
Filmomarbetning: Ändrar eller fulländar filmbildningsprocessen vid behov.

OC-lager skyddar och förbereder färgfiltermönstren.
RGB-lager bildning via beläggning, exponering och utvecklingssekvenser.
BM (Black Matrix) Layer förbättrar kontrasten och begränsar ljusläckage.
PS (Photo Spacer) Layer upprätthåller exakta gap mellan substraten, avgörande för bildkvaliteten.
IT-lager lägger till en transparent ledande film för elektrisk ledning och beröringsfunktionalitet.

Polyimid (PI) uppriktning och orientering: Applicera och orientera PI-skiktet för flytande kristallinriktning.
ODF (Optical Display Film) förbättrar visuella effekter.
Applicering av rengöring och ramtätning: Förbereder för införande av flytande kristalldroppar.
Injektion av flytande kristaller: Exakt dispensering av flytande kristaller på displayen.
TFT & CF laminering: Bindning av TFT- och CF-komponenterna.
UV-härdning och termisk bearbetning: Stelnar och fördelar den flytande kristallen jämnt med ultraviolett ljus och värmebehandling.
Skärning, elektrisk testning och kantutjämning: Forma underlaget, utföra elektriska kontroller och jämna ut kanter.
Polarisatorfäste & avbubbling: Applicering av polariserande filmer och eliminering av luftbubblor, med omarbetning tillåten vid behov.

Laserskärning & elektrisk testning: Säkerställer exakt form och elektrisk integritet.
COG (Chip On Glass) Limning, FPC (Flexible Printed Circuit) Bonding & Testing: Installera och testa drivkretsen.
Montering & Elprovning: Kombinera alla delar av displaymodulen och utför slutliga elektriska tester.
Åldrande: Långsiktig strömförsörjning för att säkerställa produktens tillförlitlighet.
Förpackning & Frakt: Förbereda den färdiga produkten för leverans.

Matrissegmentflöde
G: Portisolatorn, gjord av SiNx (Silicon Nitride), ger nödvändig isolering mellan grinden och andra lager.
I: Kanalskiktet, a-Si (amorft kisel), där den elektroniska omkopplingen sker.
N: n+ a-Si-skiktet är dopat med en hög koncentration av fosfin (PH3). Denna dopning minskar den potentiella barriären vid gränssnittet, vilket säkerställer en ohmsk kontakt som är avgörande för tillförlitlig drift av enheten.

Gate Metal (AlNd/MoN)

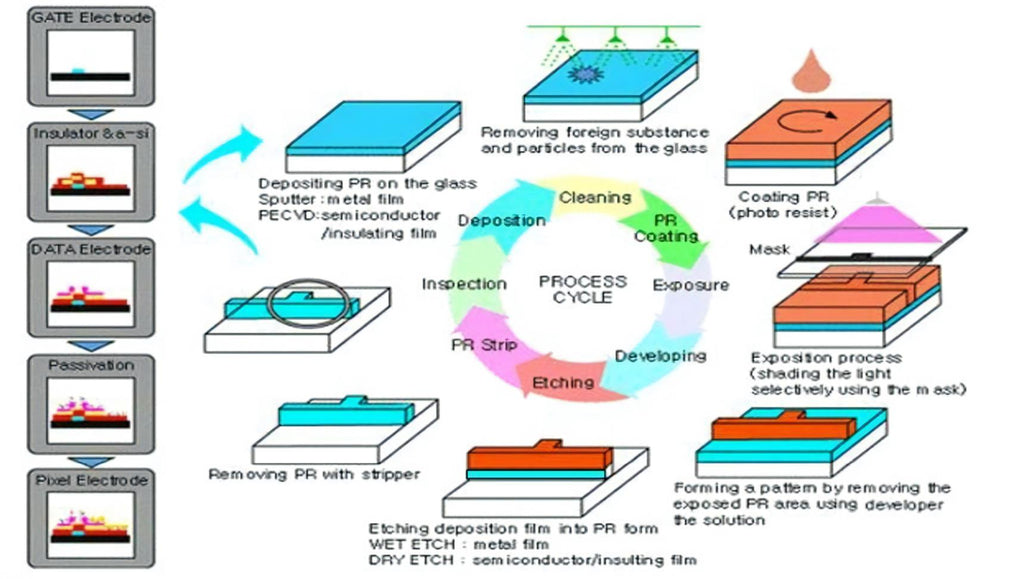
GIN (SiNx / a-Si / n+ a-Si)

S/D Metal (Mo \Al\Mo)
Bildandet av käll- och dräneringselektroder (S/D), dataelektrod och kanal inkluderar specifika procedurer såsom skiktning med molybdennitrid (MoN) och rent aluminium (för käll- och dräneringsutrustning), sputtering av S/D-metallskiktet, S/D-fotolitografi, S/D våtetsning och kanaltorretsning. Genom dessa processer bildas käll- och dräneringselektroderna, kanalen och datalinjerna för TFT på glassubstratet. I detta skede är konstruktionen av TFT avslutad. Den resulterande designen och processen är som följer:
S/D Sputtering: Detta är ett avgörande steg för att bilda käll-/dräneringselektroder. Under denna process bildas ett tätt lager av metallelektroder genom att förstofta tungmetalljoner på substratet.
Rengöring före PR-beläggning: Innan fotoresist appliceras måste substratet rengöras för att avlägsna damm och rester, vilket säkerställer goda beläggningsresultat.
DHP (varm platta): För att bättre fästa fotoresisten på substratet förvärms substratet på en varm platta innan beläggningsprocessen.
Motstå beläggning: Applicera ett lager fotoresist på det förvärmda underlaget, som används för efterföljande mönstring.
Förhärdning (SHP): Det fotoresistbelagda substratet är förhärdat för att göra fotoresisten mer enhetlig och starkare.
Stepperexponering: I det här steget kontrolleras mängden ljusexponering för att härda vissa områden av fotoresisten och skapa det önskade mönstret.
Framkallning: Den exponerade fotoresisten bearbetas för att avslöja mönstret.
Photoresist Post Baking (HHP): Fotoresistmönstret härdas ytterligare och görs mer framträdande genom en annan uppvärmningsprocess. Detta kan också förbättra dess förmåga att motstå kemisk korrosion och slitage.
Utveckla inspektion: Efter utvecklingen behövs en detaljerad inspektion för att säkerställa mönstrets noggrannhet och omedelbart upptäcka och åtgärda eventuella problem.
Våtetsning: Detta är en kemisk reaktionsprocess där en frätande vätska används för att etsa materialet i de icke-skyddade områdena för att bilda kretsmönstret.
Kanal torr etsning: En kanal bildas mellan källan och avloppet. I denna process etsas kislet i kanalområdet till den önskade formen med hjälp av en torretsningsteknik.
Motstå Strip: Slutligen, för att rengöra substratytan, skalas fotoresisten på substratet av.
Efter stegen ovan formas slutligen source/drain-elektroderna, dataelektroderna och TFT-kanalen på glassubstratet.
Passivering (SiNx)
Bildandet av passiveringsskiktet (SiNx), ofta känt som det skyddande isoleringsskiktet, tillsammans med viaorna, inkluderar specifika operationer såsom PECVD-filmbildning, fotolitografi och torretsning för via-skapning. Efter att ha gått igenom dessa procedurer formas slutligen det skyddande isoleringsskiktet för TFT-kanalen och de ledande viaorna på glassubstratet. Bilderna och processen som erhålls efter att dessa steg har slutförts är som följer:
2. Förbeläggningsrengöring - Det är här substratet rengörs före applicering av fotoresist.
3. Förbaka värmeplatta (DHP) - Detta innebär att man använder en värmeplatta för att förvärma substratet för att förbereda för beläggningssteget.
4. Fotoresistbeläggning - Ett lager av fotoresist appliceras över substratet under detta skede.
5. Soft Bake (SHP) - Substratet, belagt med fotoresist, genomgår en förhärdningsprocess för att stelna skiktet.
6. Stepperexponering – Här används stepper litografiteknik för att exponera fotoresisten och forma mönster.
7. Utveckla - Den exponerade fotoresisten bearbetas för att avslöja mönstret.
8. Hårdbaka (HHP) - Fotoresistmönstret härdas genom en efterbakningsbehandling.
9. Inspektion efter utveckling - Det här steget innebär att man inspekterar det utvecklade substratet för att bekräfta mönstrens noggrannhet.
10. Våtetsning - Oönskade tunnfilmsmaterial avlägsnas via en våtkemisk etsningsprocess för att skapa kretsmönster.
11. Avisolering av fotoresist - Fotoresisten tas bort och substratets yta rengörs.
12. Kontakthåletsning (CH Etching) - De erforderliga viaorna bildas genom en torretsningsprocess.
Dessa är de detaljerade stegen som är involverade i att förbereda substratet för TFT-applikationer, vilket leder till skyddet av den aktiva TFT-kanalen och bildandet av ledande vias.
Bildning av transparent pixelelektrod ITO (Indium-Tin-Oxide)
Skapandet av transparenta pixelelektroder i TFT-skärmar är en sofistikerad process som börjar med avsättningen av indium-tenn-oxid (ITO). De involverade stegen är precisionskonstruerade och inkluderar sputtering av ITO-lagret för att uppnå transparens, följt av fotolitografi för intrikat mönstring, och avslutas med våtetsning för att slutföra pixelstrukturen. Denna noggranna sekvens avslutas med bildandet av pixelelektroderna, perfekt integrerade på glassubstratet, vilket markerar det centrala fullbordandet av arrayprocessen. Följande arbetsflöde beskriver förfining och sekvens av operationer efter avslutad process.
Pixel Layer Deposition (ITO Sputtering) – Skapar en transparent ledande film av ITO (Indium Tin Oxide) för efterföljande pixelmönster.
Underlagsrengöring (rengöring av förresistbeläggning) – Säkerställer substratets renhet innan fotoresistmaterialet appliceras.
Underlagsförvärmning (dehydreringsvärmeplatta, DHP) – Förbereder underlaget med ett förgräddningssteg för optimal fotoresistvidhäftning.
Resist Applicering (Beläggning) – Applicerar ett enhetligt fotoresistskikt på underlaget.
Soft Bake (Förhärdning SHP) – Genomför förhärdning för att stelna fotoresisten innan mönstring.
Precisionsexponering (stepperexponering) – Använder stegfotolitografi för att exponera fotoresisten, vilket skapar det önskade mönstret.
Mönsterutveckling (Utveckla) – Utvecklar den exponerade fotoresisten för att avslöja det invecklade pixelmönstret.
Resist Harden (bakning efter exponering, hård bakning HHP) – Härdar den mönstrade fotoresisten för att förbättra etsningsmotståndet.
Mönsterinspektion (inspektion efter utveckling) – Inspekterar de utvecklade mönstren för noggrannhet och integritet.
Mönsteröverföring (ITO Etching) – Överför mönstret genom etsning av ITO-lagret för att bilda pixelelektroder.
Motståndsborttagning (remsa) – Skalar bort fotoresisten och lämnar en ren substratyta.
Prestandaförbättring (glödgning) – Glödgar komponenterna för att förbättra de elektriska egenskaperna hos tunnfilmstransistorerna.
Kvalitetskontroll (TEG-test) – Utför elektriska tester på testelement för att övervaka kvaliteten under produktionen.
Denna strömlinjeformade sekvens lägger grunden för högkvalitativa TFT-skärmar med optimal elektrisk prestanda.

Färgfilter (CF) process
Glassubstrat: Det grundläggande basskiktet som ger mekaniskt stöd.
Black Matrix (BM): Den består av ett ljusabsorberande material och avgränsar varje pixel och minimerar ljusläckage mellan pixlar, vilket förbättrar kontrasten.
Färghartslager: Som de faktiska röda, gröna och blå filtren bestämmer dessa lager pixelfärgerna. De är tillverkade av ett färgat transparent hartsmaterial.
Överlackslager (OC): Ett skyddande lager överlagrat på färghartserna för att jämna ut ytan och skydda filtren från fysiska och kemiska skador.
ITO (Indium Tin Oxide) elektrod: Detta genomskinliga ledande skikt gör att panelen fungerar som en elektrod som reglerar ljuset som passerar igenom.

Förberedelse av underlag: Renheten hos glassubstratet är av största vikt, så det genomgår en grundlig rengöring för att utrota föroreningar som kan äventyra CF-kvaliteten.
Black Matrix Formation: Genom att applicera ett fotoresistskikt på det rengjorda substratet används fotolitografi för att skissera BM-mönstret. Efter exponering avslöjas outvecklade områden och fylls med svart pigment och härdas sedan.
Färghartsapplikation: Successiv applicering av röda, gröna och blå färghartser inom BM-gränserna utförs med användning av en distinkt fotolitografiprocess för varje färgskikt. Efter beläggning och exponering framkallas områdena utan fotoresist och fylls med hartset, följt av härdning.
Applicering av ytskikt: Ett OC-skikt appliceras ovanpå hartsfärgerna för att skydda dem och skapa en slät yta för efterföljande ITO-elektrodavsättning.
ITO elektrodavsättning: Den transparenta ITO-elektroden sputterdeponeras på OC-skiktet och mönstras sedan för att strukturera elektrodarkitekturen.
Inspektion och provning: Genom hela produktionen säkerställer noggranna inspektioner och tester CF-kvalitet. Mätvärden som färgtrohet, enhetlighet och defektnivåer undersöks noggrant.
Integration: Efter kvalitetssäkring är färgfiltret exakt inriktat och laminerat med TFT-LCD-panelkomponenter som TFT-arrayen och flytande kristallskiktet.

CELLsegmentflöde
Produktionsprocessen inom "cell"-aspekten av en TFT-skärm kan grovt delas in i fyra nyckelsteg: Alignment, Boxing, Cutting och Polarisator Attachment. Målen och primära procedurer för dessa stadier beskrivs kortfattat enligt följande:
Anpassningsprocessen
Syftet med Alignment-processen är att skapa ett lager av transparent PI-film (polyimid) på både TFT- och CF-substraten. Genom en efterföljande friktionsprocess påverkar detta lager vätskekristallmolekylerna att riktas in i friktionens riktning. För en djupare förståelse av de bakomliggande principerna bör intresserade läsare hänvisa till relevant litteratur. Därför har detta steg två primära processer: PI-utskrift och gnidning.
PI(Polyimid)Utskrift
Polyimid (PI) är ett högpresterande, transparent organiskt polymermaterial som består av huvud- och sidokedjor. Efter applicering och gräddning fäster den stadigt på CF- och TFT-substratens ytor. Beläggningen av PI använder en speciell djuptrycksteknik. Förutom den primära djuptrycksprocessen, involverar PI-tryckning flera hjälpprocesser inklusive rengöring av substrat före tryckning, förgräddning efter tryckning, automatisk optisk inspektion, härdning, samt en PI-omarbetningsprocess vid behov.
1. Rengöring före PI:Det här steget innebär att substratet rengörs noggrant före utskrift, för att säkerställa att det är fritt från damm, fett och andra föroreningar för att förbereda det för nästa steg.
2.PI-utskrift:Här appliceras PI-materialet (polyimid) på substratet, analogt med att trycka en design på papper, förutom att "bläcket" är ett speciellt material som bildar ett skyddande lager.3.Förbakning:Se detta som en preliminär bakningsfas, som delvis torkar PI-skiktet för att säkerställa korrekt vidhäftning till underlaget.
4.PI-inspektion: Vid denna tidpunkt genomgår de tryckta lagren noggrann undersökning för eventuella fläckar, ojämna områden eller defekter, som liknar att inspektera en målad vägg för brister.
5.PI Omarbetning:Om några problem upptäcks under inspektionen, innebär detta steg att korrigera dessa brister, på samma sätt som att radera misstag på en skiss.
6.PI-härdning: Slutligen är PI-skiktet helt härdat genom en bakningsprocess, ungefär som lera härdas i en ugn, vilket gör den stark och hållbar.
Detta steg syftar till att ta bort damm och partiklar från substratet med hjälp av en ultraljudsrengörare, som använder ultraljudsvågor för grundlig rengöring. Detta säkerställer att substratet är fritt från föroreningar innan du fortsätter till nästa steg.
2. Justering:
Inriktningsfasen justerar substratets orientering för att uppfylla visuella krav. Denna process är enkel och fokuserar på att placera substratet korrekt för efterföljande behandlingar.
3. Gnugga:
Under gnidningsstadiet används en sammetsduk för att gnida över PI-skiktet. Denna åtgärd riktar in PI:s sidokedjor i en enhetlig riktning, organiserar molekylstrukturen för att uppnå de önskade ytegenskaperna.
4. Ultraljudsrengöring efter gnidning (USC):
Efter gnidning kan substratet ha partiklar eller rester. USC-rengöringen efter gnidning tar bort dessa rester, vilket säkerställer att underlagets yta är oklanderligt ren. Detta steg är avgörande för att upprätthålla kvaliteten på den slutliga produkten, eftersom den använder ultraljudsvågor för att avlägsna och ta bort eventuella partiklar eller rester som har fastnat under gnidningsprocessen.

ODF (One Drop Fill) Inkapslingsprocess
1. Applicering av tätningsmedel och silverpasta:UV-härdbart lim används som tätningsmedel, applicerat längs kanterna på CF- och TFT-glasunderlaget, för att säkerställa att de två substraten är ordentligt sammanfogade och för att definiera cellens tjocklek. Samtidigt används silverpasta för att ansluta de vanliga elektroderna på CF och TFT för att säkerställa elektrisk anslutning.
2. Beläggning med flytande kristall:Flytande kristallmaterial släpps på TFT-substratet som redan har belagts med tätningsmedlet. Det flytande kristallmaterialet spelar en avgörande roll i visningsprocessen; den justerar tillståndet för ljuset som passerar genom att ändra dess arrangemang och kontrollerar därigenom färgen och ljusstyrkan på pixlar.
3. Vakuumbindning:CF-substratet, som har belagts med tätningsmedel, silverpasta och flytande kristaller, är sammanfogat med TFT-substratet i en vakuummiljö. Detta steg hjälper till att förhindra bildandet av bubblor och säkerställer att det finns en tät, gapfri bindning mellan de två substraten.
Termisk härdning:Efter att UV-härdningen är klar genomgår substraten en termisk process för att ytterligare stärka tätningsmedlets vidhäftning. Detta steg är särskilt inriktat på områden som inte nås helt av UV-ljus, såsom under kablarna, vilket säkerställer att dessa delar är ordentligt härdade.

1.Skärning
På grund av glassubstratets bestämda storlek och variationen i produktstorlekar arrangeras flera produktceller på ett enda glassubstrat. Skärning utförs genom att skjuta en diamantskiva över glasytan. Det finns vanligtvis en avbindningsprocess efter kapning, men med framsteg inom skärhjulstekniken finns det nu en teknik som skapar ett mycket djupt skärmärke, vilket eliminerar behovet av avbindning.
2. Kantning
Efter att glaset skärs till individuella skärmar har varje skärms kanter många fina sprickor. För att förhindra att dessa sprickor orsakar brott på grund av kollisioner vid efterföljande hantering är kantbehandling nödvändig.
3.Elektrisk mätning
Elektrisk mätning är en hjälpprocess som används flera gånger under produktionen, men det är särskilt viktigt här eftersom det är första gången elektricitet används för att testa LCD-skärmens prestanda. Testprincipen är enkel: applicera elektricitet på individuella bildpixlar och observera cellens displayprestanda genom en polariserande film. Vanligtvis är en kort stång som används för arraytestning elektrifierad. Efter elprovning tas skärmar som inte uppfyller standarder bort för att förhindra materialspill i senare skeden.
Ytterligare hjälpprocesser inkluderar visuell inspektion efter skärning och rengöring efter kanter.
Monteringsprocess för TFT-skärmmodul
De primära processerna som är involverade i monteringen av TFT-displaymoduler inkluderar appliceringen av den polariserande filmen, COG & FPC-bindning, montering och olika stödjande processer. Nedan finns en detaljerad introduktion till var och en:
1.COG & FPC Bonding
COG (Chip on Glass) och FPC (Flexible Printed Circuit) representerar metoder för att ansluta kretsar. På grund av de många elektroderna är traditionella en-till-en trådanslutningar utmanande. Den nuvarande praxisen innebär att man bildar en elektroduppsättning på glaset, med en motsvarande grupp på IC/FPC, och använder anisotropisk ledande film (ACF) för att ansluta varje IC/FPC-elektrod med glaselektroden en efter en.2. Applicera den polariserande filmen
Eftersom LCD-drift är baserad på polariserat ljus är det en viktig process att fästa en polariserande film. Denna film kontrollerar ljuset som passerar genom de flytande kristallcellerna för att producera bilder.
3. Montering
Assembly sammanför bakgrundsbelysningen, skärmen, kontrollkretskortet och andra komponenter som pekskärmar för att bilda en komplett displaymodul. Detta görs vanligtvis manuellt av skickliga tekniker, som spelar en avgörande roll för att säkerställa kvaliteten på de monterade modulerna.
Utöver huvudprocesserna innehåller modulsegmentet flera hjälpprocesser, såsom:
1.Elektrisk mätning med laserskärning och efterskärning
Efter att komponenterna har skurits exakt med laser, testas deras elektriska funktioner för att säkerställa att de uppfyller de erforderliga specifikationerna.2.Bindning och Post-Bonding Elektrisk mätning
Elektrisk testning utförs också efter COG- och FPC-bindningsprocesserna för att verifiera integriteten hos dessa anslutningar.
3. Mikroskopisk inspektion
Efter laserskärning och limning utförs mikroskopiska inspektioner (eller Automated Optical Inspection (AOI) för FPC-limning) för att kontrollera eventuella defekter eller problem.
4.Peel Styrke Test
Efter IC-bindning och FPC-bindning görs skalhållfasthetstest för att utvärdera bindningarnas hållbarhet.
5.Åldrande efter montering
De sammansatta modulerna genomgår en åldringsprocess med kraft pålagd för att säkerställa långsiktig tillförlitlighet.
6. Förpackning och leverans
När modulerna har klarat alla tester och inspektioner paketeras de och skickas till kunden eller nästa produktionsfas.

Senaste artiklarna
-
OLED Technology 2025: Ultimate Guide, Price Analysis, and Future Trends
OLED Technology 2025: Ultimate Guide, Price Analysis, and Future Trends