
TFT LCD-näytön rakenne
Nestekidepaneeli (paneeli): Tämä on näytön pääosa, joka vastaa kuvan esittämisestä. Nestekidepaneeli muodostuu kahdesta lasilevystä, joiden välissä on nestekidekerros, joka tunnetaan nimellä nestekidekenno.
Polarisoivat suodattimet:Nämä komponentit sijaitsevat nestekidekennon molemmilla puolilla, ja niiden tehtävänä on käsitellä kennon läpi kulkevaa valoa.
Värisuodatin: Valmistetaan yleensä yhdelle suljetun nestekidekennon lasilevyistä, tätä käytetään värinäytössä.
Ohutkalvotransistoriryhmä (TFT Array): Suljetun nestekidekennon toiselle lasilevylle sijoitettuna sillä on aktiivinen rooli näytön ohjaamisessa.
Taustavalo:TFT-LCD-näyttömoduulin takana sijaitseva valonlähde tarjoaa valoa, joka tarvitaan näkyvän kuvan tuottamiseen nestekidekennon läpi.
Ulkoisen aseman piiri:Nämä piirit ovat vastuussa tulokuvasignaalien hallinnasta TFT-ryhmän ja taustavalon ohjaamiseksi asianmukaisesti.

TFT-LCD-näyttöjen valmistusprosessi
Filmin muodostuminen: Tekniikat, kuten sputterointi (SPT) ja kemiallinen höyrypinnoitus (CVD), levittävät useita kerroksia alustalle.
Fotolitografia: Fotoresistin levittäminen, valottaminen ja kehittäminen mikrorakenteiden muodostamiseksi.
Etsaus: Märkä- ja kuivaetsausmenetelmät muotoilevat alustaa poistamalla tietyt alueet.
Riisuminen: Kuvioinnin jälkeen ylimääräiset materiaalit poistetaan alustan puhdistamiseksi.
Apuprosessin vaiheet:
Puhdistus:Varmistaa, että alustalla ei ole likaa.
Merkintä ja valotus:Tunnistaa ja valmistelee alustan reunat.
Automatisoitu optinen tarkastus (AOI):Käytetään vikojen tarkastukseen.
Mikroskooppinen tarkastus ja makroskooppinen tarkastus (Mic/Mac):Yksityiskohtien tarkistus.
Elokuvan suorituskyvyn testaus:Käyttää työkaluja, kuten levyresistanssimittareita, profilometrejä, reflektometrejä/ellipsometriaa, Fourier-muunnos infrapunaspektroskopiaa.
Avoin/Short (O/S) sähkötestaus:Tarkistaa piirin jatkuvuuden ja oikosulut.Test Element Group (TEG) Sähkötestaus: Testaa elementtien sähköistä suorituskykyä.
Ryhmän sähkötestaus:Varmistaa ryhmän sähköisen toimivuuden.
Laserkorjaus:Korjaa mahdolliset viat tarkastustulosten mukaan.
Photoresist Rework (PR Rework):Säätää tai toistaa fotolitografiavaiheita tarvittaessa.
Film Rework: Muuttaa tai täydentää kalvonmuodostusprosessia tarvittaessa.

OC-kerros suojaa ja valmistelee värisuodatinkuvioita.
RGB-kerros muodostuminen päällystys-, altistus- ja kehitysjaksojen kautta.
BM (Black Matrix) -kerros parantaa kontrastia ja rajoittaa valovuotoa.
PS (Photo Spacer) -kerros säilyttää tarkan raon substraattien välillä, mikä on ratkaisevan tärkeää kuvanlaadun kannalta.
IT-kerros lisää läpinäkyvän johtavan kalvon sähkönjohtamista ja kosketustoimintoja varten.

Polyimidi (PI) kohdistus ja suuntaus: PI-kerroksen levittäminen ja suuntaaminen nestekidekohdistusta varten.
ODF (optinen näyttökalvo) parantaa visuaalisia tehosteita.
Puhdistus ja rungon tiivistysaine levitys: Valmistellaan nestekidepisaroiden lisäämistä varten.
Nestekide-injektio: Annostelee nestekidettä tarkasti näytölle.
TFT- ja CF-laminointi: TFT- ja CF-komponenttien liittäminen yhteen.
UV-kovettuminen ja lämpökäsittely: Kiinteyttää ja tasaa nestekidettä ultraviolettivalolla ja lämpökäsittelyllä.
Leikkaus, sähkötestaus ja reunojen tasoitus: Alustan muotoilu, sähkötarkistukset ja reunojen tasoitus.
Polarisaattorin kiinnitys ja kuplien poisto: Polarisoivien kalvojen levittäminen ja ilmakuplien poistaminen, tarvittaessa korjaustyöt sallittu.

Laserleikkaus ja sähkötestaus: Varmistaa tarkan muodon ja sähköisen eheyden.
COG (Chip On Glass) -liimaus, FPC (Flexible Printed Circuit) -liimaus ja -testaus: Ajopiirien asennus ja testaus.
Asennus ja sähkötestaus: Kaikkien näyttömoduulien osien yhdistäminen ja lopullisten sähkötestien suorittaminen.
Ikääntyminen: Pitkäaikainen virtalähde tuotteen luotettavuuden varmistamiseksi.
Pakkaus & Toimitus: Valmiin tuotteen valmistelu toimitusta varten.

Taulukon segmenttivirta
G: SiNx:stä (Silicon Nitride) valmistettu portin eriste tarjoaa tarvittavan eristyksen portin ja muiden kerrosten välillä.
I: Kanavakerros, a-Si (amorfinen pii), jossa elektroninen kytkentä tapahtuu.
N: n+ a-Si -kerros on seostettu suurella fosfiinipitoisuudella (PH3). Tämä doping vähentää potentiaalin estettä rajapinnassa varmistaen ohmisen kontaktin, joka on ratkaisevan tärkeä laitteen luotettavan toiminnan kannalta.

Gate Metal (AlNd/MoN)

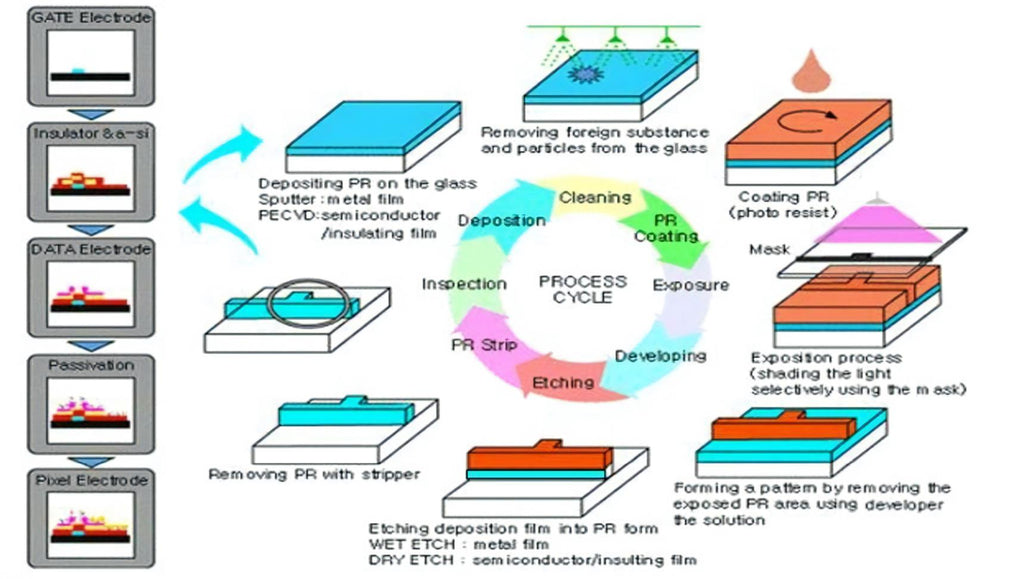
GIN (SiNx / a-Si / n+ a-Si)

S/D-metalli (Mo \Al\Mo)
Lähde- ja tyhjennyselektrodien (S/D), dataelektrodin ja kanavan muodostamiseen sisältyy erityisiä toimenpiteitä, kuten kerrostaminen molybdeeninitridillä (MoN) ja puhtaalla alumiinilla (lähde ja viemäri), S/D-metallikerroksen sputterointi, S/D-fotolitografia, S/D-märkäetsaus ja kanavakuivaetsaus. Näiden prosessien kautta TFT:n lähde- ja tyhjennyselektrodit, kanava ja datalinjat muodostuvat lasisubstraatille. Tässä vaiheessa TFT:n rakentaminen on saatu päätökseen. Tuloksena oleva suunnittelu ja prosessi ovat seuraavat:
S/D Sputtering: Tämä on ratkaiseva vaihe lähde-/tyhjennyselektrodien muodostamisessa. Tämän prosessin aikana muodostuu tiheä metallielektrodien kerros ruiskuttamalla raskasmetalli-ioneja alustalle.
Puhdistus ennen PR-pinnoitusta: Ennen fotoresistin levittämistä alusta on puhdistettava pölyn ja jäännösten poistamiseksi, mikä varmistaa hyvän pinnoitustuloksen.
DHP (keittolevy): Jotta fotoresisti kiinnittyy paremmin alustaan, substraatti esilämmitetään kuumalla levyllä ennen pinnoitusprosessia.
Resist Coating: Levitä kerros fotoresistiä esilämmitetylle alustalle, jota käytetään myöhempään kuviointiin.
Esikovetus (SHP): Fotoresistillä päällystetty substraatti on esikovetettu, jotta fotoresististä tulee tasaisempi ja vahvempi.
Stepper-valotus: Tässä vaiheessa valotuksen määrää säädetään valoresistin tiettyjen alueiden kovettamiseksi ja halutun kuvion luomiseksi.
Kehittyy: Valottunut fotoresisti käsitellään kuvion paljastamiseksi.
Photoresist Post Baking (HHP): Fotoresistikuvio on edelleen kovettunut ja tehty näkyvämmäksi toisen kuumennusprosessin avulla. Tämä voi myös parantaa sen kykyä vastustaa kemiallista korroosiota ja kulumista.
Tarkastuksen kehittäminen: Kehittämisen jälkeen tarvitaan yksityiskohtainen tarkastus kuvion tarkkuuden varmistamiseksi ja mahdollisten ongelmien nopeaan havaitsemiseen ja korjaamiseen.
Märkä Etsaus: Tämä on kemiallinen reaktioprosessi, jossa syövyttävää nestettä käytetään syövyttämään materiaalia suojaamattomilla alueilla piirikuvion muodostamiseksi.
Kanavan kuivaetsaus: Lähteen ja viemärin väliin muodostuu kanava. Tässä prosessissa kanava-alueen pii syövytetään haluttuun muotoon kuivaetsaustekniikalla.
Resist Strip: Lopuksi substraatin pinnan puhdistamiseksi poistetaan alustan fotoresisti.
Yllä olevien vaiheiden jälkeen lähde/tyhjennyselektrodit, dataelektrodit ja TFT:n kanava muodostetaan lopuksi lasisubstraatille.
Passivointi (SiNx)
Passivointikerroksen (SiNx), joka tunnetaan usein suojaavana eristekerroksena, muodostuminen läpivientien kanssa sisältää erityisiä toimenpiteitä, kuten PECVD-kalvon muodostuksen, fotolitografian ja kuivaetsauksen läpivientien luomista varten. Näiden toimenpiteiden jälkeen TFT-kanavan suojaava eristekerros ja johtavat läpivientireiät muodostetaan lopulta lasisubstraatille. Näiden vaiheiden suorittamisen jälkeen saadut kuvat ja prosessi ovat seuraavat:
2. Pinnoitteen esipuhdistus - Tässä alusta puhdistetaan ennen fotoresistin levittämistä.
3. Keittolevy Esipaista (DHP) - Tähän sisältyy keittolevyn käyttö alustan esilämmittämiseen pinnoitusvaiheen valmistelua varten.
4. Valonkestävä pinnoite - Tämän vaiheen aikana alustan päälle levitetään kerros fotoresistiä.
5. Pehmeä paista (SHP) - Fotoresistillä päällystetty substraatti käy läpi esikovetusprosessin kerroksen kiinteyttämiseksi.
6. Stepper Exposure - Tässä käytetään stepper-litografiatekniikkaa valoresistin ja muotokuvioiden paljastamiseen.
7. Kehittyminen - Valottunut fotoresisti käsitellään kuvion paljastamiseksi.
8. Hard Bake (HHP) - Fotoresistikuvio kovettuu jälkileistokäsittelyllä.
9. Kehityksen jälkeinen tarkastus - Tämä vaihe sisältää kehitetyn alustan tarkastamisen kuvioiden tarkkuuden varmistamiseksi.
10. Märkäetsaus - Ei-toivotut ohutkalvomateriaalit poistetaan märkäkemiallisella etsausprosessilla piirikuvioiden luomiseksi.
11. Fotoresist Stripping - Fotoresisti poistetaan ja alustan pinta puhdistetaan.
12. Kontaktireiän etsaus (CH-etsaus) - Tarvittavat läpiviennit muodostetaan kuivaetsausprosessilla.
Nämä ovat yksityiskohtaiset vaiheet, jotka liittyvät substraatin valmisteluun TFT-sovelluksia varten, mikä johtaa aktiivisen TFT-kanavan suojaamiseen ja johtavien läpivientien muodostumiseen.
Läpinäkyvän pikselielektrodin ITO (indium-tina-oksidi) muodostuminen
Läpinäkyvien pikselielektrodien luominen TFT-näytöissä on pitkälle kehitetty prosessi, joka alkaa indium-tinaoksidin (ITO) kerrostamisesta. Vaiheet ovat tarkasti suunniteltuja, ja niihin kuuluu ITO-kerroksen ruiskuttaminen läpinäkyvyyden saavuttamiseksi, jota seuraa fotolitografia monimutkaisen kuvioinnin aikaansaamiseksi ja päättyy märkäsyövytykseen pikselirakenteen viimeistelemiseksi. Tämä huolellinen sekvenssi päättyy pikselielektrodien muodostumiseen, jotka on integroitu virheettömästi lasisubstraattiin, mikä merkitsee ryhmäprosessin keskeistä loppuunsaattamista. Seuraava työnkulku kuvaa tarkennusta ja toimintojen järjestystä prosessin valmistumisen jälkeen.
Pikselikerrospinnoitus (ITO-sputterointi) – Muodostaa läpinäkyvän johtavan kalvon ITO:sta (indium Tin Oxide) myöhempää pikselikuviointia varten.
Alustan puhdistus (Pre-Resist Coating Clean) – Varmistaa alustan puhtauden ennen fotoresistimateriaalin levittämistä.
Alustan esilämmitys (dehydratointilevy, DHP) – Valmistelee alustan esipaistovaiheella optimaalisen fotoresistin kiinnittymisen varmistamiseksi.
Kestää levitystä (pinnoitus) – Levittää tasaisen fotoresistikerroksen alustalle.
Soft Bake (esikovettuva SHP) – Suorittaa esikovettamisen kiinteyttääkseen fotoresistin ennen kuviointia.
Tarkkuusvalotus (Stepper Exposure) – Käyttää stepper-fotolitografiaa valoresistin paljastamiseen ja luo halutun kuvion.
Mallin kehittäminen (kehittäminen) – Kehittää valotetun fotoresistin paljastamaan monimutkaisen pikselikuvion.
Resist Harden (altistuksen jälkeinen paisto, kova paisto HHP) – Kovettaa kuviollisen fotoresistin parantaakseen etsauskestävyyttä.
Kuvion tarkastus (kehityksen jälkeinen tarkastus) – Tarkistaa kehitettyjen mallien tarkkuuden ja eheyden.
Kuvion siirto (ITO-etsaus) – Siirtää kuvion syövyttämällä ITO-kerroksen pikselielektrodien muodostamiseksi.
Resist poistaminen (nauhat) – Poistaa fotoresistin jättäen puhtaan alustapinnan.
Suorituskyvyn parantaminen (hehkutus) – Hehkuttaa komponentit parantaakseen ohutkalvotransistoreiden sähköisiä ominaisuuksia.
Laadunvalvonta (TEG-testi) – Suorittaa testielementtien sähkötestejä laadun valvomiseksi tuotannon aikana.
Tämä virtaviivainen sekvenssi luo pohjan korkealaatuisille TFT-näytöille, joilla on optimaalinen sähköinen suorituskyky.

Color Filter (CF) -prosessi
Lasipohja: Perustuspohja, joka antaa mekaanista tukea.
Musta Matrix (BM): Valmistettu valoa absorboivasta materiaalista, se rajaa jokaisen pikselin ja minimoi pikselien välisen valovuodon, mikä parantaa kontrastia.
Värilliset hartsikerrokset: Varsinaisina punaisen, vihreän ja sinisen värisinä suodattimina nämä tasot määrittävät pikselien värit. Ne on valmistettu värjätystä läpinäkyvästä hartsimateriaalista.
Päällystakkikerros (OC): Suojakerros, joka on päällystetty värihartsien päällä, tasoittaa pintaa ja suojaa suodattimia fyysisiltä ja kemiallisilta haitoilta.
ITO-elektrodi (indiumtinaoksidi): Tämä läpinäkyvä johtava kerros mahdollistaa paneelin toiminnan elektrodina, joka säätelee läpi kulkevaa valoa.

Alustan valmistelu: Lasisubstraatin puhtaus on ensiarvoisen tärkeää, joten se puhdistetaan perusteellisesti CF-laatua heikentävien epäpuhtauksien poistamiseksi.
Mustan matriisin muodostuminen: Kun fotoresistikerros levitetään puhdistetulle alustalle, fotolitografiaa käytetään hahmottamaan BM-kuvio. Altistuksen jälkeen kehittymättömät alueet paljastuvat ja täytetään mustalla pigmentillä, minkä jälkeen ne kovettuvat.
Värihartsisovellus: Punaisten, vihreiden ja sinisten värihartsien peräkkäinen levitys BM-rajojen sisällä suoritetaan käyttämällä erillistä fotolitografiaprosessia jokaiselle värikerrokselle. Päällystyksen ja valotuksen jälkeen alueet, joissa ei ole fotoresistiä, kehitetään ja täytetään hartsilla, minkä jälkeen kovetetaan.
Päällystakkikerroksen levitys: Hartsivärien päälle levitetään OC-kerros suojaamaan niitä ja muodostamaan sileä pinta myöhempää ITO-elektrodipinnoitusta varten.
ITO-elektrodipinnoitus: Läpinäkyvä ITO-elektrodi sputteroidaan OC-kerrokselle ja kuvioillaan sitten elektrodin arkkitehtuurin jäsentämiseksi.
Tarkastus ja testaus: Koko tuotannon ajan huolelliset tarkastukset ja testit varmistavat CF-laadun. Mittarit, kuten värien tarkkuus, tasaisuus ja virhetasot, tutkitaan perusteellisesti.
Integrointi: Laadunvarmistuksen jälkeen värisuodatin on kohdistettu tarkasti ja laminoitu TFT-LCD-paneelin komponenttien, kuten TFT-ryhmän ja nestekidekerroksen, kanssa.

CELL Segment Flow
TFT-näytön "solu"-osion tuotantoprosessi voidaan jakaa karkeasti neljään avainvaiheeseen: kohdistus, nyrkkeily, leikkaus ja polarisaattorin kiinnitys. Näiden vaiheiden tavoitteet ja ensisijaiset menettelytavat on kuvattu lyhyesti seuraavasti:
Kohdistusprosessi
Kohdistusprosessin tavoitteena on luoda kerros läpinäkyvää PI (polyimidi) -kalvoa sekä TFT- että CF-substraateille. Myöhemmän kitkaprosessin kautta tämä kerros vaikuttaa nestekidemolekyyleihin asettumaan kitkan suuntaan. Kiinnostuneiden lukijoiden tulee perehtyä asiaan liittyviin periaatteisiin syvällisemmin. Siksi tässä vaiheessa on näkyvästi kaksi pääprosessia: PI-tulostus ja hankaus.
PI (polyimidi) painatus
Polyimidi (PI) on korkean suorituskyvyn läpinäkyvä orgaaninen polymeerimateriaali, joka koostuu pää- ja sivuketjuista. Levityksen ja paistamisen jälkeen se kiinnittyy tiukasti CF- ja TFT-alustojen pintoihin. PI:n pinnoituksessa käytetään erityistä syväpainotekniikkaa. Ensisijaisen syväpainoprosessin lisäksi PI-tulostukseen kuuluu useita apuprosesseja, kuten alustan puhdistus ennen painatusta, esipaistaminen painatuksen jälkeen, automaattinen optinen tarkastus, kovetus sekä tarvittaessa PI-muokkausprosessi.
1.Pre-PI-puhdistus:Tämä vaihe sisältää alustan perusteellisen puhdistamisen ennen tulostamista varmistaen, että se on vapaa pölystä, rasvasta ja muista epäpuhtauksista, jotta se valmistelee seuraavia vaiheita varten.
2.PI-tulostus: Tässä PI (polyimidi) -materiaalia levitetään alustalle, analogisesti kuvion tulostamiseen paperille, paitsi että "muste" on erityinen materiaali, joka muodostaa suojakerroksen.3. Esileivonta:Pidä tätä alustavana paistovaiheena, joka kuivattaa PI-kerroksen osittain varmistaakseen oikean tarttuvuuden alustaan.
4.PI-tarkastus: Tässä vaiheessa painetut kerrokset tutkitaan tarkasti mahdollisten tahrojen, epätasaisten alueiden tai vikojen varalta, mikä muistuttaa maalatun seinän tarkastamista virheiden varalta.
5.PI Rework:Jos tarkastuksen aikana havaitaan ongelmia, tämä vaihe edellyttää näiden epätäydellisyyksien korjaamista, kuten luonnoksen virheiden poistamista.
6.PI Kovetus: Lopuksi PI-kerros kovettuu täysin paistoprosessissa, aivan kuten savi kovettuu uunissa, mikä tekee siitä vahvan ja kestävän.
Tämä vaihe on tarkoitettu pölyn ja hiukkasten poistamiseen alustalta ultraäänipuhdistimella, joka käyttää ultraääniaaltoja perusteelliseen puhdistukseen. Tämä varmistaa, että alustassa ei ole epäpuhtauksia ennen kuin siirryt seuraaviin vaiheisiin.
2. Kohdistus:
Kohdistusvaihe säätää alustan suunnan vastaamaan visuaalisia vaatimuksia. Tämä prosessi on suoraviivainen, ja siinä keskitytään substraatin oikeaan sijoittamiseen myöhempiä käsittelyjä varten.
3. Hankaus:
Hankausvaiheessa PI-kerroksen yli hierotaan samettikankaalla. Tämä toiminto kohdistaa PI:n sivuketjut yhtenäiseen suuntaan ja järjestää molekyylirakenteen haluttujen pintaominaisuuksien saavuttamiseksi.
4. Hieronnan jälkeinen ultraäänipuhdistus (USC):
Hankaamisen jälkeen alustassa voi olla hiukkasia tai jäämiä. Hieronnan jälkeinen USC-puhdistus poistaa nämä jäännökset varmistaen, että alustan pinta on moitteettoman puhdas. Tämä vaihe on kriittinen lopputuotteen laadun säilyttämiseksi, koska se käyttää ultraääniaaltoja hankausprosessin aikana kiinnittyneiden hiukkasten tai jäännösten irrottamiseen ja poistamiseen.

ODF (One Drop Fill) -kapselointiprosessi
1. Tiivistysaineen ja hopeatahnan käyttö:Tiivisteaineena käytetään UV-kovettuvaa liimaa, joka levitetään CF- ja TFT-lasialustojen reunoja pitkin varmistamaan, että kaksi alustaa ovat tiukasti kiinni, ja määrittää kennon paksuuden. Samanaikaisesti hopeatahnaa käytetään CF:n ja TFT:n yhteisten elektrodien yhdistämiseen sähköliitäntöjen varmistamiseksi.
2. Nestekidepinnoite:Nestekidemateriaalia tiputetaan TFT-substraatille, joka on jo päällystetty tiivisteaineella. Nestekidemateriaalilla on kriittinen rooli näyttöprosessissa; se säätää läpi kulkevan valon tilaa muuttamalla sen järjestelyä, mikä säätelee pikselien väriä ja kirkkautta.
3. Tyhjiölimaus:CF-substraatti, joka on päällystetty tiivisteaineella, hopeatahnalla ja nestekiteellä, liitetään TFT-substraattiin tyhjiöympäristössä. Tämä vaihe auttaa estämään kuplien muodostumista ja varmistaa, että kahden alustan välillä on tiivis, aukoton sidos.
Lämpökovettuminen:Kun UV-kovettuminen on valmis, substraatit käyvät läpi lämpöprosessin, joka vahvistaa tiivisteen tarttuvuutta entisestään. Tämä vaihe on suunnattu erityisesti alueille, joita UV-valo ei täysin tavoita, kuten johtojen alle, mikä varmistaa näiden osien perusteellisen kovettumisen.

1.Leikkaus
Lasisubstraatin määrätyn koon ja tuotekokojen vaihtelun vuoksi yhdelle lasisubstraatille on järjestetty useita tuotekennoja. Leikkaus suoritetaan liu'uttamalla timanttilaikkaa lasipinnan poikki. Leikkauksen jälkeen tapahtuu yleensä sidosten irrotusprosessi, mutta leikkauslaikkateknologian edistymisen myötä on nyt olemassa tekniikka, joka luo erittäin syvän leikkausjäljen, mikä eliminoi sidosten irrottamisen tarpeen.
2. Reunus
Sen jälkeen, kun lasi on leikattu yksittäisiksi näytöiksi, jokaisen näytön reunoissa on monia hienoja halkeamia. Reunojen käsittely on välttämätöntä, jotta nämä halkeamat eivät aiheuta murtumia myöhemmässä käsittelyssä tapahtuvien törmäysten vuoksi.
3. Sähkömittaus
Sähkömittaus on apuprosessi, jota käytetään useita kertoja tuotannon aikana, mutta se on erityisen tärkeä tässä, koska tämä on ensimmäinen kerta, kun sähköä käytetään LCD-näytön suorituskyvyn testaamiseen. Testausperiaate on yksinkertainen: syötä sähköä yksittäisiin näytön pikseleihin ja tarkkaile solun näytön suorituskykyä polarisoivan kalvon läpi. Tyypillisesti ryhmätestaukseen käytetty lyhyt tanko on sähköistetty. Sähkötestauksen jälkeen standardien vastaiset suojukset poistetaan materiaalin tuhlauksen estämiseksi myöhemmissä vaiheissa.
Muita apuprosesseja ovat leikkausjälkeinen silmämääräinen tarkastus ja reunojen jälkipuhdistus.
TFT-näyttömoduulin kokoonpanoprosessi
TFT-näyttömoduulien kokoonpanoon liittyvät ensisijaiset prosessit sisältävät polarisoivan kalvon, COG- ja FPC-sidosten, kokoamisen ja erilaisia tukiprosesseja. Alla on yksityiskohtainen esittely jokaisesta:
1.COG- ja FPC-liimaus
COG (Chip on Glass) ja FPC (Flexible Printed Circuit) edustavat menetelmiä piirien yhdistämiseksi. Elektrodien suuresta määrästä johtuen perinteiset yksi-yhteen johtoliitännät ovat haastavia. Nykyinen käytäntö käsittää elektrodiryhmän muodostamisen lasille, vastaavan ryhmän IC/FPC:lle ja anisotrooppisen johtavan kalvon (ACF) käyttämisen jokaisen IC/FPC-elektrodin yhdistämiseksi lasielektrodiin yksitellen.2. Polarisoivan kalvon kiinnittäminen
Koska LCD-näytön toiminta perustuu polarisoituun valoon, polarisoivan kalvon kiinnittäminen on olennainen prosessi. Tämä kalvo ohjaa nestekidekennojen läpi kulkevaa valoa kuvien tuottamiseksi.
3. Kokoonpano
Assembly yhdistää taustavalon, näytön, ohjauspiirilevyn ja muut komponentit, kuten kosketusnäytöt, muodostamaan täydellisen näyttömoduulin. Tämän tekevät tyypillisesti ammattitaitoiset teknikot, joilla on ratkaiseva rooli koottujen moduulien laadun varmistamisessa.
Pääprosessien lisäksi moduulisegmentti sisältää useita apuprosesseja, kuten:
1.Laserleikkaus ja leikkauksen jälkeinen sähkömittaus
Kun komponentit on leikattu tarkasti laserilla, niiden sähköiset toiminnot testataan sen varmistamiseksi, että ne täyttävät vaaditut vaatimukset.2. Liimaus ja liimauksen jälkeinen sähkömittaus
Sähkötestaus suoritetaan myös COG- ja FPC-sidosprosessien jälkeen näiden liitäntöjen eheyden varmistamiseksi.
3. Mikroskooppinen tarkastus
Laserleikkauksen ja liimauksen jälkeen suoritetaan mikroskooppiset tarkastukset (tai automaattinen optinen tarkastus (AOI) FPC-sidokselle) mahdollisten vikojen tai ongelmien tarkistamiseksi.
4. Kuorinnan lujuustesti
IC-sidoksen ja FPC-sidoksen jälkeen tehdään kuoriutumislujuustestit sidosten kestävyyden arvioimiseksi.
5. Ikääntyminen kokoonpanon jälkeen
Kootut moduulit läpikäyvät vanhenemisprosessin teholla, joka varmistaa pitkän aikavälin luotettavuuden.
6. Pakkaus ja lähetys
Kun moduulit läpäisevät kaikki testit ja tarkastukset, ne pakataan ja lähetetään asiakkaalle tai seuraavaan tuotantovaiheeseen.

Latest articles
-
OLED Technology 2025: Ultimate Guide, Price Analysis, and Future Trends
OLED Technology 2025: Ultimate Guide, Price Analysis, and Future Trends